结构密封件检测的重要性与核心内容
结构密封件作为工业设备、建筑幕墙、汽车制造等领域的关键组件,承担着防泄漏、抗振动、耐老化等重要功能。其性能直接影响系统的安全性、可靠性和使用寿命。随着行业对质量要求的提升,结构密封件检测已成为生产、安装及维护全流程中不可或缺的环节。通过科学的检测手段,可精准评估密封材料的物理特性、化学稳定性和环境适应性,确保其在实际工况中达到设计预期。
核心检测项目分析
1. 物理性能测试
包括拉伸强度、断裂伸长率、硬度(邵氏A/D)、压缩永久变形率等指标的测定。例如通过万能材料试验机模拟密封件在长期受压状态下的回弹性能,判断其抗变形能力是否满足安装需求。
2. 化学成分分析
采用光谱仪(如EDX)、色谱仪(GC-MS)等设备检测原材料中的主成分及添加剂含量,验证是否符合RoHS、REACH等环保要求,同时排除有害物质超标风险。
3. 密封性能测试
通过气密性试验(压差法)、液体渗透试验等手段,模拟实际工况下的介质压力(如液压油、气体),评估密封件在不同温度(-40℃至150℃)、压力(0-50MPa)条件下的密封有效性。
4. 耐久性测试
包含加速老化试验(紫外线/臭氧老化箱)、疲劳寿命测试(动态往复运动模拟)等,验证密封件在长期使用后的性能衰减程度,预测其更换周期。
5. 外观与尺寸检测
利用光学投影仪、三维测量仪等工具,检查密封件表面缺陷(裂纹、气泡、杂质)及关键尺寸(内径、截面厚度)的公差范围,确保与装配部件的匹配精度。
行业标准与认证体系
检测需参照GB/T 3452.1(液压气动用橡胶密封件)、ASTM D2000(汽车密封件)、EN 12188(建筑幕墙密封胶)等标准。通过 /CMA认证的实验室可出具具有国际互认效力的检测报告,为产品出口或招投标提供技术背书。
检测流程优化建议
企业应建立“原料入厂-过程监控-成品检验”三级检测体系,结合X射线无损检测、红外热成像等齐全技术,实现缺陷早期预警。对于特殊工况(如核电站、深海设备),还需增加辐射耐受性、深海高压密封专项测试,构建完整的质量闭环。
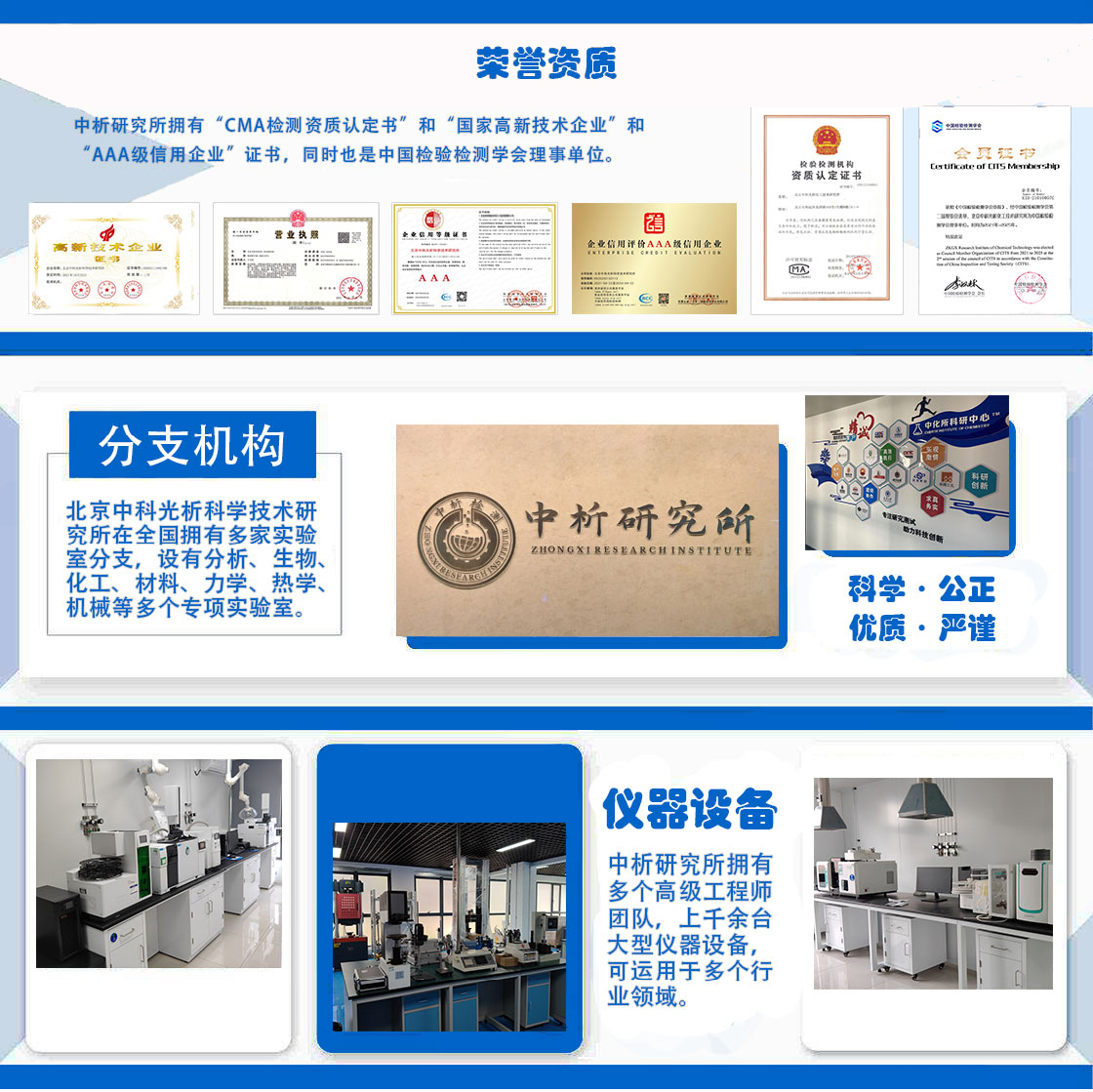
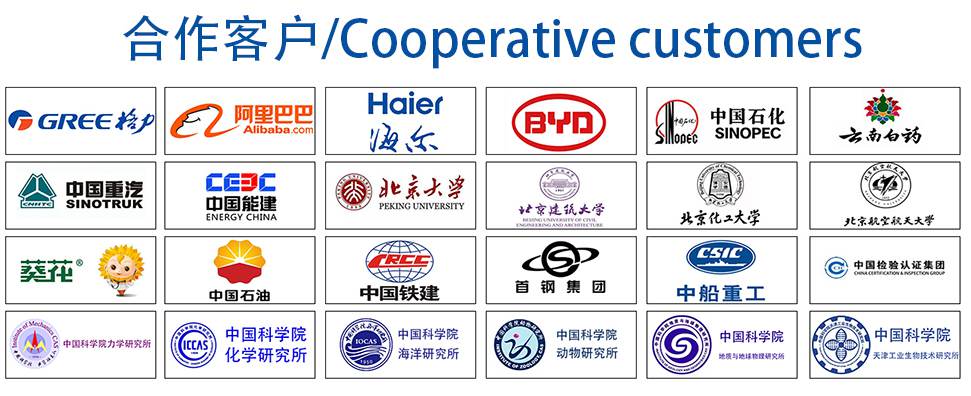