注汽系统检测的重要性与实施要点
注汽系统作为稠油热采、工业锅炉及热能转换领域的核心设备,其运行状态直接关系到能源效率、生产安全及环境保护。系统通过高压蒸汽注入地层或工艺管线实现目标功能,但因长期处于高温(300-450℃)、高压(10-25MPa)及腐蚀性介质环境下,易出现管线变形、阀门泄漏、流量偏差等问题。定期开展注汽系统检测能有效预防突发性故障,延长设备寿命,保障蒸汽干度达标,从而提高采收率或热效率近30%。现代检测技术已形成涵盖物理参数、化学指标、机械性能的完整评估体系。
核心检测项目分类及实施规范
1. 压力与温度联动监测
采用智能压力传感器阵列与红外热成像技术,对注汽锅炉出口、分配管汇、井下井口等关键节点进行24小时动态监测。重点检测瞬时压力波动是否超出设计值的±5%,温度梯度是否符合每百米管线≤15℃的标准,同步验证安全阀起跳压力精度误差是否控制在0.5MPa以内。
2. 蒸汽干度在线分析
通过两相流计量装置与微波水分仪的结合应用,实时监测蒸汽质量干度值。要求工业锅炉出口干度≥75%,井口注汽干度≥85%,当检测到干度值连续2小时低于临界值时,自动触发氯化物浓度检测模块排查水质异常。
3. 管线完整性评估
结合DR数字射线检测与电磁超声测厚技术,对高温管线进行三维扫描。重点检测焊缝区域缺陷尺寸(裂纹长度≤3mm)、弯头处壁厚减薄量(≤设计值10%),并建立腐蚀速率预测模型。对于服役超过5年的管线,需增加应力腐蚀开裂(SCC)专项检测。
