空气制动软管和软管组合件检测的重要性
空气制动系统是商用车、轨道交通及工程机械等领域的核心安全装置,其性能直接影响车辆的制动效果与运行安全。作为系统中的关键组件,空气制动软管和软管组合件承担着传递压缩空气、保障制动响应的重要功能。然而,长期使用中软管可能因老化、磨损、化学腐蚀或机械损伤导致漏气、破裂等问题,进而引发制动失效等重大安全隐患。因此,定期对空气制动软管及组合件进行系统性检测,既是行业标准(如GB/T 7128、ISO 7628)的强制要求,也是保障车辆安全运营的核心环节。
检测过程需覆盖物理性能、耐久性、环境适应性等多维度指标,确保软管在极端温度、压力波动、动态弯曲等复杂工况下仍能稳定工作。同时,随着新能源汽车和智能驾驶技术的发展,对制动系统的可靠性提出了更高要求,检测技术的精准性和全面性显得尤为重要。
空气制动软管和软管组合件检测的核心项目
1. 外观与尺寸检测
通过目视检查软管表面是否存在裂纹、气泡、异物嵌入或局部变形,并测量内径、外径、长度等关键尺寸是否符合设计公差要求。例如,软管内径偏差超过±0.5mm可能导致空气流量异常,影响制动响应速度。
2. 耐压性能测试
模拟实际工况下的压力负载,对软管进行静压试验(如额定工作压力的1.5倍)和脉冲压力试验(频率2Hz,循环次数≥20万次),检测其抗爆破能力及长期承压稳定性。试验后软管不得出现渗漏或结构损伤。
