铸件检测:保障工业基础件的核心质量
铸件作为机械制造、汽车工业、能源装备等领域的关键基础部件,其质量直接影响设备的安全性、稳定性和使用寿命。在铸造过程中,受原材料配比、工艺参数、模具设计等多重因素影响,铸件可能出现气孔、缩松、裂纹、夹杂物等多种缺陷。铸件检测通过系统化的技术手段对产品进行全方位质量评估,是工业制造中不可或缺的环节。据统计,每年因铸件质量问题引发的设备失效事故中,70%以上可通过有效检测提前规避。随着智能制造技术的发展,现代铸件检测已形成从传统目视检测到智能化三维扫描的完整技术体系。
核心检测项目与技术解析
1. 外观质量检测
采用目视检测与光学测量相结合的方式,通过工业内窥镜、表面粗糙度仪等设备,检查铸件表面是否存在裂纹、冷隔、粘砂等缺陷。新型结构光扫描技术可实现0.05mm精度的三维形貌重建,精准识别表面凹陷或凸起。
2. 内部缺陷检测
运用X射线探伤(DR检测)、超声波探伤(UT)、工业CT等无损检测技术,可穿透铸件本体检测内部气孔、缩孔、夹杂物的位置和尺寸。其中微焦点CT的分辨率可达5μm,能清晰呈现复杂腔体内部结构。
3. 尺寸精度检测
