高压锻件检测的重要性与核心内容
高压锻件作为石油化工、能源电力、航空航天等领域的核心承压部件,其质量直接关系到设备运行安全与使用寿命。由于长期承受高温、高压及腐蚀介质作用,锻件内部可能产生裂纹、气孔、夹杂等缺陷,导致突发性失效风险。因此,通过科学的检测技术对原材料、制造工艺及成品质量进行全面评估,成为保障高压锻件可靠性的关键环节。检测过程需严格遵循ASME、ISO 10423、NB/T 47013等行业标准,覆盖从化学成分到力学性能的多维度指标。
高压锻件核心检测项目分类
1. 材质成分分析
采用光谱分析仪(OES)和碳硫分析仪对锻件材料的C、Mn、Cr、Mo、V等合金元素进行定量检测,确保符合ASTM A182等材料标准。尤其关注硫磷含量控制,硫化物超标会显著降低锻件抗氢致开裂性能。
2. 力学性能测试
通过万能试验机完成拉伸(屈服强度、抗拉强度、延伸率)、冲击(夏比V型缺口冲击试验)、硬度(布氏/洛氏硬度)等测试。高温拉伸试验需模拟实际工况温度,验证材料在400-600℃下的性能稳定性。
3. 无损探伤检测
综合应用超声检测(UT)、磁粉检测(MT)、渗透检测(PT)三种技术:
- 超声相控阵(PAUT)可检测内部缺陷的深度、尺寸及取向,灵敏度达Φ2mm当量平底孔
