齿轮滚刀检测
实验室拥有众多大型仪器及各类分析检测设备,研究所长期与各大企业、高校和科研院所保持合作伙伴关系,始终以科学研究为首任,以客户为中心,不断提高自身综合检测能力和水平,致力于成为全国科学材料研发领域服务平台。
立即咨询齿轮滚刀检测的重要性
齿轮滚刀作为齿轮加工的核心刀具,其精度与质量直接决定了齿轮产品的传动性能、使用寿命和噪音水平。在高速、重载的工业应用场景中,滚刀的微小误差可能导致齿轮啮合不良,引发设备故障。因此,通过系统化的检测项目对齿轮滚刀进行全维度质量把控,是保障齿轮制造精度的必要环节。检测过程需覆盖材料性能、几何精度、表面质量及热处理效果等关键指标,确保滚刀从设计到生产的每个环节均符合国家或行业标准(如GB/T 6084、ISO 4468)。
核心检测项目及方法
1. 几何精度检测
采用三坐标测量机(CMM)或专用刀具检测仪,对滚刀的轴向齿距偏差、齿形误差、螺旋线偏差进行精密测量。重点检测前角、后角、容屑槽对称度等参数,确保切削刃的空间位置精度控制在±0.005mm以内。对于模数≥3的滚刀,还需进行齿顶圆跳动量检测。
2. 表面硬度与热处理检测
通过洛氏硬度计(HRC)或维氏硬度计(HV)分层测量刃口区(58-62HRC)与刀体芯部(35-45HRC)的硬度梯度,验证渗碳/氮化处理的深度均匀性。配合金相显微镜观察马氏体形态,评估热处理工艺是否达到消除残余奥氏体的技术要求。
