不压井作业装备检测的重要性
不压井作业(Snubbing Operation)是一种在油气井维护、修井或完井过程中无需压井液即可控制井口压力的高效技术。与传统作业方式相比,它避免了地层污染、节约了压井液成本,同时缩短了作业周期。然而,由于作业过程中设备需承受高压、高温及复杂工况的考验,装备的可靠性和安全性直接决定了作业成败。因此,系统化、精准化的装备检测成为不压井作业的核心保障,需覆盖机械性能、密封性、耐腐蚀性及智能化控制等关键指标。
核心检测项目及技术要点
1. 防喷器系统(BOP)检测
防喷器是不压井作业的核心安全屏障,需重点检测其密封性能、压力承载能力和阀门响应速度。检测内容包括: - 环形防喷器(Annular BOP)橡胶胶芯的弹性恢复率和抗挤压能力; - 闸板防喷器(Ram BOP)的液压锁紧装置动作精度; - 全系统在额定压力(如70MPa)下的密封性测试,确保无泄漏。 检测需依据API 16A标准,结合氦气检漏、动态压力循环测试等方法。
2. 井下工具及连接部件检测
包括连续油管接头、液压震击器、安全阀等井下工具,检测重点为: - 金属材料的抗拉强度、疲劳寿命及耐硫化氢腐蚀性能; - 螺纹连接部位的密封性和抗扭矩能力; - 工具表面涂层完整性(如镀镍、渗碳处理),防止井下磨损。 采用无损检测技术(如超声波探伤、磁粉检测)并结合模拟井况的压力-温度循环试验。
3. 动态密封组件检测
针对作业中频繁动作的密封部件(如旋转防喷器动密封): - 检测密封材料(如聚四氟乙烯复合材料)的耐温范围(-20℃至150℃); - 模拟高频率往复运动(>1000次/小时)下的磨损量; - 高压流体(含砂、酸性介质)冲击下的密封失效阈值。
