钢材及焊接材料检测的重要性与核心内容
在现代工业制造、建筑工程和装备制造领域,钢材及焊接材料作为基础性原材料,其质量直接关系到工程的安全性、耐久性和功能性。钢材需具备高强度、耐腐蚀性及可加工性,而焊接材料的性能则直接影响焊接接头的可靠性和结构稳定性。因此,通过科学系统的检测项目对钢材及焊接材料的理化性能、力学性能及工艺适应性进行全面评估,是保障工程质量的核心环节。检测过程需严格遵循国家标准(如GB/T)、行业规范(如JB/T)或国际标准(如ISO、ASTM),确保材料从生产到应用的每个环节均符合设计要求。
钢材检测的主要项目
1. 理化性能检测:包括抗拉强度、屈服强度、延伸率、冲击韧性等力学性能测试,以及硬度、金相组织分析。通过万能试验机、冲击试验机等设备验证钢材的承载能力和变形特性。
2. 化学成分分析:采用光谱仪、碳硫分析仪等设备检测钢材中碳、硅、锰、硫、磷等元素的含量,确保材料成分符合牌号要求,避免杂质超标影响性能。
3. 无损检测(NDT):利用超声波探伤(UT)、磁粉探伤(MT)、渗透探伤(PT)等技术检测钢材表面及内部缺陷(如裂纹、气孔、夹渣),判定材料内部结构的完整性。
4. 耐腐蚀性测试:通过盐雾试验、晶间腐蚀试验等方法评估钢材在特定环境下的抗腐蚀能力,尤其适用于海洋工程、化工设备等场景。
焊接材料检测的核心项目
1. 焊条/焊丝成分检测:对焊材的合金元素、药皮成分进行定量分析,确保其与母材的相容性及焊接工艺稳定性。
