机车车辆用材料检测的重要性
机车车辆作为高速、重载运输的核心装备,其材料性能直接关系到运行安全性与使用寿命。在复杂多变的工况下(如高温、高压、振动、冲击等),材料需具备优异的机械强度、耐腐蚀性、抗疲劳性及环境适应性。因此,材料检测是机车制造、维修及质量管控过程中不可或缺的关键环节。通过科学规范的检测手段,可确保材料符合国家及行业标准(如ISO、GB/T、EN等),避免因材料缺陷引发的安全隐患,同时优化材料选型以提升车辆整体性能。
主要检测项目及内容
1. 机械性能测试
机械性能是材料检测的核心指标,包括拉伸试验(测定抗拉强度、屈服强度、延伸率)、冲击试验(评估材料韧性)、硬度测试(布氏/洛氏/维氏硬度)及弯曲试验。例如,车体结构钢需通过高强度拉伸测试以满足动态载荷要求。
2. 化学成分分析
通过光谱分析仪、碳硫分析仪等设备,精确测定材料的元素含量(如C、Mn、Si、S、P等),确保合金成分符合设计标准。例如,轮轴用钢的碳含量需严格控制在0.40%-0.60%范围,以平衡强度与韧性。
3. 金相组织分析
利用金相显微镜观察材料的微观组织结构(如晶粒度、夹杂物、相组成),评估热处理工艺效果。例如,转向架弹簧钢需具备均匀细密的回火马氏体组织以提升抗疲劳性能。
