飞机电加温玻璃作为航空器关键部件之一,承担着防风、防冰、除雾及保持座舱视野清晰的重要功能。其通过内置电热元件对玻璃表面进行加热,确保极端高空环境中不会因低温结冰或起雾影响飞行员视线。然而,随着飞行次数的增加和环境压力的作用,电加温玻璃可能发生性能衰减、结构损伤或电气故障。因此,定期开展系统性检测是保障飞行安全、延长部件寿命的核心环节。检测项目需覆盖电热性能、结构完整性、绝缘特性等多个维度,并结合齐全仪器与标准规范进行全面评估。
一、电热性能检测
通过模拟高空低温环境,测试玻璃在额定电压下的升温速率、温度均匀性及稳态功耗。使用红外热成像仪记录表面温度分布,验证加热膜工作是否正常,避免局部过热或冷区现象。
二、玻璃结构完整性检测
采用目视检查、超声波探伤和X射线检测技术,排查玻璃内部裂纹、气泡、分层或导电膜断裂等问题。重点检查边缘区域和电极端子连接处,确保无应力集中导致的隐性损伤。
三、密封性及透光率测试
使用氦质谱检漏仪验证玻璃夹层密封性能,防止湿气渗透导致电热元件氧化。同时通过光谱分析仪检测透光率,确保可见光透过率≥85%(符合ASTM F733标准),避免光学畸变影响飞行视野。
四、电气安全检测
