制动片检测:保障行车安全的核心环节
作为车辆制动系统的核心部件,制动片的质量直接影响着刹车性能与行车安全。据统计,每年约23%的交通事故与制动系统故障相关,其中制动片异常磨损占比高达68%。专业规范的制动片检测不仅能预防刹车失效风险,更能通过科学评估延长配件使用寿命。现代检测技术已从传统目视检查发展为多维度综合分析,涵盖物理性能、材料特性及工况模拟等多个层面。
关键检测项目解析
1. 厚度测量与磨损评估
使用激光测厚仪进行三维扫描,精确测量摩擦材料剩余厚度。根据SAE J866标准,当厚度低于原厂规格50%或3mm(以先到者为准)时,必须强制更换。同时检测磨损槽形态,判断是否存在偏磨现象。
2. 摩擦材料成分分析
采用X射线荧光光谱仪(XRF)检测配方比例,重点监控石棉、铜含量等环保指标。通过热重分析(TGA)测定有机粘合剂热分解温度,确保材料在650℃高温下仍能保持稳定摩擦系数。
3. 力学性能测试
包括:
- 剪切强度测试:模拟紧急制动时10-12MPa冲击载荷
- 压缩弹性模量检测:确保在0.5-1.5GPa合理区间
- 洛氏硬度测定:控制在HRB 85-100最佳范围
4. 动态摩擦特性检测
在惯性试验台模拟不同工况:
- 常温(100℃)摩擦系数需保持0.35±0.05
- 高温(350℃)衰减率不超过初始值的25%
- 水湿状态恢复时间<3次制动循环
5. NVH性能验证
通过振动加速度传感器和声学摄像头,检测制动噪声频段。要求:
- 低频振动(1-5kHz)加速度<3.5m/s²
- 高频尖叫(8-16kHz)声压级<72dB(A)
智能检测技术突破
新型AI视觉系统可自动识别摩擦材料表面裂纹(识别精度达0.02mm),而车载传感器可实时监测制动片温度梯度(采样频率100Hz)。这些技术使预防性维护响应时间缩短40%,大幅提升检测效率与准确性。
行业标准与检测周期
建议每10,000公里或6个月进行专业检测,重点车辆(如商用车)应缩短至5,000公里。检测需符合GB/T 34422-2017和ECE R90标准要求,特别关注环保法规对铜含量(<0.5%)的限制要求。
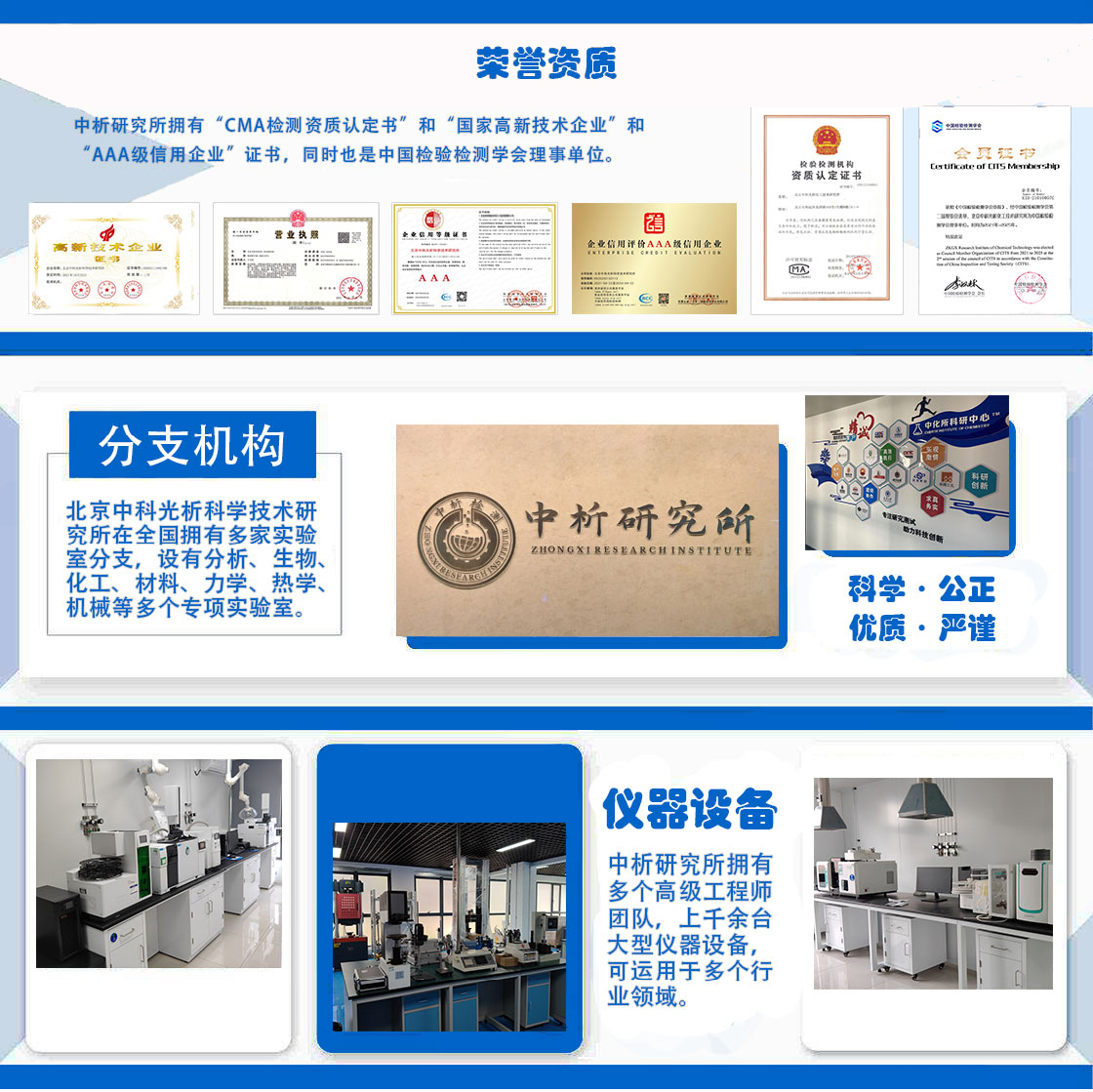
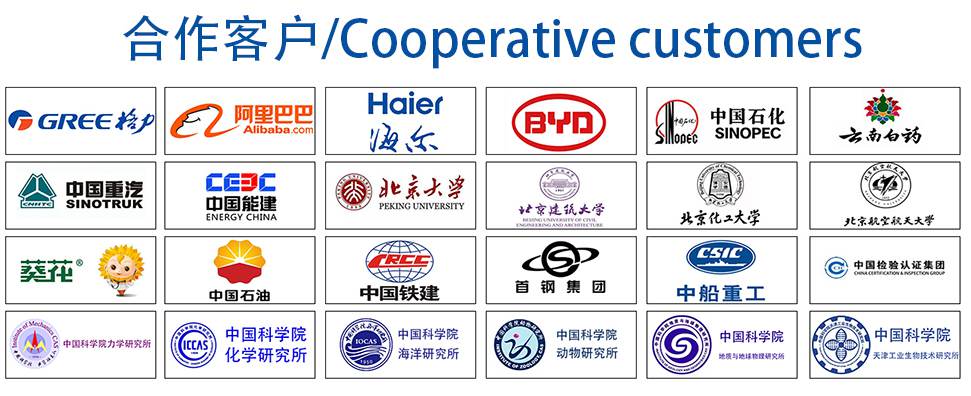