往复式整筒抽油泵检测的重要性与实施要点
往复式整筒抽油泵作为石油开采中举升系统的核心设备,其性能直接关系到油井产量、能耗效率和设备使用寿命。由于长期处于高温、高压、腐蚀性介质等复杂工况下,泵体易出现磨损、变形、密封失效等问题。通过系统化的检测项目能够精准评估设备状态,预防突发故障,降低维护成本。本文将从结构特点出发,深入解析抽油泵检测的关键指标及实施规范,为油田运维提供技术参考。
核心检测项目分类与标准
1. 外观完整性检测:采用目视检查与工业内窥镜相结合的方式,重点检测泵筒内壁划痕(深度不超过0.05mm)、柱塞表面镀层脱落(面积≤5%)、阀座密封面腐蚀等缺陷。需按照SY/T 5059标准对缺陷进行分级判定。
2. 尺寸精度检测:使用三坐标测量仪对关键尺寸进行精密测量,包括: - 泵筒内径公差(H8级别) - 柱塞与泵筒配合间隙(0.03-0.12mm) - 阀球圆度误差(≤0.01mm) - 阀座平面度偏差(≤0.02mm/100mm)
3. 密封性能测试:在专用液压试验台上模拟工作压力(最高35MPa),检测内容涵盖: - 柱塞-泵筒动态泄漏量(≤0.5L/min) - 固定阀/游动阀密封时效(保压10分钟压降≤5%) - 螺纹连接处渗漏情况
材料性能与失效分析