测量绝缘电阻(≥500MΩ/1500VDC)和耐压强度(3000V/1min无击穿),评估加热电路的电气安全性。使用接地导通测试仪验证屏蔽层与机身搭接电阻(≤0.1Ω),符合MIL-STD-889标准要求。
五、环境适应性试验
通过温度循环(-60℃至+80℃)、湿热循环(95%RH)和盐雾试验(1000h),验证玻璃在极端环境下的耐久性。振动测试需模拟飞机起降阶段0.5g加速度的长期机械冲击影响。
六、功能寿命评估
连续运行电加温系统2000小时,监测功率衰减是否<10%,同时进行500次冷热循环模拟老化测试。结合历史维护数据建立寿命预测模型,精准制定更换周期。
七、维修后复检流程
更换加热膜或修复导电线路后,需重新执行绝缘耐压测试和功能验证,并采用高精度电桥测量电路阻抗平衡度(偏差≤5%)。最终结果需录入飞机持续适航文件系统,确保符合CCAR-21-R4适航要求。
通过上述系统化检测,可及时发现电加温玻璃的潜在失效风险。检测数据需与原始出厂参数进行趋势对比,对性能降幅超过15%的部件启动预防性更换程序,同时建议每500飞行小时或每年进行一次全面检测(以先到为准),切实保障航空器运行安全。
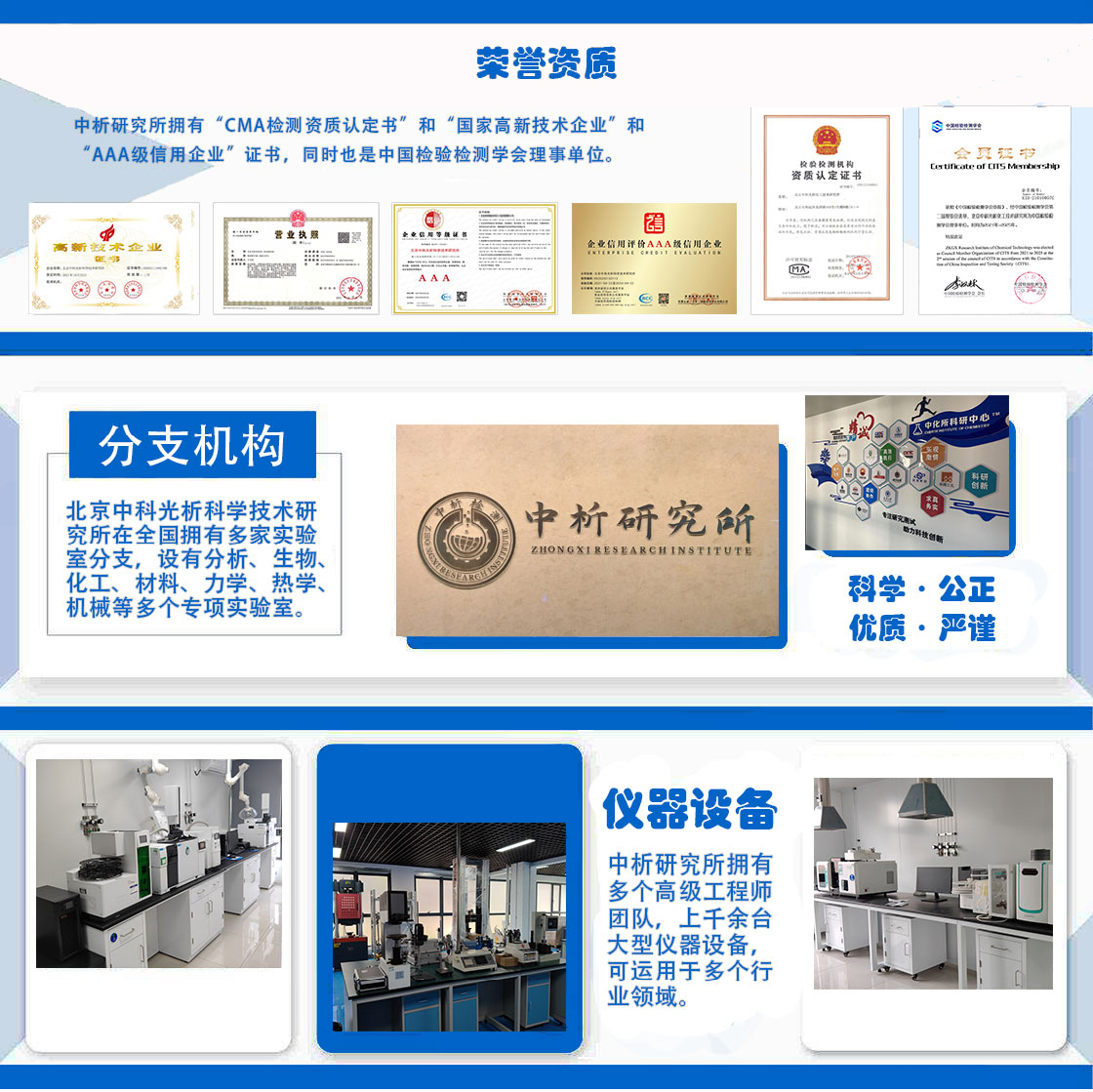
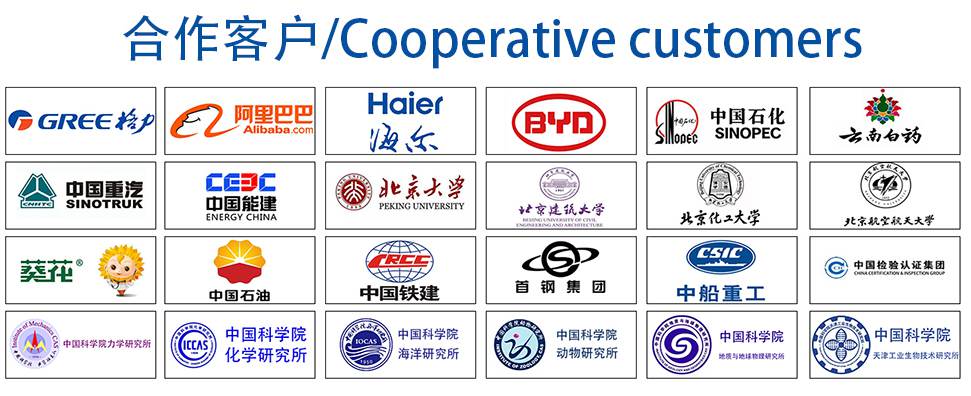