使用三坐标测量机(CMM)配合激光跟踪仪,对关键配合尺寸、形位公差进行精密测量。针对大型铸件,全站仪与摄影测量系统的组合方案可实现±0.1mm/m的测量精度,满足风电铸件等超大部件的检测需求。
4. 材料性能检测
通过光谱分析仪进行化学成分检测,结合金相显微镜观察微观组织,确保材料符合牌号要求。力学性能测试包括拉伸试验(检测抗拉强度、屈服强度)、冲击试验(检测韧性)、布氏硬度测试等系列项目。
5. 特殊环境适应性检测
对高温/低温服役铸件进行热疲劳试验,通过循环升降温模拟实际工况。耐腐蚀检测采用盐雾试验箱、电化学工作站等设备,评估铸件在特定介质中的抗蚀能力。
智能化检测技术发展趋势
基于机器视觉的AI缺陷识别系统已实现每分钟200个铸件的在线检测,误判率低于0.3%。数字孪生技术可将检测数据实时映射到虚拟模型,实现质量问题的预测性分析。随着ISO 4990等国际标准的更新,铸件检测正向着自动化、数字化、标准化的方向发展。
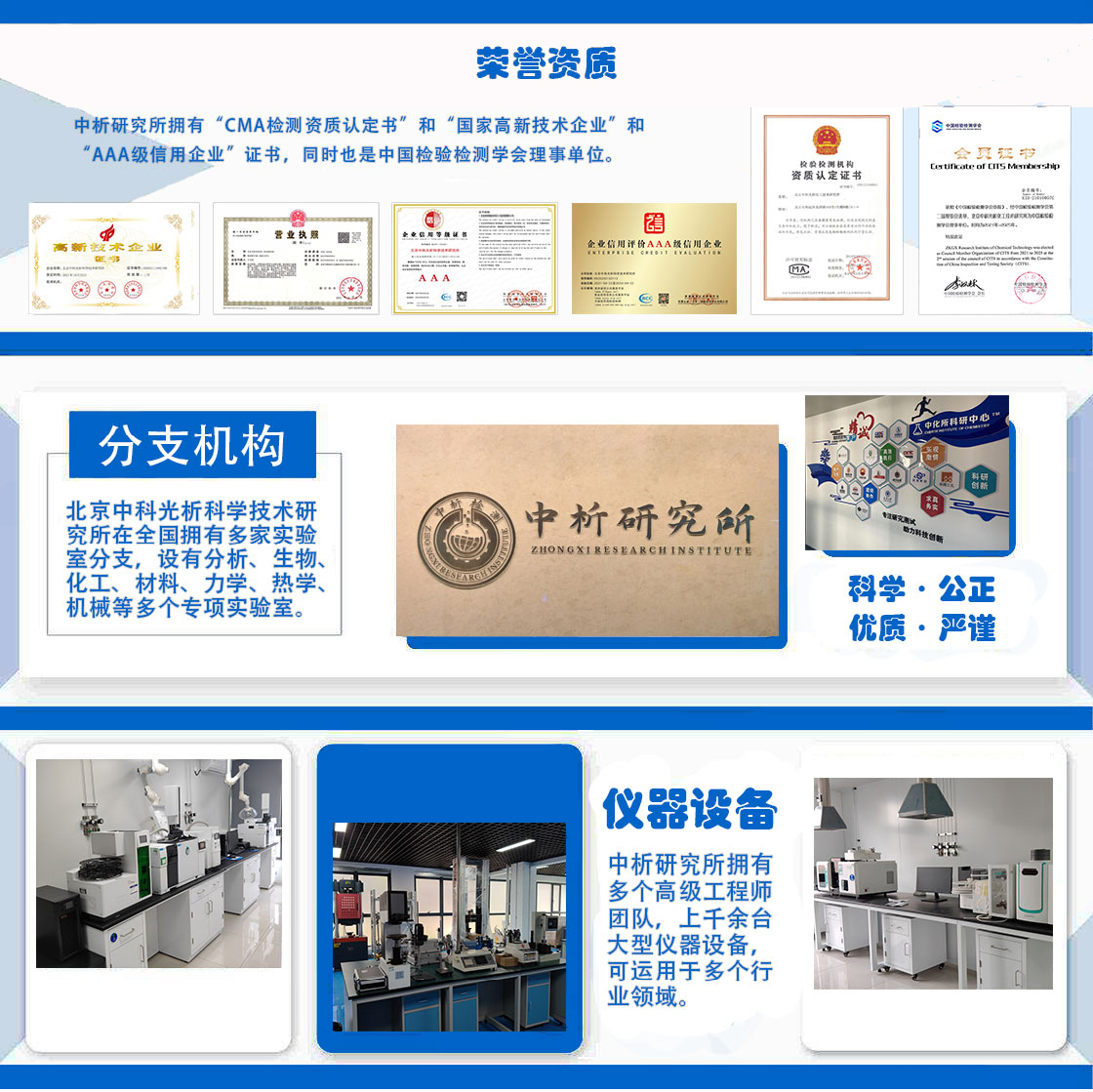
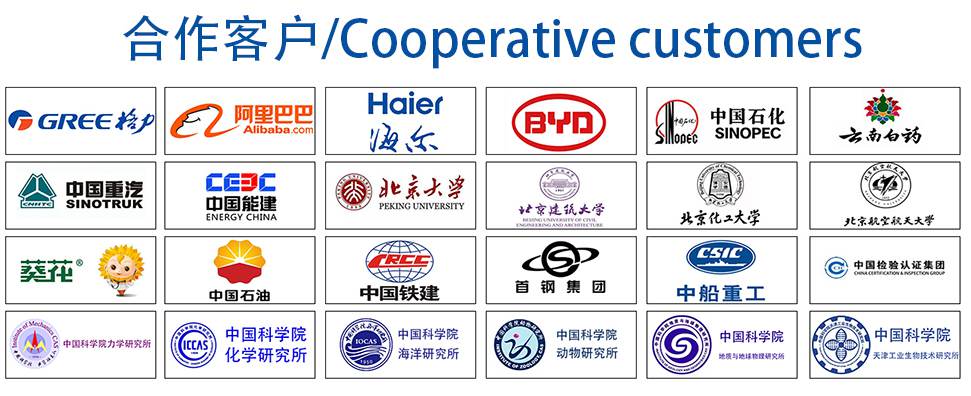