3. 涂层性能检测
对TiN/TiAlN等PVD涂层进行三方面考核:使用纳米压痕仪测试涂层硬度(>2000HV),通过划痕试验机检测涂层结合力(临界载荷LC≥70N),采用高温摩擦磨损试验机模拟实际切削工况下的耐磨性能(摩擦系数≤0.4)。
4. 动态平衡检测
在6000-8000rpm转速范围内进行动平衡测试,要求剩余不平衡量不超过G2.5级标准。对于直径>150mm的大型滚刀,需在两端轴承位安装振动传感器,监测高速旋转时的振幅是否<0.01mm。
5. 切削性能验证
通过标准试件切削试验,考核滚刀的实际加工能力。监测切削力波动范围(≤±15%)、加工表面粗糙度(Ra<1.6μm)及刀具寿命(连续加工20小时齿形精度维持IT6级),建立切削参数优化数据库。
数字化检测趋势
随着工业4.0技术的应用,基于机器视觉的在线检测系统可实时捕捉滚刀表面缺陷,AI算法可预测刀具剩余寿命。激光干涉仪配合数字孪生技术,已实现滚刀全生命周期质量数据的云端管理与追溯,检测效率较传统方式提升40%以上。
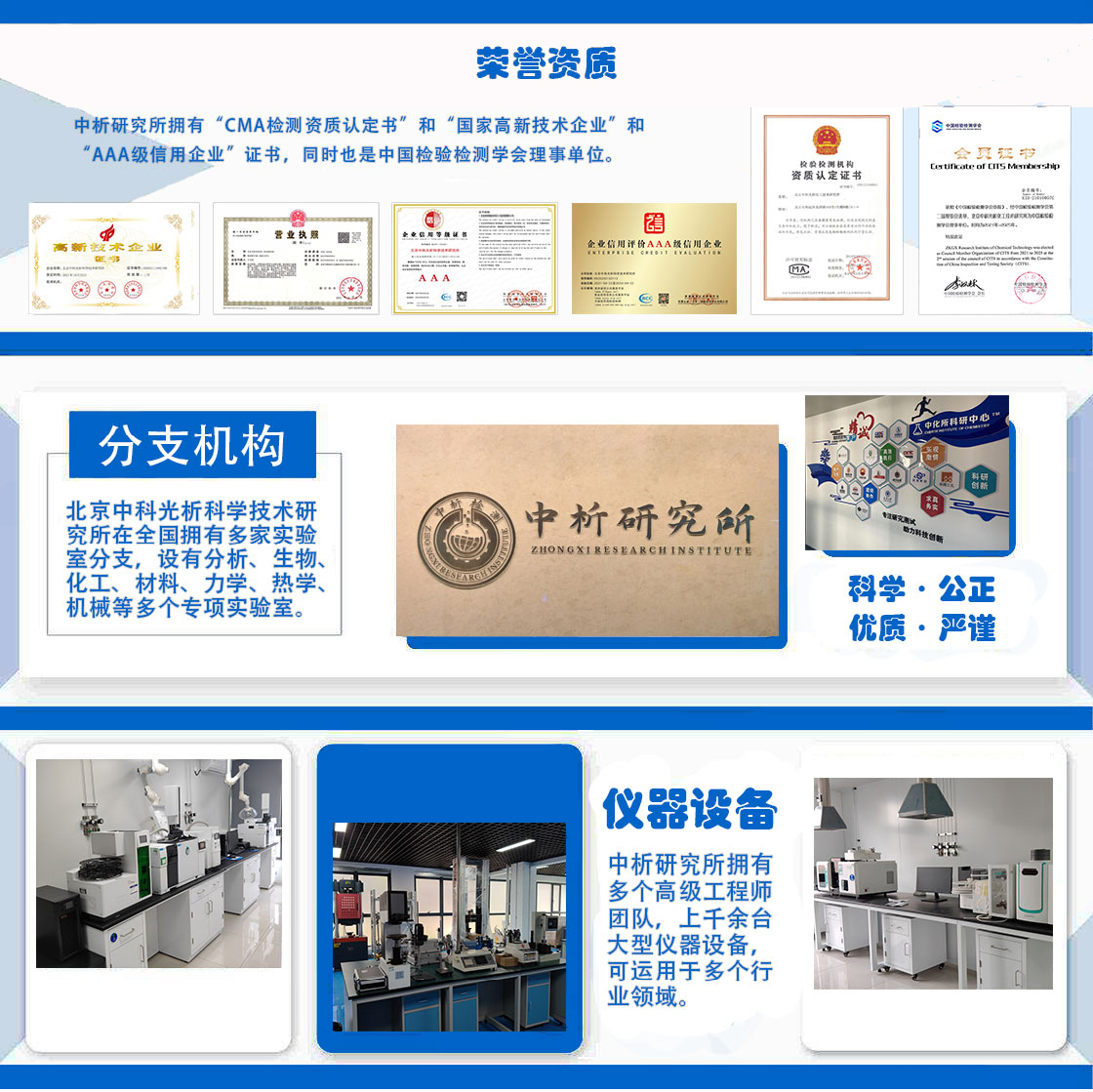
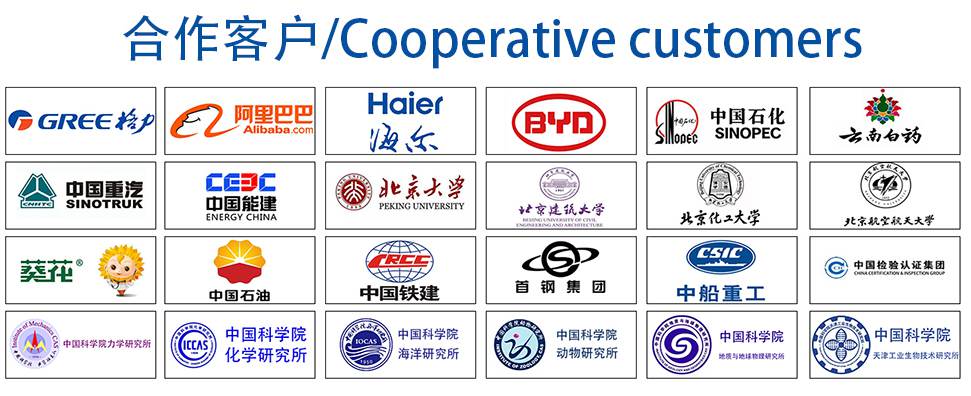