4. 材质验证检测:通过光谱分析确认泵筒(38CrMoAlA)、柱塞(20CrNiMo)等部件的材料成分,使用显微硬度计检测表面硬化层深度(≥0.3mm)。金相组织分析可发现热处理缺陷,如脱碳层、晶间腐蚀等异常现象。
5. 耐磨层评估:针对镀铬/渗氮处理的柱塞表面,采用涡流测厚仪检测镀层厚度(0.10-0.15mm),划格法测试镀层结合强度(达到GB/T 5270 1级标准)。
动态性能与可靠性验证
6. 模拟工况试验:在闭环试验系统中实现: - 不同冲次(5-15次/分钟)下的容积效率测试 - 含砂介质(粒径≤0.1mm,浓度≤0.5%)磨蚀试验 - 交变载荷(最大悬点载荷±10%)疲劳测试
7. 振动特性分析:安装加速度传感器监测泵体振动频谱,重点识别: - 柱塞偏磨引发的低频振动(<50Hz) - 阀球冲击产生的高频谐波(>500Hz) - 共振频率点偏移量(≤5%)
检测周期与数据管理
建议采用三级检测制度:日常巡检(每72小时)、预防性检测(每6000小时)、大修期全面检测。建立检测数据库,运用趋势分析算法预测剩余寿命,当柱塞间隙增速超过0.02mm/1000小时或容积效率低于75%时,应触发预警机制。
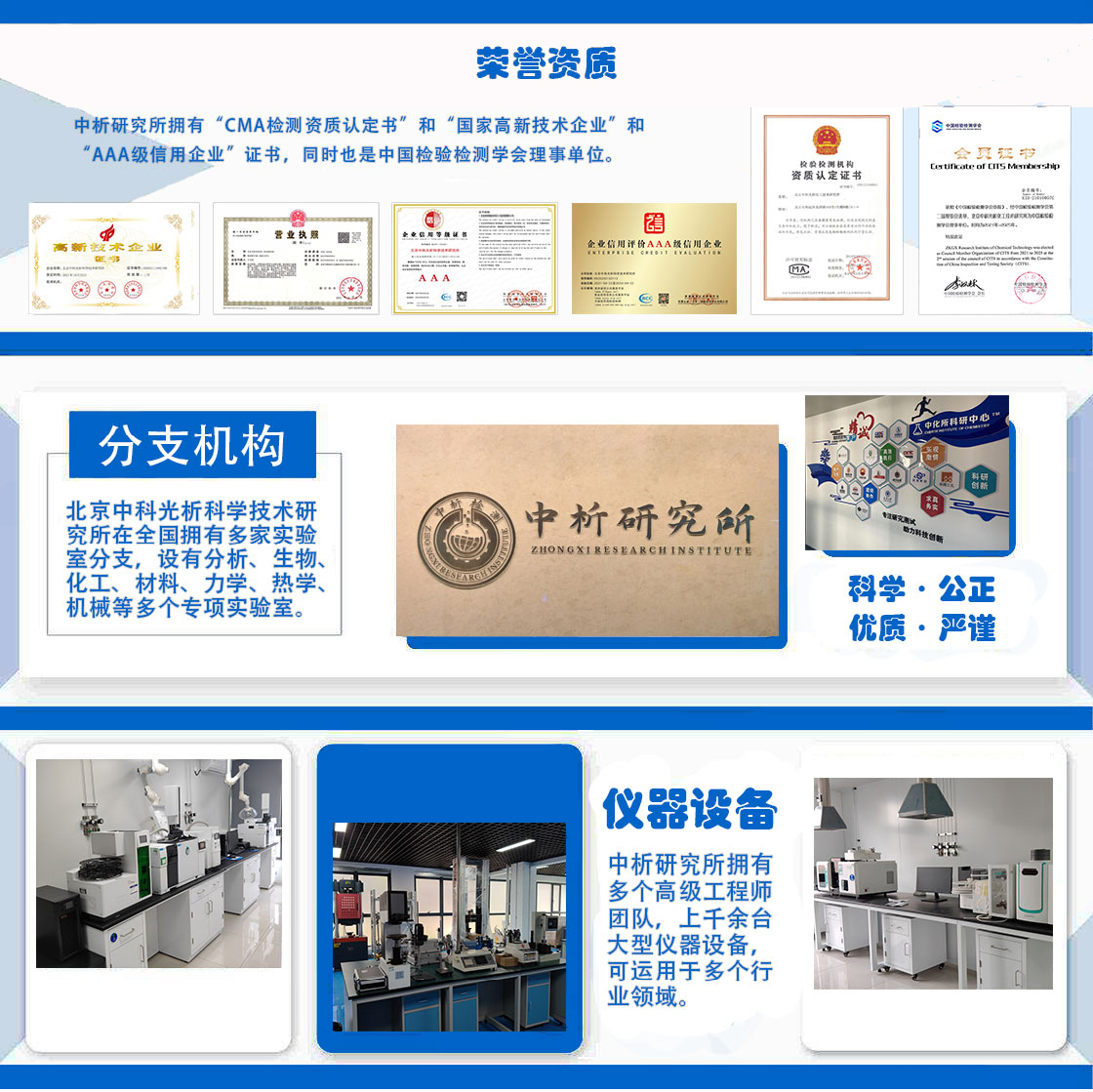
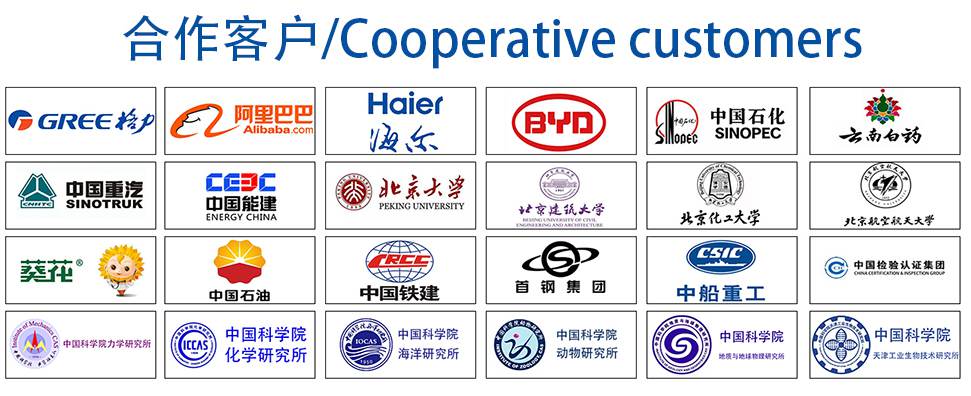