4. 耐腐蚀性测试
通过盐雾试验、湿热试验、电化学腐蚀测试等方法,模拟恶劣环境对材料的侵蚀,评估其防护涂层的耐久性。车体铝合金需通过至少500小时中性盐雾试验,防止因腐蚀导致的强度退化。
5. 无损检测(NDT)
采用超声波检测、磁粉探伤、渗透探伤及射线检测技术,在不破坏材料的前提下识别内部缺陷(如裂纹、气孔、夹杂等)。例如,焊接接头需通过100%超声波检测以确保连接可靠性。
6. 疲劳性能测试
通过高频疲劳试验机模拟长期交变载荷作用,测定材料的疲劳极限及寿命曲线。车轴材料需通过10^7次循环载荷测试,确保其在服役期内无断裂风险。
检测标准与技术创新
机车材料检测严格遵循《铁道车辆用材料技术条件》(TB/T 3139)、《高速动车组用材料技术规范》等标准。近年来,随着智能化技术的发展,原位检测、数字孪生建模及AI数据分析逐步应用于检测领域,显著提升了检测效率和精准度。未来,材料检测将更加注重环保性能(如可回收材料评估)与极端工况适应性(如耐寒耐高温涂层测试),为机车行业的高质量发展提供技术支撑。
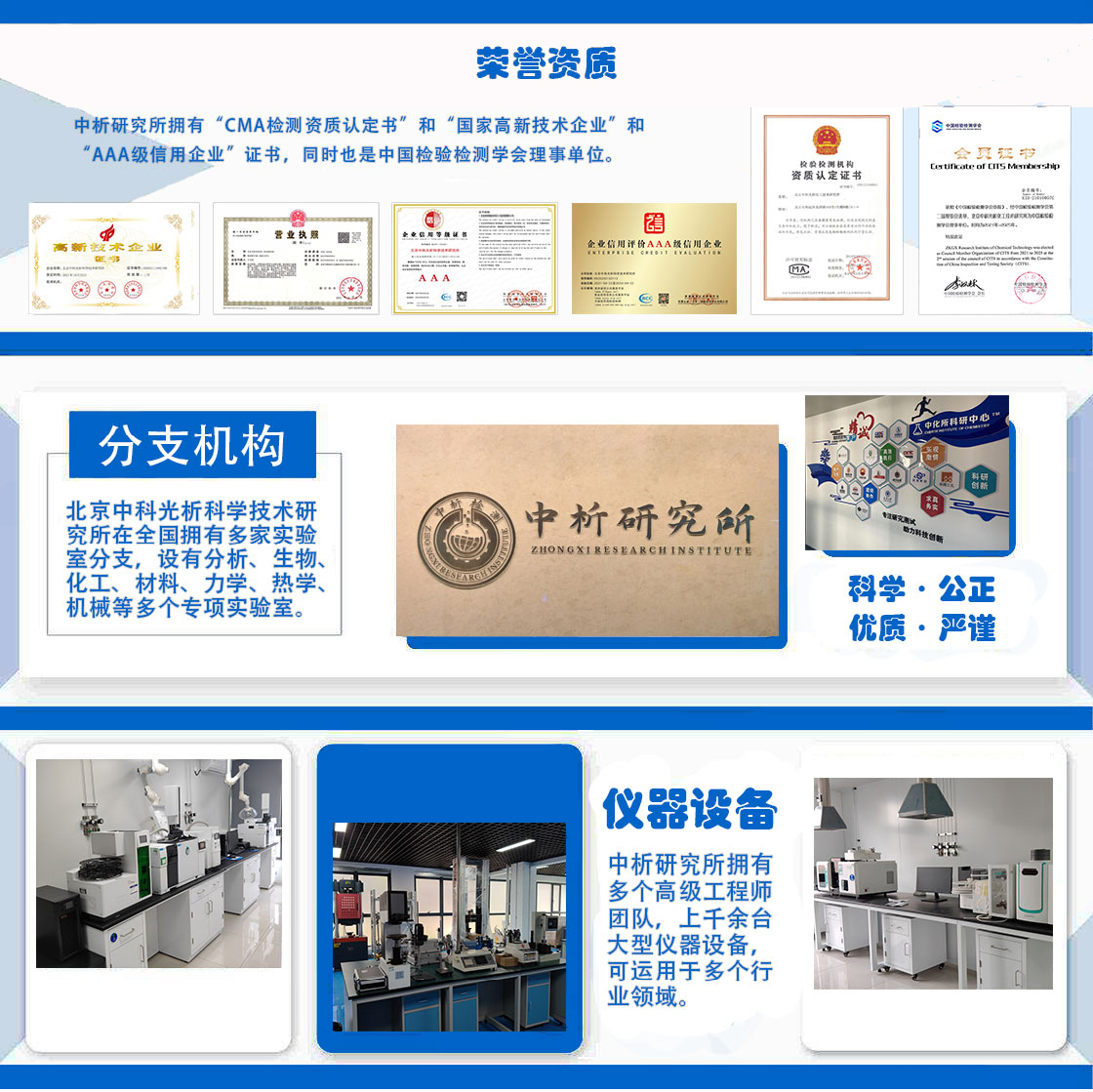
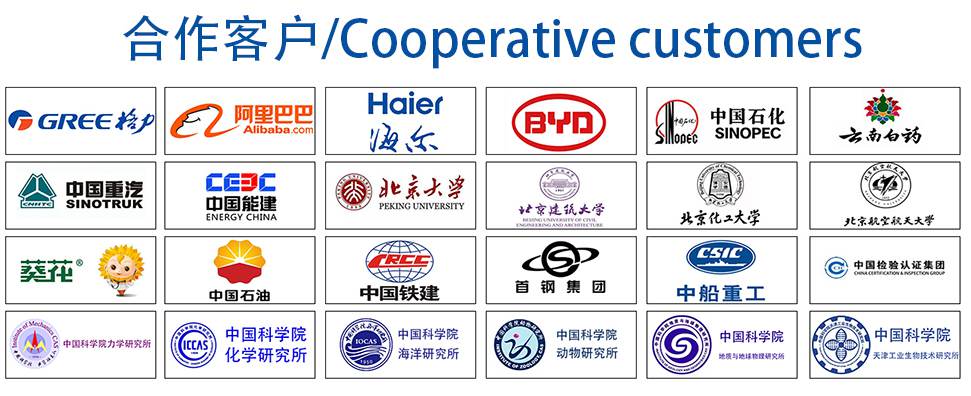