气密封井口检测系统检测
实验室拥有众多大型仪器及各类分析检测设备,研究所长期与各大企业、高校和科研院所保持合作伙伴关系,始终以科学研究为首任,以客户为中心,不断提高自身综合检测能力和水平,致力于成为全国科学材料研发领域服务平台。
立即咨询气密封井口检测系统的重要性与检测背景
气密封井口检测系统是石油天然气开采中保障井口安全的核心设备,其功能在于防止高压气体泄漏、控制井下压力并确保作业环境的稳定性。随着深层油气资源开发需求的增加,井口面临更高压力、腐蚀性介质及复杂工况的挑战,对气密封系统的可靠性提出了严苛要求。定期对气密封井口检测系统进行全面检测,不仅能够预防井喷、环境污染等重大事故,还能延长设备使用寿命,降低运维成本。
核心检测项目及技术要点
1. 压力密封性检测
通过模拟井口实际工况压力,使用液压/气压测试仪对密封组件进行分级加压测试,检测阀门、法兰连接处及密封圈的承压能力。重点记录压力衰减曲线,判断是否存在微泄漏(如采用氦质谱检测法精度可达10-9 mbar·L/s)。
2. 泄漏路径定位检测
运用红外热成像技术结合超声波泄漏检测仪,对井口装置进行三维扫描,精确定位微小泄漏点。通过对比环境温度与泄漏气体热辐射差异,可识别肉眼不可见的隐蔽缺陷。
3. 密封材料性能评估
对橡胶密封圈、金属垫片等关键材料进行实验室分析,包括硬度测试(邵氏A/D标度)、压缩永久变形率(ASTM D395标准)和耐介质腐蚀测试(模拟H2S/CO2环境),确保材料在极端条件下的稳定性。