- 磁粉检测用于表面及近表面裂纹检测,灵敏度达0.02mm开口裂纹
- 渗透检测适用于非磁性材料表面开口缺陷的显现
4. 金相组织检验
通过光学显微镜和扫描电镜(SEM)观察晶粒度(ASTM E112)、夹杂物级别(ASTM E45)、带状组织等微观特征。对马氏体不锈钢锻件需特别检测δ铁素体含量,控制在5-15%范围以保证耐蚀性。
5. 尺寸公差检测
使用三维坐标测量仪(CMM)验证法兰密封面平面度(≤0.05mm)、螺栓孔位置度(±0.1mm)等关键尺寸,配合超声波测厚仪检查壁厚均匀性(公差±5%)。
6. 压力循环试验
在压力试验台上进行150%设计压力的静水压试验,持续30分钟无渗漏。对交变载荷部件需进行10^5次压力循环测试(压力波动幅度±20%),监测疲劳裂纹萌生情况。
数字化检测技术应用趋势
当前正逐步推广TOFD超声成像、DR数字射线、三维CT扫描等智能检测手段,结合大数据平台实现检测结果的可视化分析与质量追溯。某核电锻件项目中,通过多探头阵列超声系统实现了0.8mm微裂纹的精准定位,检测效率提升40%以上。
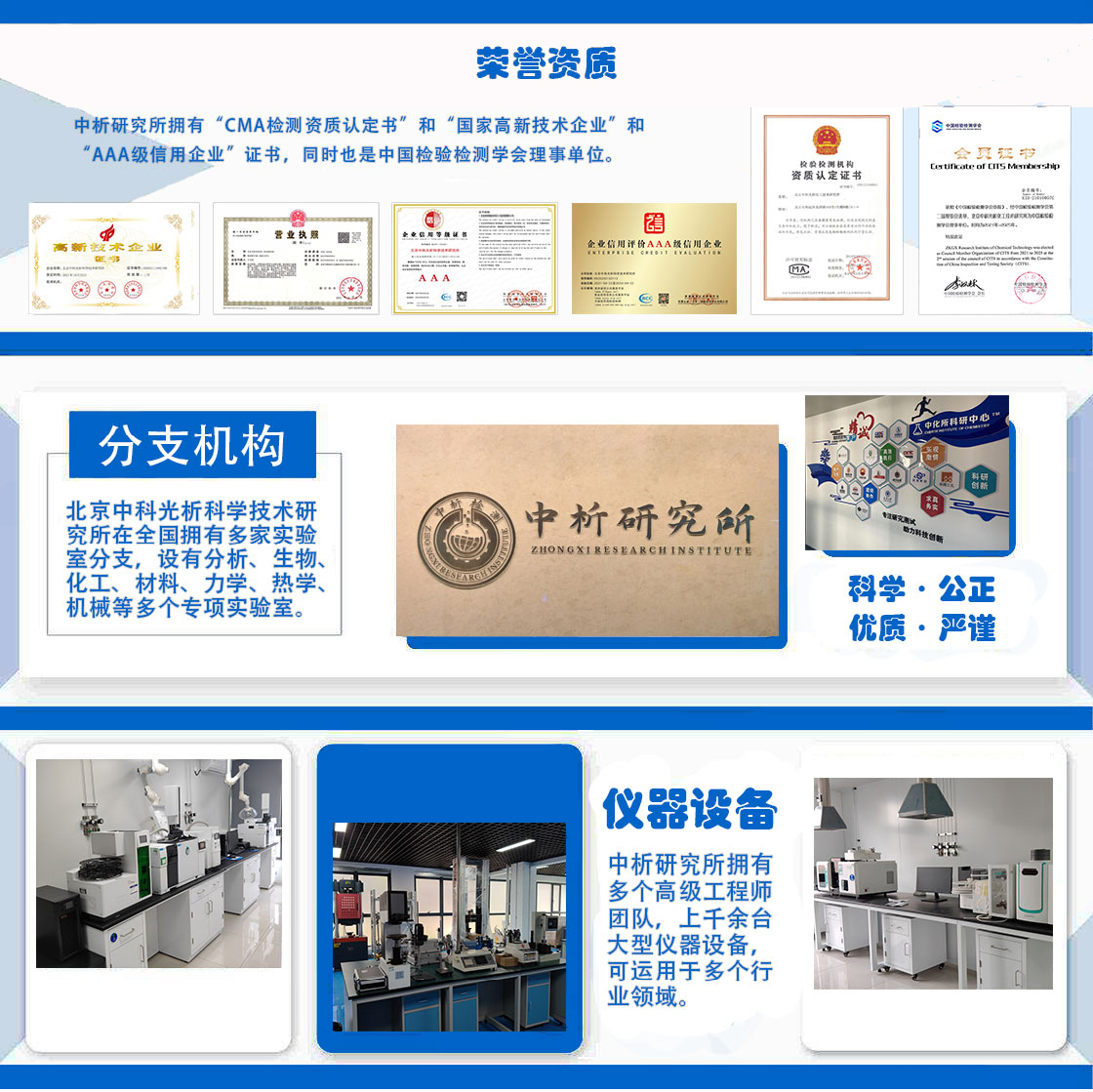
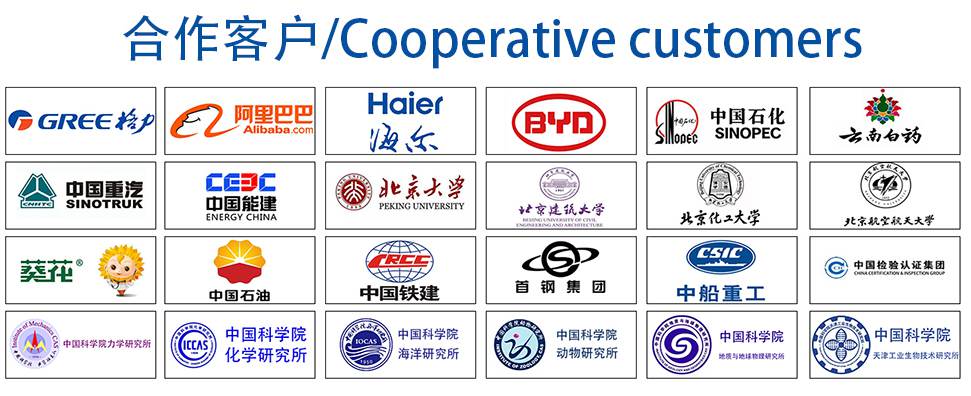