机加工零件检测的关键项目与技术解析
在机械制造领域,机加工零件的质量控制直接关系到设备性能和使用寿命。随着工业4.0的推进,检测技术正从传统人工测量向数字化、智能化方向转型。根据2023年《精密制造行业白皮书》数据显示,采用系统化检测流程的企业产品合格率平均提升23.6%,返工成本降低42%。本文将从核心检测维度出发,深入解析现代机加工零件检测的标准体系与技术应用。
一、尺寸精度检测
作为基础检测项目,需使用三坐标测量机(CMM)对长宽高、孔径、螺纹等关键尺寸进行μm级测量。特别对于薄壁件和异形件,需结合激光扫描技术建立三维数字模型,通过比对理论值与实测值的偏差云图,精准定位超差区域。ISO 2768标准规定,常规零件的线性尺寸公差应控制在IT7-IT9级。
二、形位公差验证
包含平面度、圆度、同轴度等12项基本公差检测,需采用专用工装配合电子水平仪、圆度仪等设备。例如齿轮箱壳体要求平面度≤0.02mm/m,通过高精度花岗岩平台配合数显千分表进行多点测量。最新自动化检测线已实现形位公差的在线实时监控,检测效率提升5倍以上。
三、表面质量评估
粗糙度检测使用接触式轮廓仪(Ra值测量)和激光共聚焦显微镜(3D形貌分析),航空零件要求Ra≤0.8μm。表面缺陷检测引入机器视觉系统,配置环形LED光源和500万像素工业相机,可识别0.05mm级别的划痕、气孔等缺陷,检测速度达120件/分钟。
四、材料性能测试
包括硬度(洛氏/维氏硬度计)、金相组织(电子显微镜)、化学成分(光谱分析仪)三大模块。以汽车传动轴为例,需确保表面淬火层深度0.8-1.2mm,芯部硬度HRC22-28,同时通过能谱分析验证材料中铬、钼等合金元素含量是否符合AMS 6414标准。
五、功能性装配检测
采用模拟工况的检测平台,如液压阀块需在35MPa压力下测试密封性能,精密丝杠要进行200km模拟行程测试。智能化检测系统可同步采集振动、温升、扭矩等多维度数据,通过AI算法预测零件使用寿命,实现从符合性检测向预防性质量控制的跨越。
当前检测技术正与数字孪生、区块链溯源等新技术深度融合。建议企业建立包含11项核心指标的检测矩阵,结合MES系统实现质量数据全流程追溯,这将帮助制造企业在新一轮产业升级中构建核心竞争力。
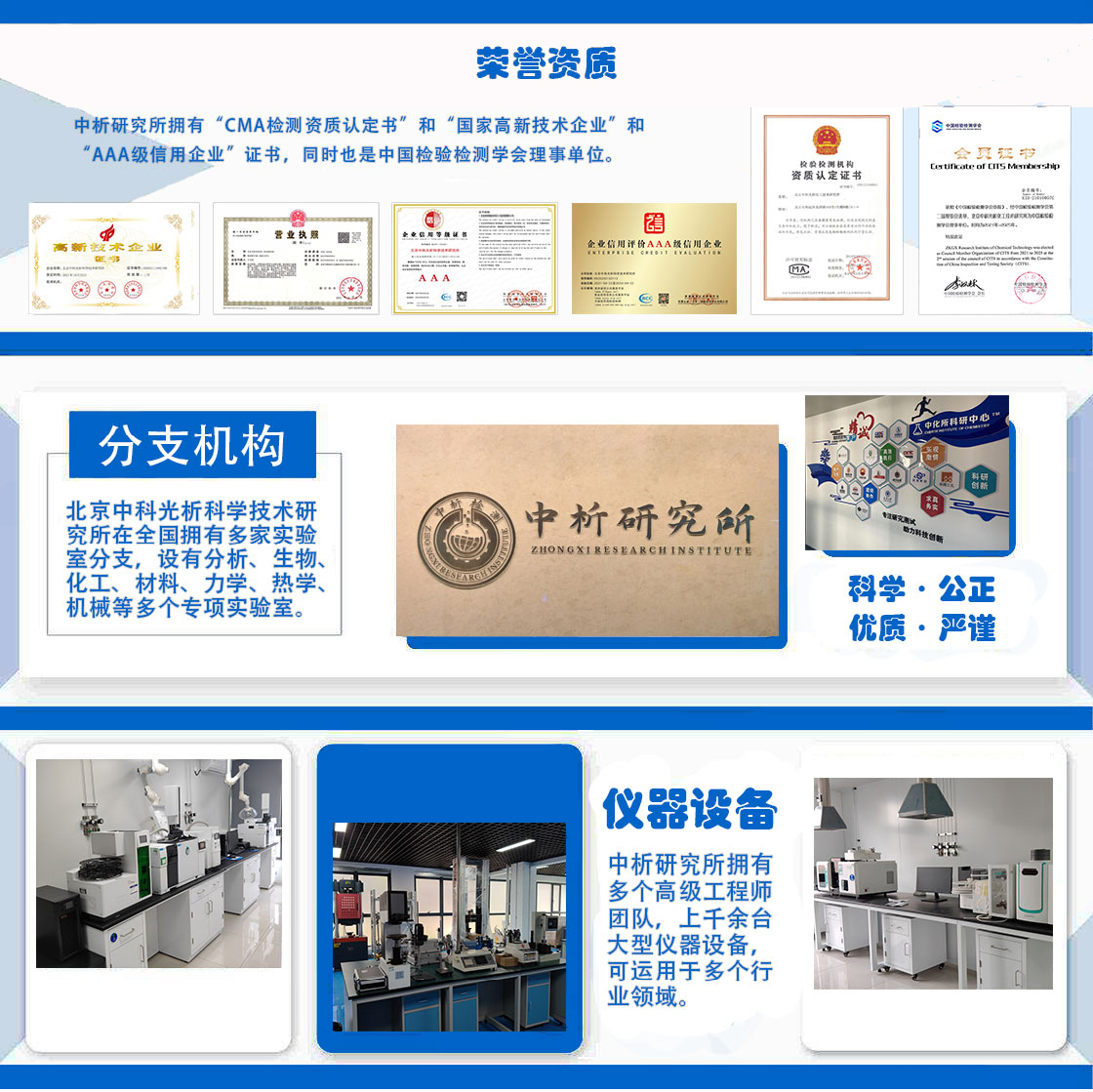
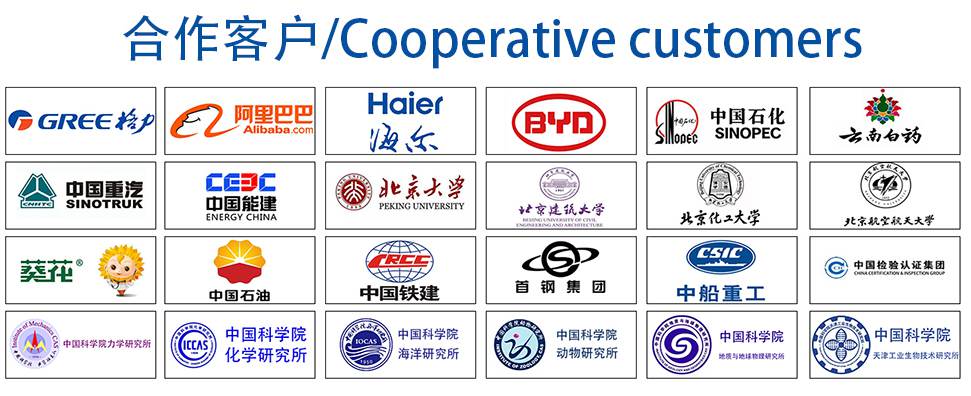