3. 气密性验证
在软管内部充入规定压力的气体(通常为0.8-1.2MPa),通过浸水法或气体流量计检测泄漏量。要求静态泄漏率≤0.1mL/min,动态泄漏率(弯曲状态下)≤0.3mL/min,确保密封性能达标。
4. 耐温与耐候性试验
将软管置于高温(120℃±2℃)、低温(-40℃±2℃)环境中进行循环测试,观察其柔韧性变化及是否出现硬化、龟裂现象。同时通过紫外线加速老化试验评估长期户外使用的抗老化能力。
5. 动态弯曲疲劳测试
模拟车辆行驶中软管的弯曲运动,利用专用设备以固定频率(如2Hz)反复弯折软管,记录其达到规定循环次数(如50万次)后的破损情况,评估抗疲劳性能。
6. 耐化学腐蚀检测
将软管浸泡于制动液、润滑油、盐雾等介质中48小时,检测其质量变化率(≤5%)及表面是否发生溶胀、分层等异常,验证材料的环境适应性。
7. 接头连接强度测试
对软管组合件的接头部位进行轴向拉伸、扭转试验,检测其抗拉强度(≥软管爆破压力的70%)和抗扭力矩(≥设计值的1.2倍),确保连接可靠性。
检测标准与实施建议
检测需
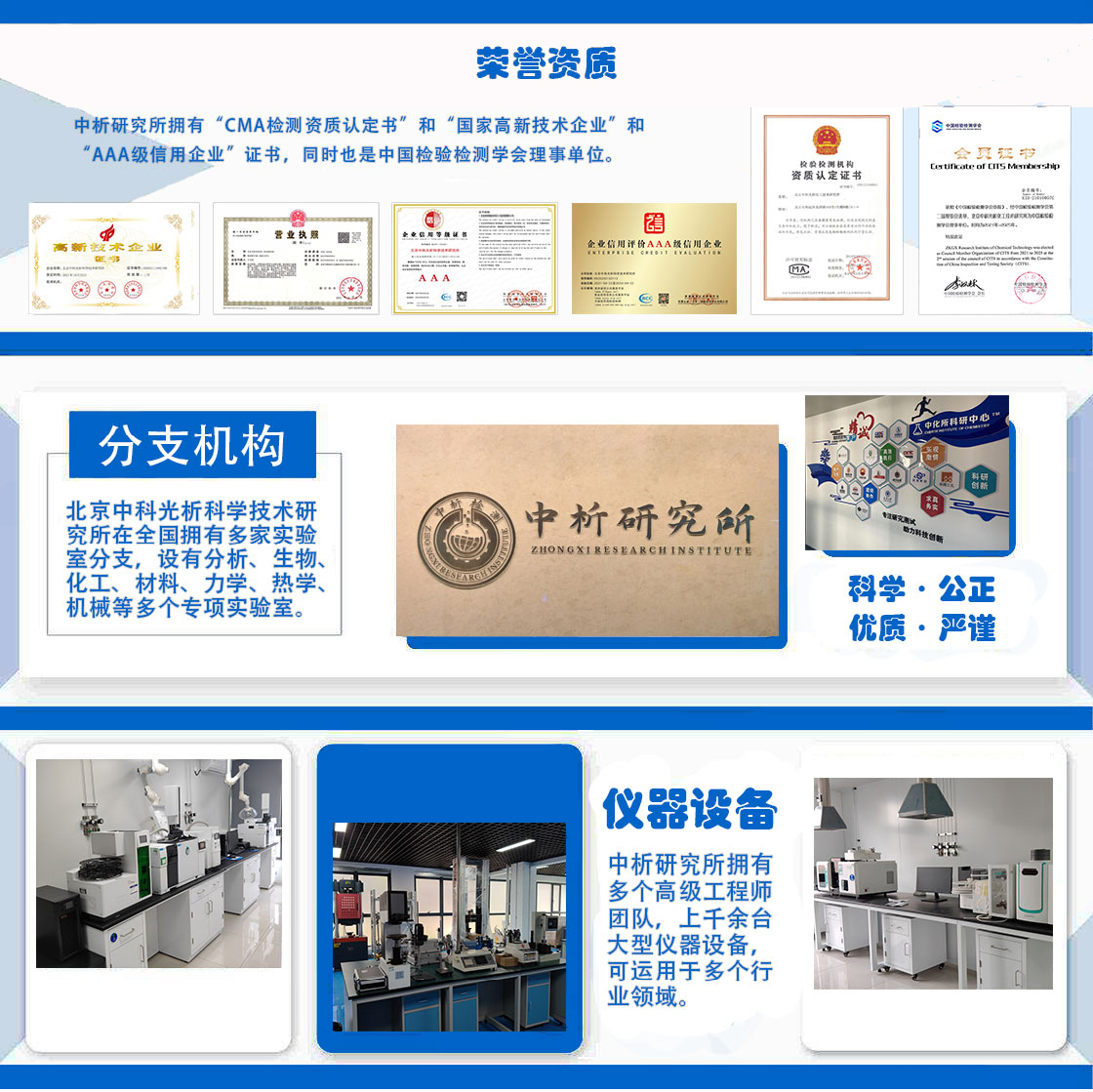
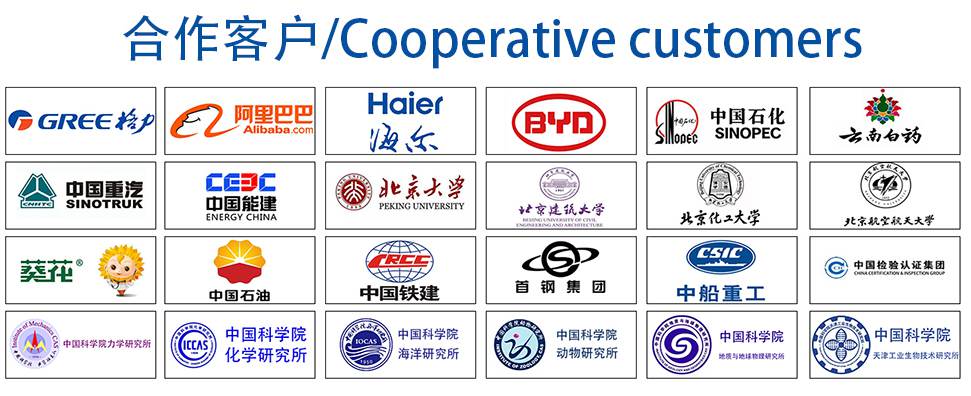