4. 液压控制系统检测
液压动力单元的稳定性和响应速度直接影响作业安全,检测需覆盖: - 液压泵输出压力波动范围(≤±2%额定压力); - 电磁阀切换时间(<50ms)及故障冗余机制; - 管线耐压强度(1.5倍工作压力保压30分钟无泄漏)。
5. 实时数据监测系统标定
集成式传感器网络(压力、温度、位移)需定期校准: - 压力传感器精度等级需达0.25%FS; - 井下工具定位误差≤±0.1m; - 数据传输延迟<100ms,确保地面控制中心实时掌握工况。
6. 腐蚀与疲劳寿命评估
通过金相分析、硬度测试和有限元模拟,预测装备在酸性环境(H₂S分压>0.3kPa)下的剩余寿命,重点关注: - 应力腐蚀裂纹(SCC)萌生风险; - 高周疲劳(>10⁶次循环)下的裂纹扩展速率; - 局部腐蚀速率(如点蚀深度>0.5mm/年需强制更换)。
7. 应急切断装置功能验证
模拟井喷、超压等极端工况,测试: - 剪切闸板切断油管的时间(<5秒); - 自动关井系统的触发阈值偏差(<5%设定值); - 应急电源(UPS)在断电后维持系统运行时间(≥30分钟)。
检测周期与标准化管理
依据API RP 5C7、SY/T 6160等行业规范,建立分级检测制度: - 日常作业前:快速功能测试(2小时/次); - 月度检测:关键部件性能核查(8小时/次); - 年度大修:全面解体检测(≥72小时),更新寿命评估数据库。 通过数字化检测平台实现数据追溯,动态优化维护策略,保障不压井作业装备始终处于最佳工况。
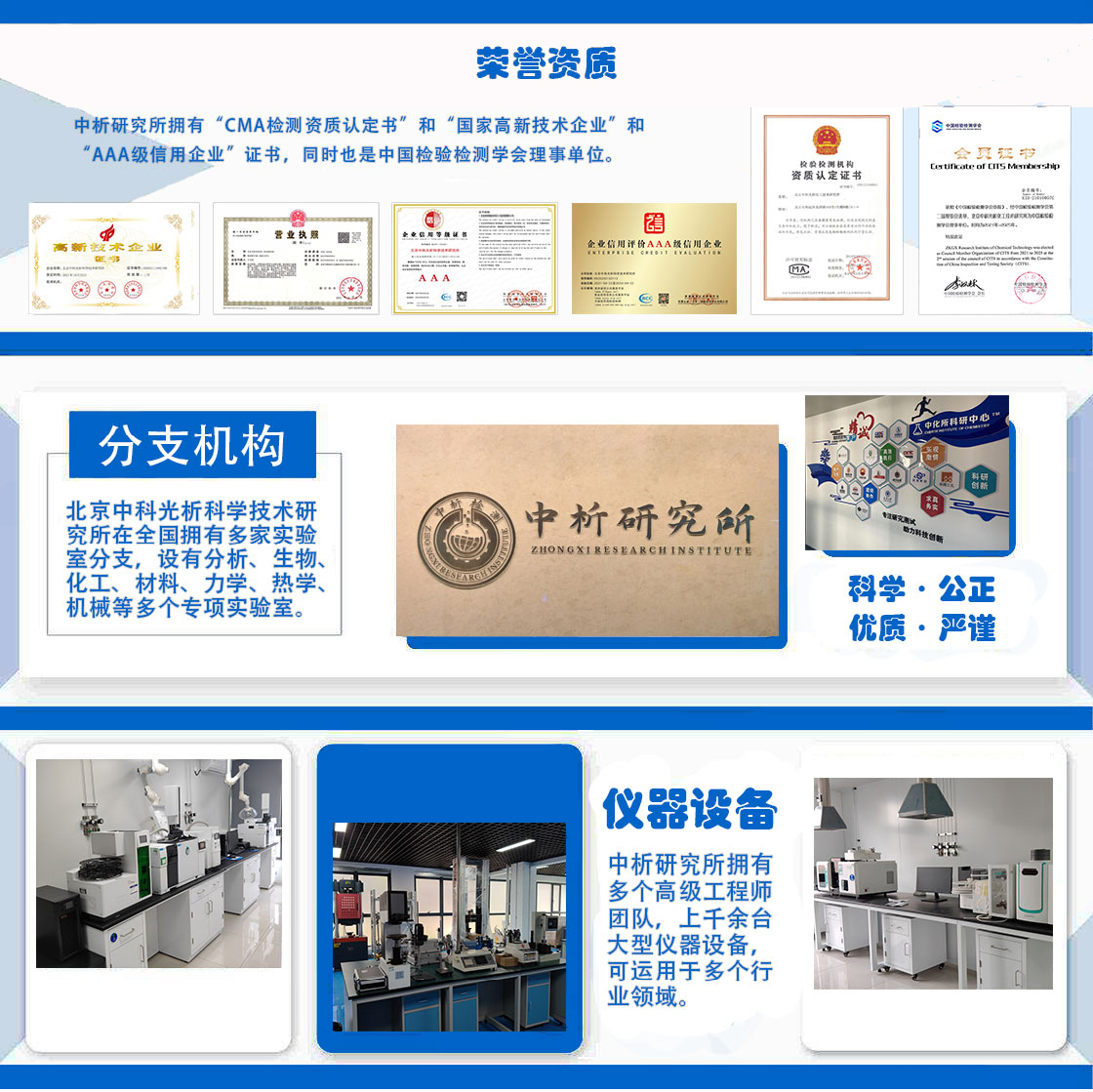
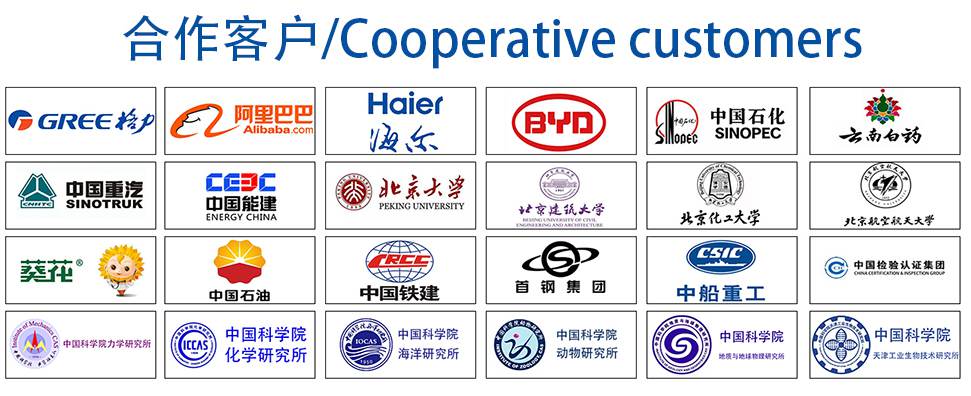