温感器控制检测的重要性与应用场景
温感器(温度传感器)作为环境监测与自动化控制系统的核心元件,其性能直接关系到工业设备、家用电器、医疗仪器等领域的运行安全与效率。温感器控制检测的核心目标在于验证其测量精度、响应速度、稳定性及抗干扰能力,确保其在复杂工况下仍能提供可靠数据。尤其在智能制造、冷链物流、新能源汽车电池管理等场景中,微小的温度偏差可能引发设备故障甚至安全事故,因此系统化的检测流程和标准化的测试项目成为质量控制的关键环节。
温感器控制检测的核心项目
1. 静态精度测试
通过恒温槽或高精度温度校准仪模拟标准温度环境,比对温感器输出值与标准参考值的误差。测试需覆盖全量程范围,包括常温段(-20℃~80℃)、高温极限(最高150℃)及低温极限(最低-40℃),依据IEC 60751或GB/T 30121等标准判定精度等级。
2. 动态响应测试
使用快速变温装置(如Peltier元件系统)模拟温度突变场景,记录温感器从检测到温度变化至输出稳定值的时间(τ值)。重点关注10%~90%阶跃响应的上升时间,评估其对突发温度波动的捕捉能力。
3. 环境适应性检测
包含三组关键实验:湿热循环测试(温度85℃/湿度85% RH,持续48小时)、振动测试(5Hz~500Hz随机振动谱)、EMC抗干扰测试(30V/m场强下的射频干扰)。验证传感器在极端环境下的信号稳定性与结构可靠性。
4. 长期稳定性验证
通过1000小时持续老化试验,每24小时记录零点漂移和量程漂移数据。结合Arrhenius加速模型推算器件寿命,确保在标称工作年限内误差不超过允许阈值。
5. 通讯协议兼容性测试
针对数字型温感器(如DS18B20、PT100变送器),需验证Modbus、HART、CAN等协议的数据帧完整性,并检测总线负载率超过70%时的通讯稳定性,确保与上位机系统的无缝对接。
智能化检测技术的发展趋势
随着AIoT技术的普及,现代温感器检测系统已引入机器学习算法,能够自动识别温度曲线异常模式(如非线性漂移、阶跃突变),并通过数字孪生技术实现虚拟标定。部分高端检测平台还支持OTA(空中下载)校准,显著提升了批量检测效率与精度可追溯性。
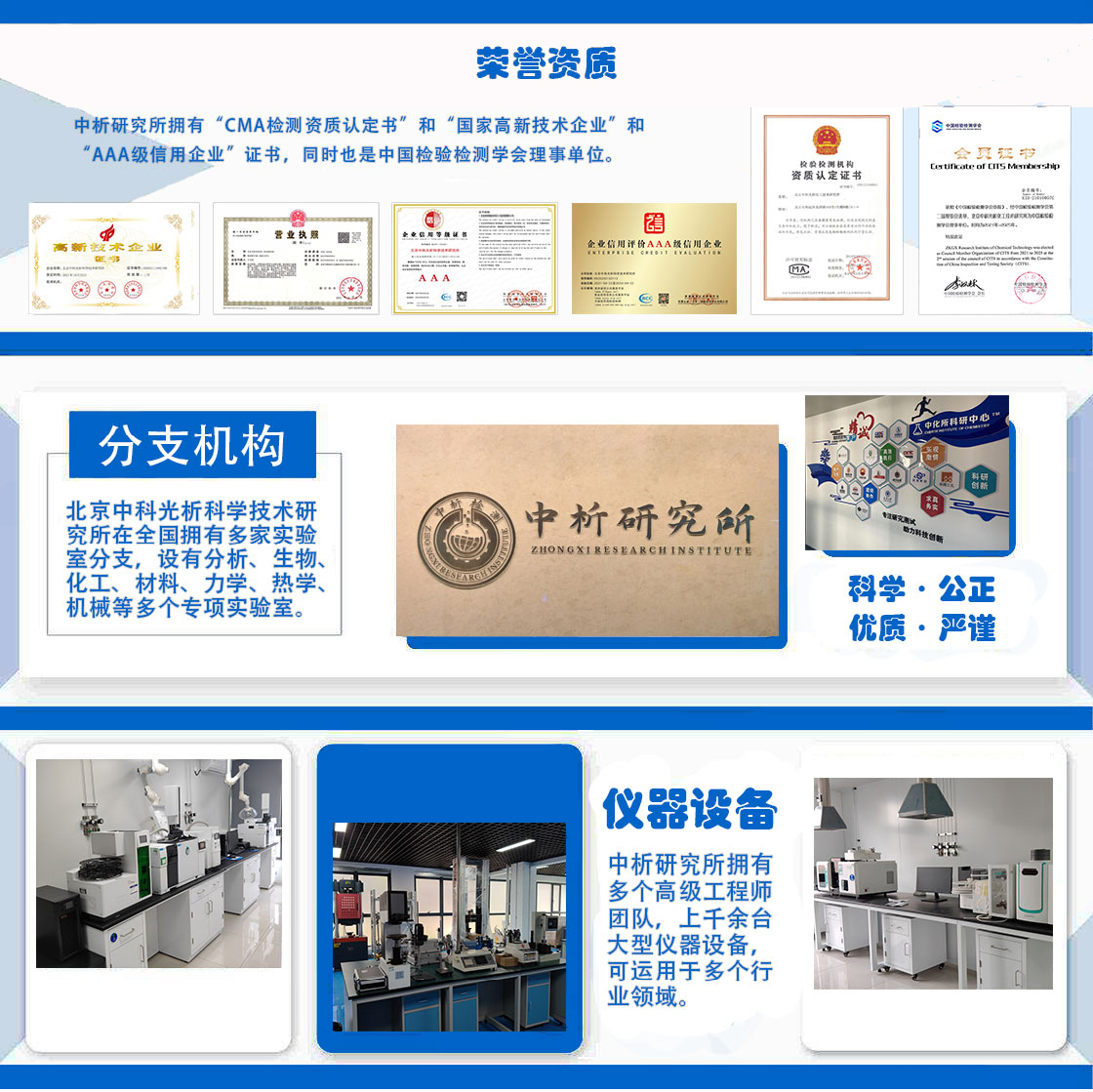
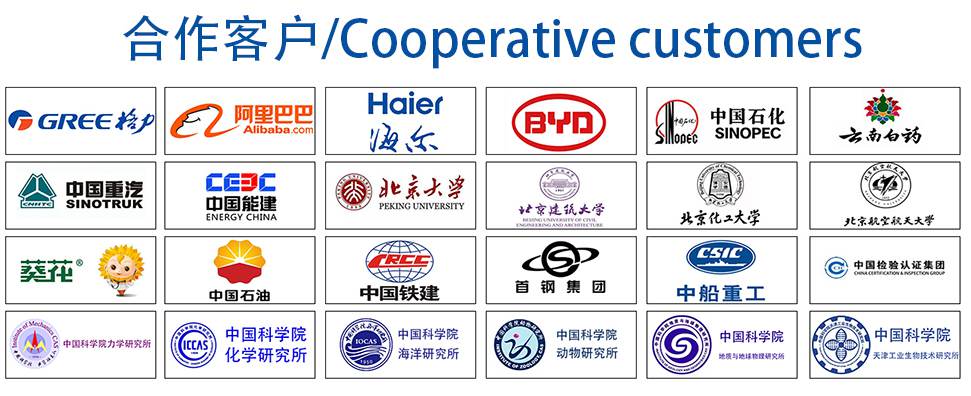