4. 应急关断系统响应测试
通过故障注入法验证自动关断阀的响应时间和闭锁效能,要求从压力异常到完全关断不超过2秒,同时检测液压/电动执行机构的动作一致性,确保紧急状态下快速隔离井口。
5. 环境适应性检测
在温控舱内模拟-40℃至120℃极端温度循环,测试密封系统热胀冷缩特性;通过盐雾试验箱(ASTM B117标准)评估防腐涂层耐候性,确保系统在海洋平台等恶劣环境下的长期可靠性。
智能检测技术应用趋势
新一代检测系统集成物联网传感器和AI算法,可实现:① 在线振动监测分析密封件磨损状态;② 基于数字孪生的密封失效预测;③ 检测数据自动生成三维可视化报告。这些技术将传统定期检测升级为预防性智能运维,显著提升检测效率50%以上。
检测标准与合规要求
检测过程需严格遵循API 6A/17D、ISO 10423等国际标准,结合SY/T 5323等国内规范。检测报告应包含原始数据记录、缺陷位置图示、材料检测证书及改进建议,形成完整的质量追溯链条。
结语
气密封井口检测系统的全面检测是保障油气田安全生产的技术基石。通过多维度的检测项目组合与智能化技术应用,可有效识别潜在风险,为高含硫、超深井等复杂工况提供可靠保障。建议企业建立周期性检测制度,结合实时监测系统构建双重防护体系。
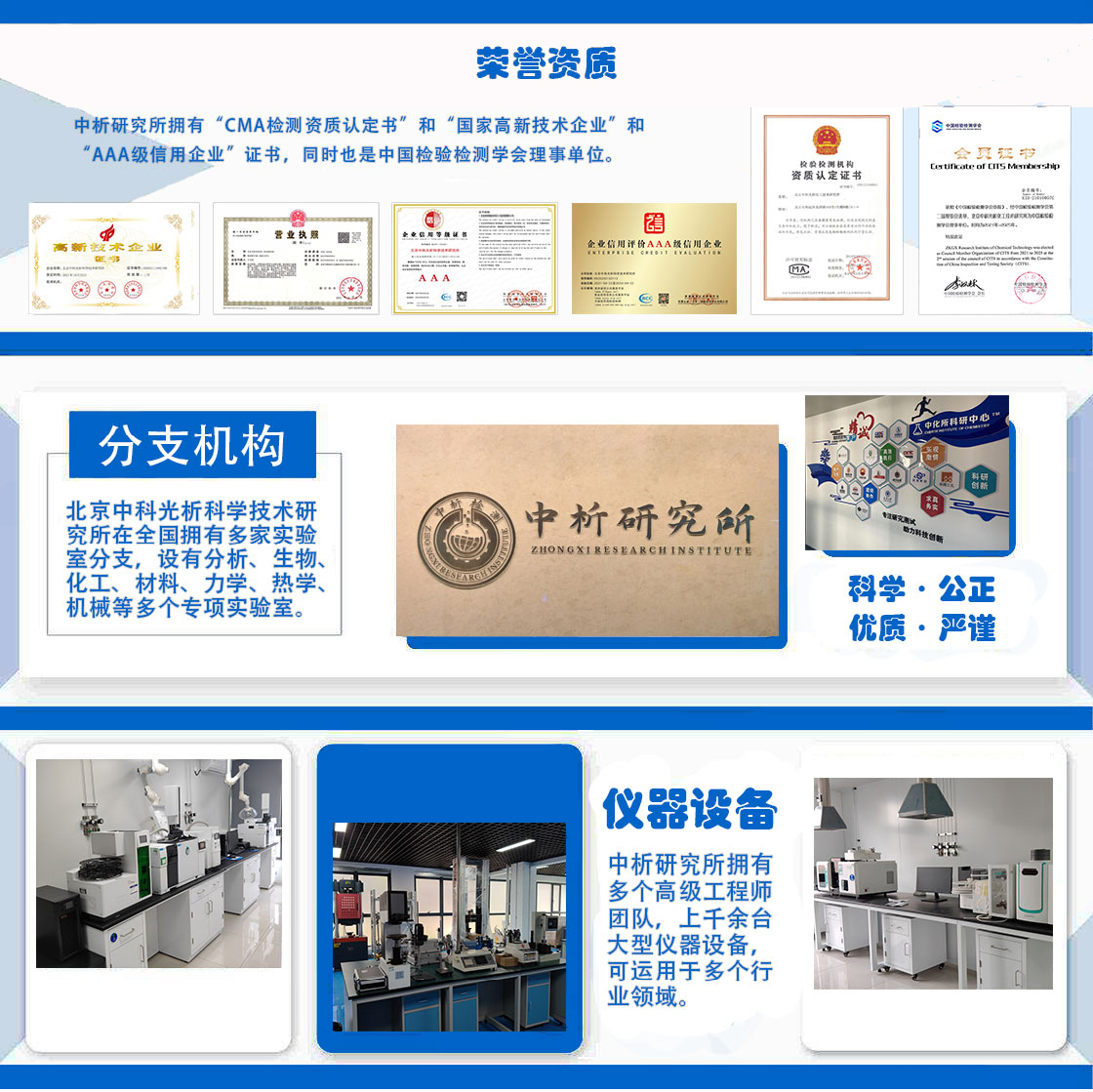
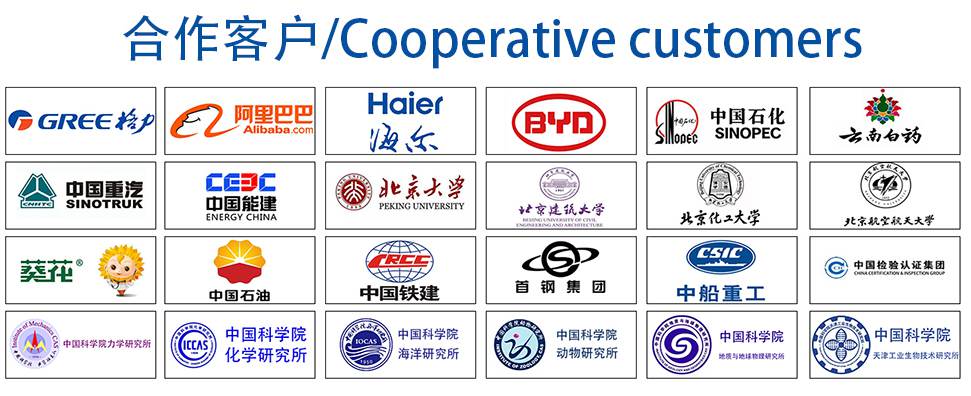