井下套管阀检测
实验室拥有众多大型仪器及各类分析检测设备,研究所长期与各大企业、高校和科研院所保持合作伙伴关系,始终以科学研究为首任,以客户为中心,不断提高自身综合检测能力和水平,致力于成为全国科学材料研发领域服务平台。
立即咨询井下套管阀检测的重要性与技术要点
井下套管阀是油气井完井过程中用于控制井下流体流动、保障井筒完整性的关键设备,广泛应用于高压、高温、腐蚀性介质的复杂工况中。长期运行中,套管阀可能受地层压力波动、化学腐蚀、机械磨损等因素影响,导致密封失效、阀体变形或驱动机构故障,进而引发井控风险或生产事故。因此,定期开展井下套管阀检测是确保油气井安全运行、延长设备使用寿命的核心环节。检测项目需覆盖阀体结构、材料性能、密封能力及动态响应等多个维度,并借助专业工具和技术手段实现精准评估。
井下套管阀检测的主要项目
1. 阀体密封性能检测
通过加压试验验证套管阀的密封能力,利用氮气或水介质对阀体施加额定工作压力的1.25-1.5倍,监测压力保持时间与泄漏量。重点关注阀座与阀板接触面、阀杆密封处的渗漏情况,配合荧光检漏剂或声发射技术定位微观缺陷。
2. 腐蚀与磨损评估
采用超声波测厚仪、电磁涡流探伤仪对阀体及关键部位进行壁厚测量,结合内窥镜观察内腔腐蚀形貌。针对高含硫井况,需额外开展硫化氢应力腐蚀开裂(SSC)敏感性测试,使用金相显微镜分析材料微观组织变化。
