连续抽油杆检测的重要性与挑战
连续抽油杆作为石油开采中的核心部件,其性能直接关系到油井作业效率与设备安全性。与传统分体式抽油杆相比,连续抽油杆具有长度可调、应力分布均匀、疲劳寿命长等优势,但同时也面临更复杂的服役环境和更高的质量要求。由于长期承受交变载荷、腐蚀介质和复杂地质条件的影响,连续抽油杆易出现裂纹、磨损、腐蚀及形变等问题。因此,系统化的检测项目成为保障其可靠性、延长使用寿命的关键环节。当前行业已形成涵盖材料性能、几何结构、表面质量及动态特性的多维检测体系,旨在早期发现潜在缺陷,避免因失效导致的停机事故和经济损失。
关键检测项目分类
1. 表面质量检测
通过目视检查、磁粉探伤或涡流检测技术,排查抽油杆表面划痕、凹坑、氧化皮及裂纹等缺陷。重点检查杆体与接箍连接处、弯曲部位的应力集中区,确保表面光洁度符合SY/T 5550标准中Ra≤6.3μm的要求。
2. 力学性能检测
包括拉伸试验(测定抗拉强度≥965MPa、屈服强度≥862MPa)、冲击韧性测试(-20℃下夏比冲击功≥27J)及疲劳寿命试验(模拟实际工况下循环次数≥10^7次)。通过万能试验机和高频疲劳试验机验证材料性能指标是否达到API 11C规范。
3. 尺寸精度检测
使用激光扫描仪或三坐标测量仪对杆体直径(公差±0.1mm)、直线度(≤0.5mm/m)、椭圆度(≤0.05mm)进行精确测量,确保抽油杆在连续作业中的顺畅运行和密封性能。
4. 耐腐蚀性能检测
