航天用钛合金饼材检测的重要性与技术要求
在航空航天领域,钛合金因其高强度、耐高温、抗腐蚀和轻量化等特性,成为发动机压气机盘、火箭燃料舱壳体等关键部件的核心材料。其中,钛合金饼材作为锻造用坯料,其质量直接影响最终零件的性能与安全性。由于航天器需承受极端温度、高压及复杂载荷环境,对饼材的冶金缺陷、组织均匀性及力学性能提出了近乎苛刻的要求。据统计,航天用钛合金材料缺陷导致的故障中,约60%源自原材料质量问题。因此,建立系统化的检测体系是确保航天装备可靠性的关键环节。
1. 化学成分分析
采用直读光谱仪(OES)结合电感耦合等离子体质谱(ICP-MS)进行全元素分析,确保钛含量控制在89%-95%范围内,关键合金元素如Al(5.5-6.8%)、V(3.5-4.5%)等需严格符合GB/T 3620.1-2016标准。特别关注间隙元素O≤0.20%、N≤0.05%的管控,避免β相脆性转变。
2. 力学性能测试
通过万能试验机进行室温/高温拉伸试验(GB/T 228.1),要求抗拉强度≥895MPa,延伸率≥10%。夏比冲击试验(GB/T 229)测定-50℃条件下的冲击功值(≥34J),并采用旋转弯曲疲劳试验机验证10^7次循环下的疲劳极限。
3. 显微组织检验