3. 阀体材料强度验证
通过硬度测试、拉伸试验和冲击韧性检测评估材料力学性能,对比原始出厂参数判断是否存在强度衰减。对于焊接部位,需进行X射线或超声波探伤(UT)检查焊缝完整性。
4. 驱动机构功能测试
模拟井下实际工况,检测液压/机械驱动系统的响应速度、扭矩输出和行程精度。通过循环开关试验验证执行器在高温(150℃+)高压(70MPa+)环境中的动作可靠性,记录卡滞、延迟等异常现象。
5. 压力-温度循环试验
在实验室模拟井筒压力与温度交变条件(如0-100MPa压力波动、20-180℃温度循环),持续监测阀体变形量和密封性能变化,评估其抗疲劳特性与工况适应能力。
6. 几何尺寸与形变检测
使用三维激光扫描仪获取阀体全尺寸点云数据,对比设计图纸检测形变量;利用专用通径规检查阀腔流道内径,确保满足井下工具通过性要求,公差需控制在API标准范围内。
检测技术的发展趋势
随着智能化技术的应用,基于物联网的在线监测系统可通过井下传感器实时采集压力、温度、振动数据,结合机器学习算法预测套管阀剩余寿命。同时,全自动检测机器人可替代人工完成高风险井况下的精细化操作,显著提升检测效率与安全性。
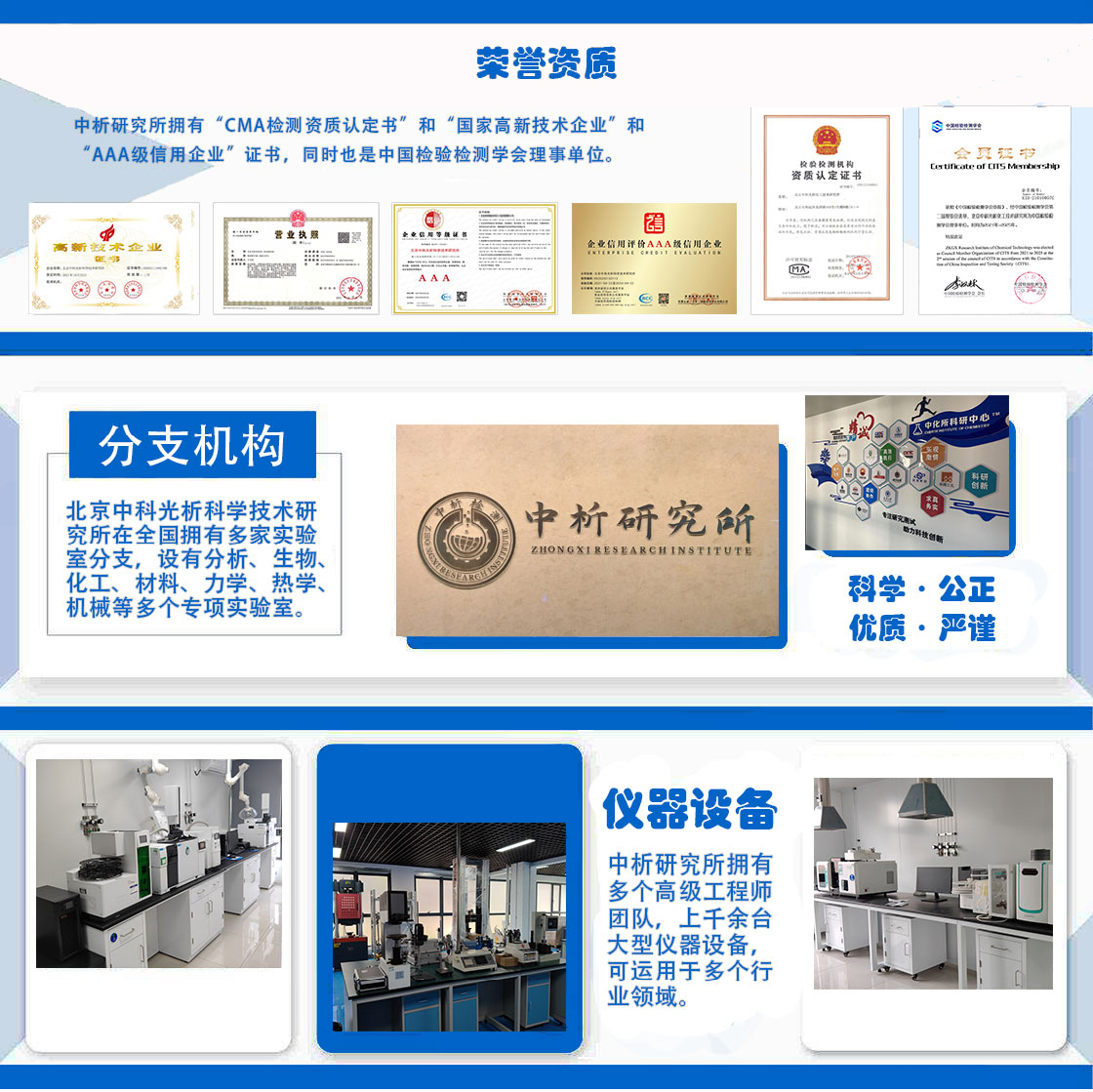
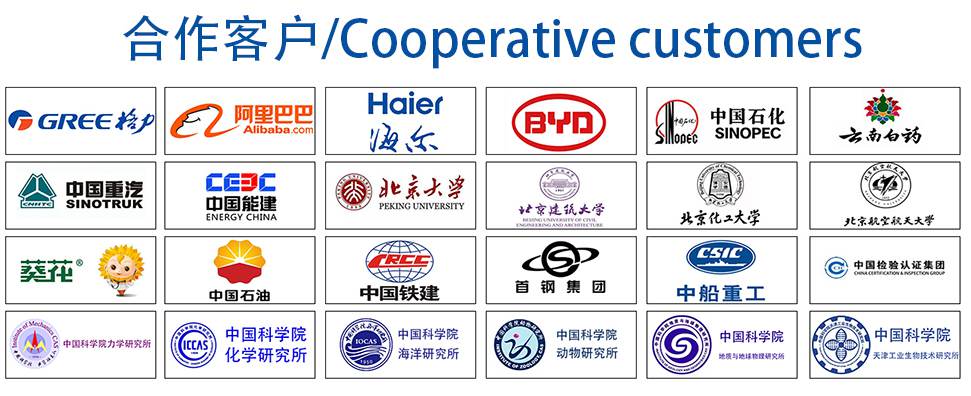