4. 热能效率综合评价
采用热流密度计与烟气分析系统,计算系统综合热效率指标。标准要求燃气注汽锅炉热效率≥88%,燃煤系统≥82%,同时对排烟温度(≤180℃)、氧含量(3-6%)等参数进行优化诊断,生成能效改进方案。
5. 智能控制系统验证
对PLC/DCS控制系统进行三级检测:硬件层面测试I/O模块精度(±0.1%FS),软件层面验证PID调节响应时间(≤2s),系统层面实施故障注入测试,确保在供电异常、传感器失效等极端情况下仍能维持安全联锁功能。
6. 环境保护专项检测
按照GB13271锅炉大气污染物排放标准,配置在线CEMS系统监测氮氧化物(≤150mg/m³)、二氧化硫(≤100mg/m³)及颗粒物(≤30mg/m³)排放浓度,同时设置噪声监测点确保厂界噪声昼间≤65dB(A)。
现代注汽系统检测已发展为包含18大类76项指标的标准化流程,通过采用物联网传感、数字孪生、大数据分析等技术,实现从定期检修向预测性维护的转变。专业检测机构建议每季度开展1次常规检测,新投运系统前三个月需进行月度检测,并结合ASME B31.3、SY/T 5323等行业标准建立全生命周期健康档案。
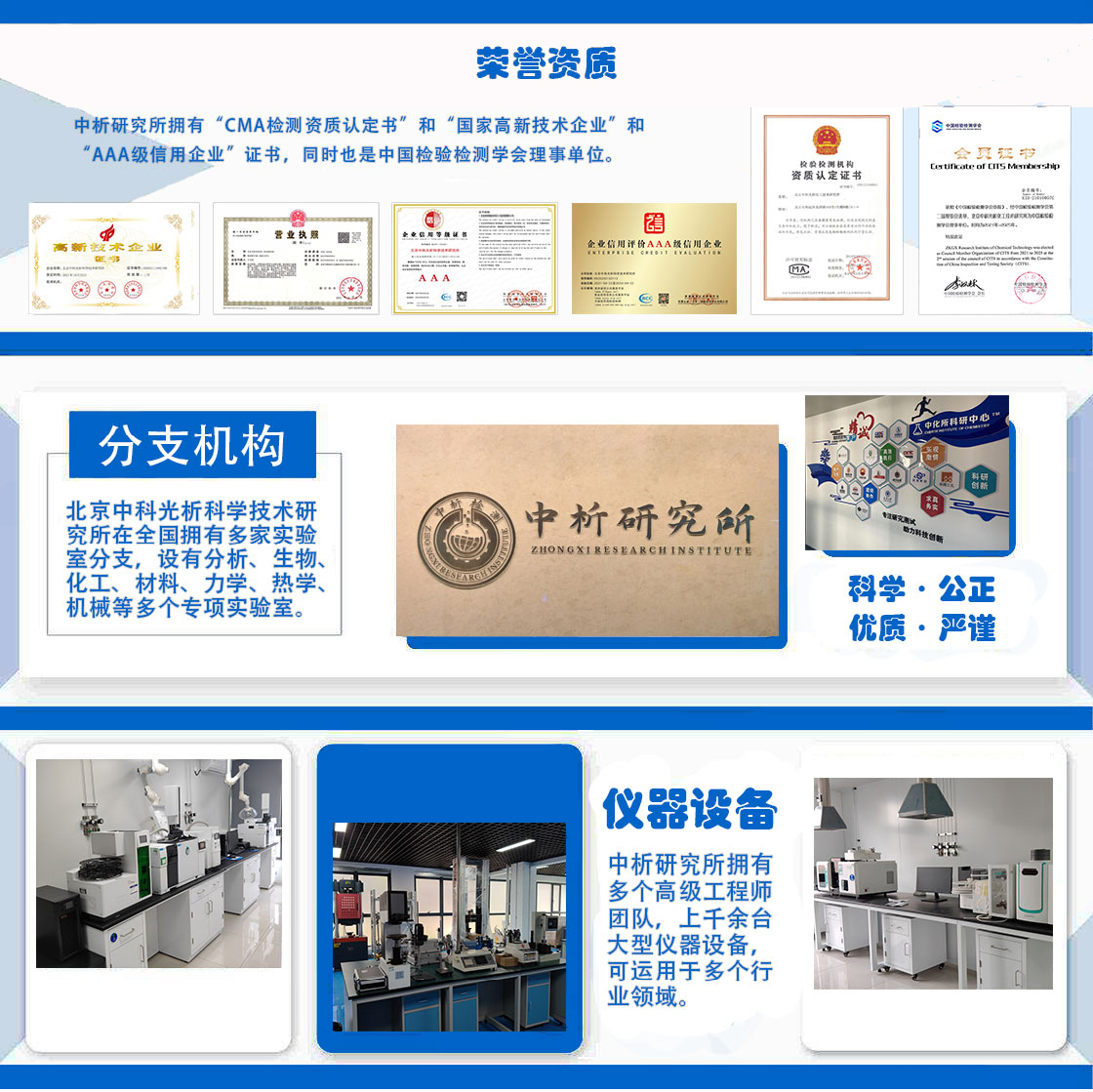
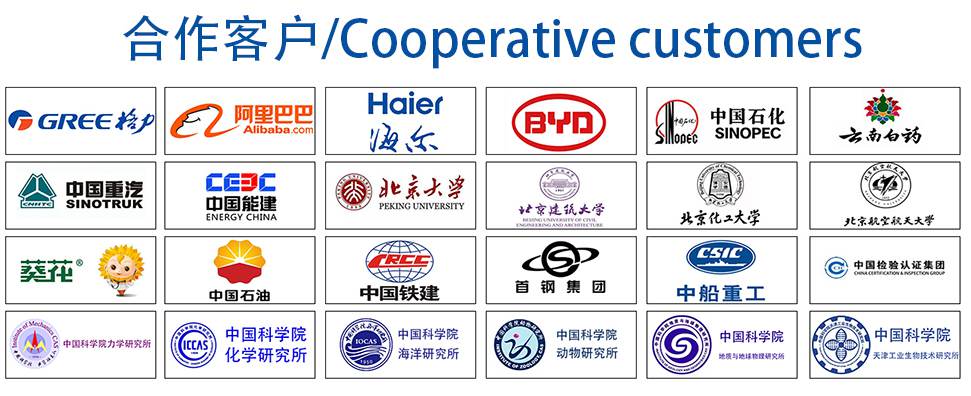