依据GB/T 5168进行金相制样,使用500倍金相显微镜观察α+β双相组织形态,评估初生α相含量(15-45%)、β晶粒尺寸(≤100μm)。扫描电镜(SEM)配合能谱分析(EDS)检测元素偏析,电子背散射衍射(EBSD)表征织构分布。
4. 无损检测技术应用
采用多频涡流检测(ECT)筛查表面裂纹,超声波探伤(UT)灵敏度需达到Φ0.8mm平底孔标准,覆盖率100%。针对大厚度饼材(>300mm),实施X射线分层成像(CL)检测内部疏松缺陷,缺陷当量直径不得大于1.2mm。
5. 尺寸与几何公差检测
使用激光跟踪仪进行三维建模,检测直径公差(±0.5mm)、平面度(≤0.1mm/m)及垂直度(≤0.05°)。超声测厚仪多点抽样验证厚度均匀性,波动范围控制在±1%以内。
6. 热处理工艺验证
通过差示扫描量热法(DSC)测定β转变温度(Tβ),建立固溶时效工艺曲线。残余应力测试采用X射线衍射法(XRD),表面残余压应力应>200MPa,芯部拉应力<50MPa。
现代航天用钛合金饼材检测已形成"成分-组织-性能"三位一体的评价体系,配合数字化检测报告系统,实现全生命周期质量追溯。随着增材制造技术的应用,原位检测、CT三维重建等新型方法正在不断完善,为新一代航天装备提供更可靠的材料保障。
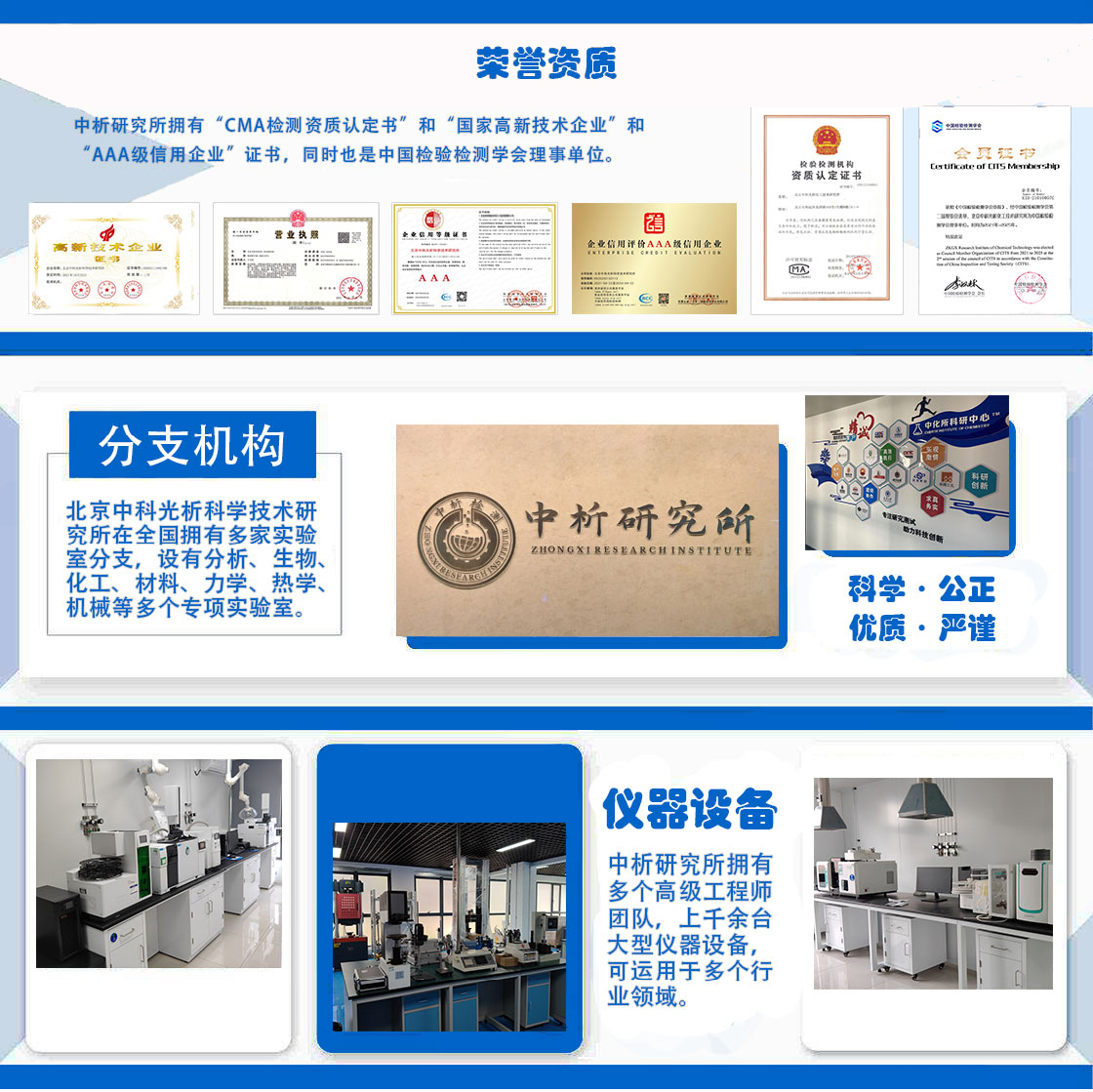
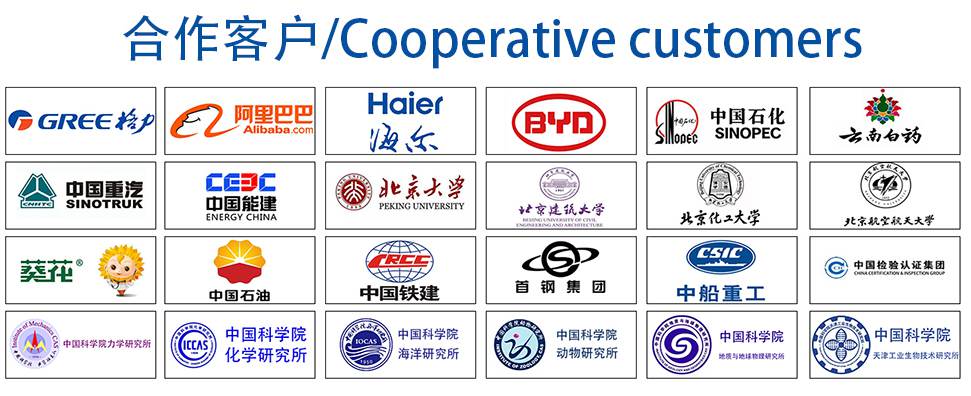