2. 焊缝力学性能测试:包括焊接接头的拉伸、弯曲、冲击试验,以及宏观/微观金相检验,验证焊缝强度、延展性及是否存在未熔合、气孔等缺陷。
3. 扩散氢含量测定:通过甘油法或气相色谱法检测焊材中的氢含量,预防焊接冷裂纹的产生,尤其对低合金高强钢焊接至关重要。
4. 工艺适应性评价:模拟实际工况进行焊接工艺评定(WPS/PQR),测试焊材在不同电流、电压、预热温度下的熔敷效率和成形质量。
检测标准与认证要求
钢材及焊接材料检测需依据具体应用场景选择标准。例如:建筑钢结构参考GB/T 700、GB/T 1591;压力容器用钢遵循GB/T 713;焊接材料检测则适用GB/T 5117(焊条)、GB/T 5293(埋弧焊丝)。国际项目中常采用AWS(美国焊接学会)或EN(欧洲标准)系列规范。通过检测的材料可获得CMA/ 认证报告,为产品进入市场提供技术背书。
结语
钢材及焊接材料的检测体系覆盖了从原材料到成品的全生命周期质量控制,通过多维度、多手段的检测项目,能够有效识别潜在风险,优化材料选型与工艺设计。企业需建立完善的检测流程,结合第三方权威机构验证,确保材料性能满足工程需求,为行业高质量发展提供技术保障。
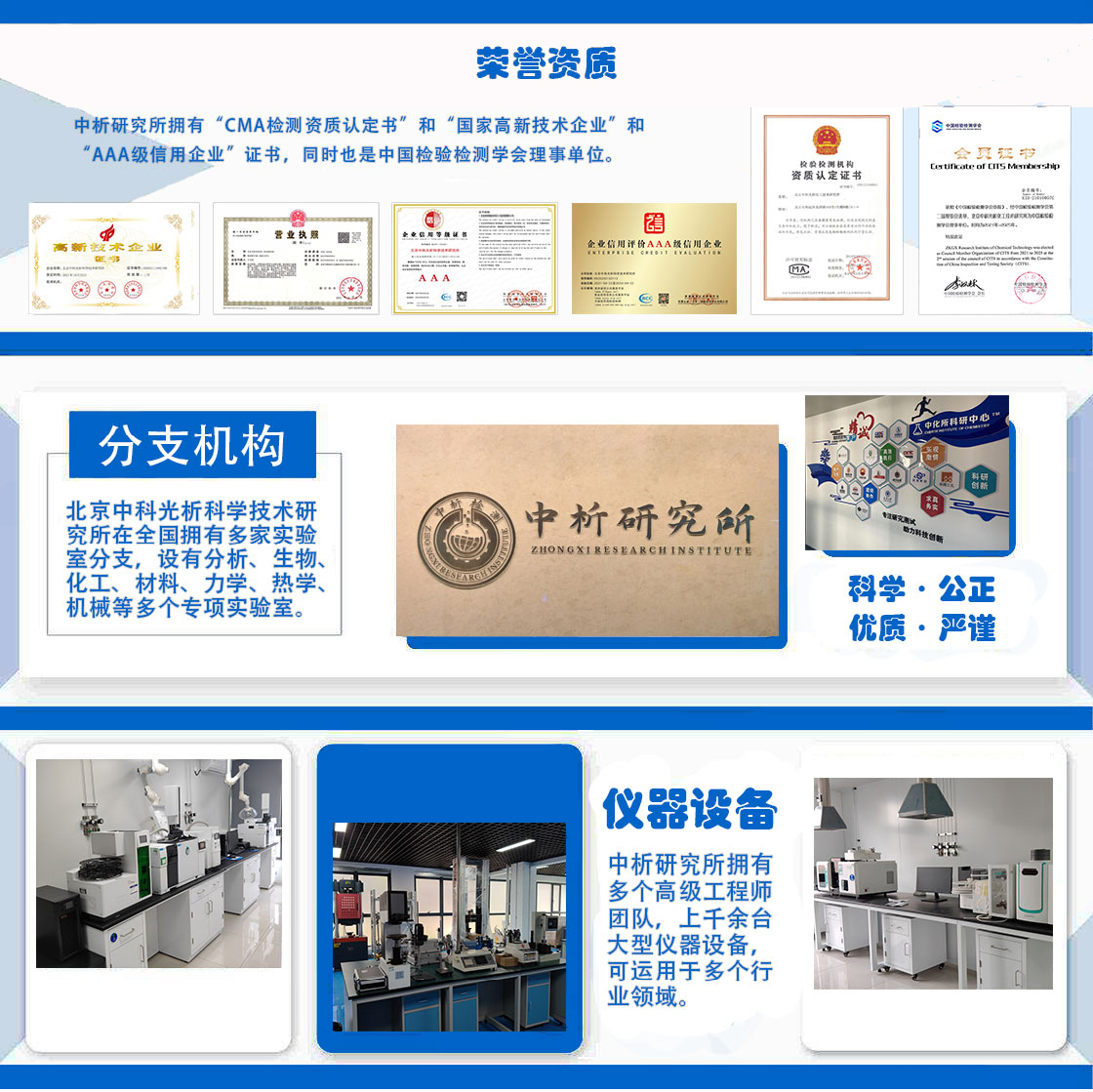
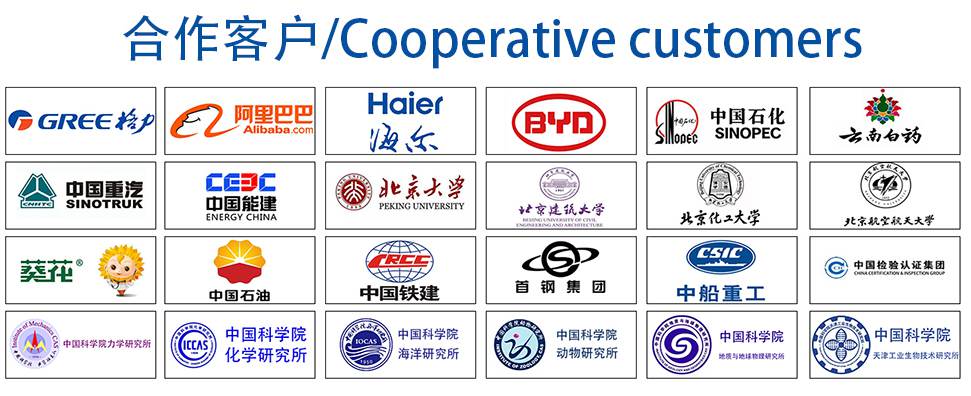