依据NACE TM0177标准开展硫化氢应力腐蚀试验,评估材料在含H₂S介质中的抗硫化物应力开裂(SSC)能力。同时进行盐雾试验(72小时)和电化学腐蚀速率测定,验证防腐涂层与基体材料的协同防护效果。
5. 焊缝质量检测
针对连续抽油杆的闪光对焊接头,采用超声波探伤(UT)和射线检测(RT)技术检测未熔合、气孔、夹渣等缺陷,焊缝强度需达到母材强度的95%以上,并满足ISO 13679规定的密封性要求。
6. 动态特性检测
通过振动模态分析仪测试抽油杆的固有频率、阻尼比和振型,结合有限元仿真验证其动态响应特性,预防共振导致的早期失效。同时监测作业时的实际应力分布,优化杆柱组合设计。
检测方法与技术发展
当前检测技术正朝着智能化、在线化方向发展:引入机器视觉实现表面缺陷自动识别,应用光纤光栅传感器实时监测应变分布,结合大数据分析预测剩余寿命。检测周期从传统停机检修缩短至在线连续监测,检测精度提升至微米级,显著提高了故障预警能力。
行业标准与检测意义
检测工作需严格遵循API Spec 11C、SY/T 5550-2018等标准体系。系统化的检测不仅能避免因抽油杆断裂导致的油井停产(单井日均损失可达数万元),还可延长杆体使用寿命30%以上,同时为优化杆柱设计、改进制造工艺提供数据支撑,推动石油装备技术向高效智能化方向发展。
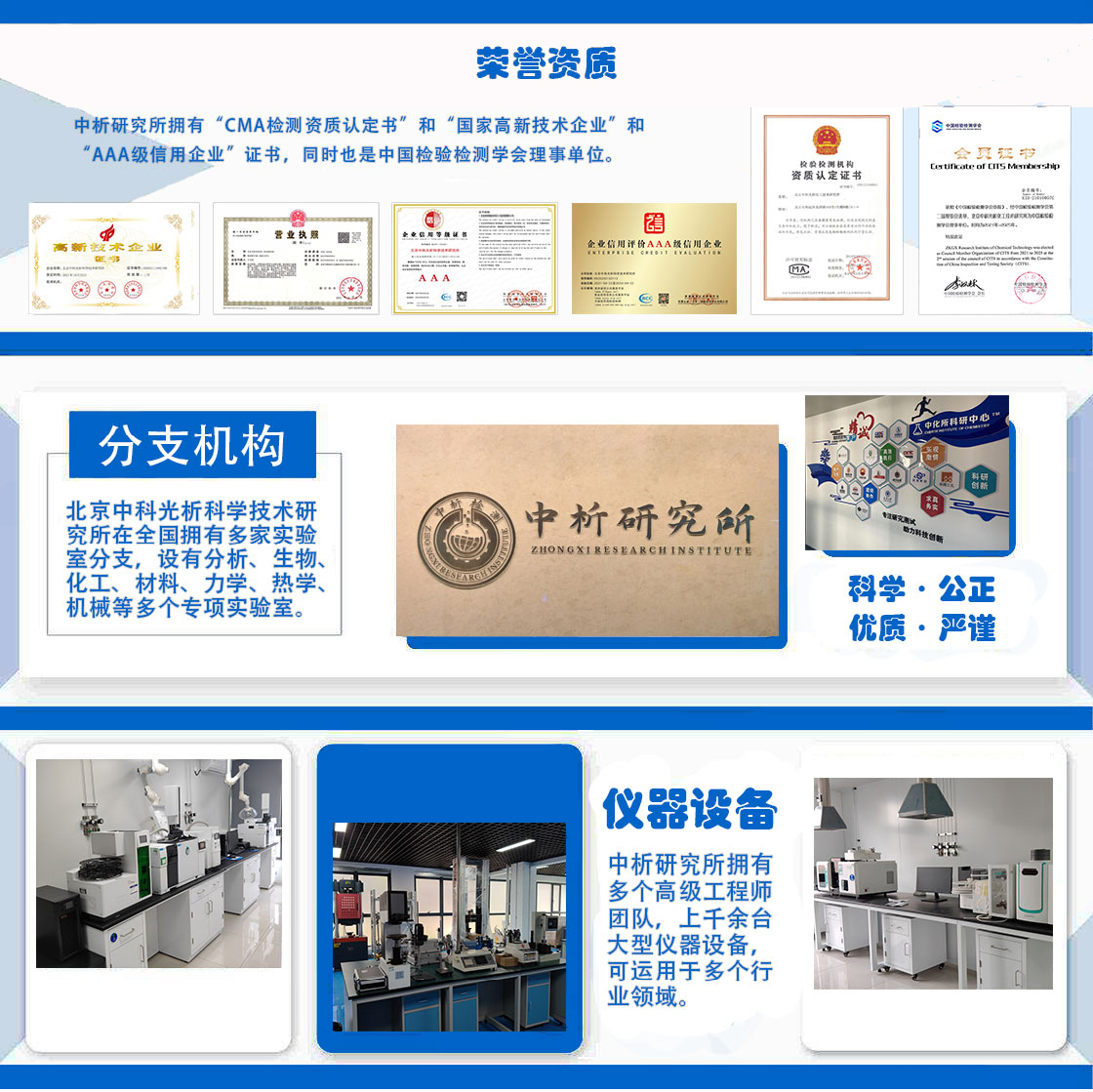
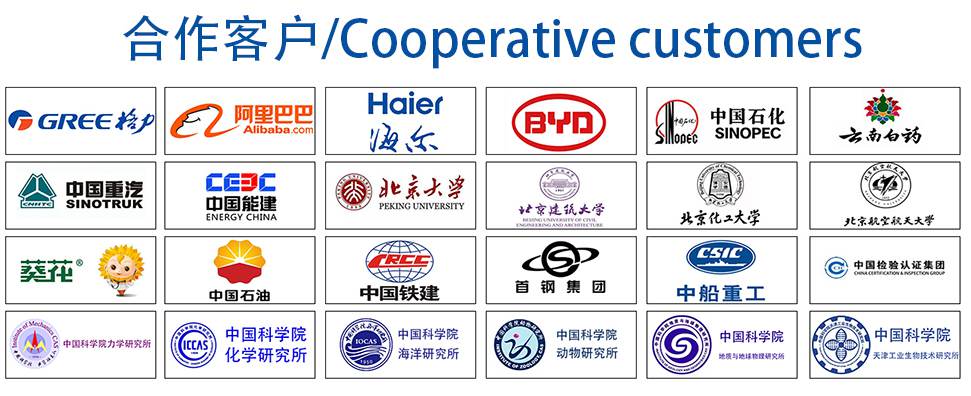