第一类第二类中压力容器检测
实验室拥有众多大型仪器及各类分析检测设备,研究所长期与各大企业、高校和科研院所保持合作伙伴关系,始终以科学研究为首任,以客户为中心,不断提高自身综合检测能力和水平,致力于成为全国科学材料研发领域服务平台。
立即咨询第一类与第二类中压力容器检测项目详解
中压力容器是工业生产中广泛使用的特种设备,根据《固定式压力容器安全技术监察规程》(TSG 21-2016)的分类标准,其按介质危害性、设计压力和容积等因素分为第一类、第二类和第三类。本文重点针对第一类和第二类中压力容器的检测项目展开说明,帮助使用单位明确检测要求,确保设备安全运行。
一、第一类中压力容器检测项目
第一类压力容器通常指介质危害性较低(非易燃、无毒)且设计压力≤1.6MPa的容器。其核心检测内容包括:
1. 外观与宏观检查:重点检测容器表面腐蚀、变形、焊缝缺陷及密封面完整性,使用测厚仪对关键部位进行壁厚测量;
2. 安全附件校验:包括压力表、安全阀的校准及泄压功能测试,确保动作压力符合设计要求;
3. 材质复验:对主体材料的化学成分、力学性能进行抽样检测,验证是否符合原设计标准;
4. 耐压试验:采用水压试验(试验压力为设计压力的1.25倍)或气压试验(需严格安全防护),持续保压时间≥30分钟。
二、第二类中压力容器检测项目
第二类压力容器涉及易燃、有毒介质或更高设计压力(1.6MPa<P≤10MPa),检测要求更为严格,需增加以下项目:
1. 无损检测(NDT)扩展:对焊缝进行100%射线检测(RT)或超声波检测(UT),重点区域采用TOFD或相控阵技术;
2. 应力分析:通过有限元模拟或应变片测试,评估高应力区域的疲劳寿命和承载能力;
3. 介质残留检测:使用气体检测仪对有毒/易燃介质残留量进行定量分析,确保检修安全;
4. 腐蚀监测:针对内壁腐蚀情况,采用内窥镜检查或腐蚀挂片法,建立腐蚀速率预测模型;
5. 紧急切断装置测试:验证快开门联锁装置、紧急泄放系统的响应速度和可靠性。
三、检测周期与注意事项
第一类容器定期检验周期一般为6年,第二类缩短至4年,高危工况需加密检测。检测过程中需遵循以下原则:
1. 检测前需彻底清洗置换容器,排除介质干扰;
2. 采用经CMA/ 认证的检测机构,确保数据权威性;
3. 对检测发现的局部减薄、裂纹等缺陷,按《承压设备损伤模式判定》标准进行安全评级;
4. 建立数字化检测档案,实现全生命周期管理。
通过科学的分类检测,可显著降低压力容器运行风险,同时避免过度检测造成的资源浪费。企业需结合设备实际工况,动态调整检测策略,切实保障特种设备安全。
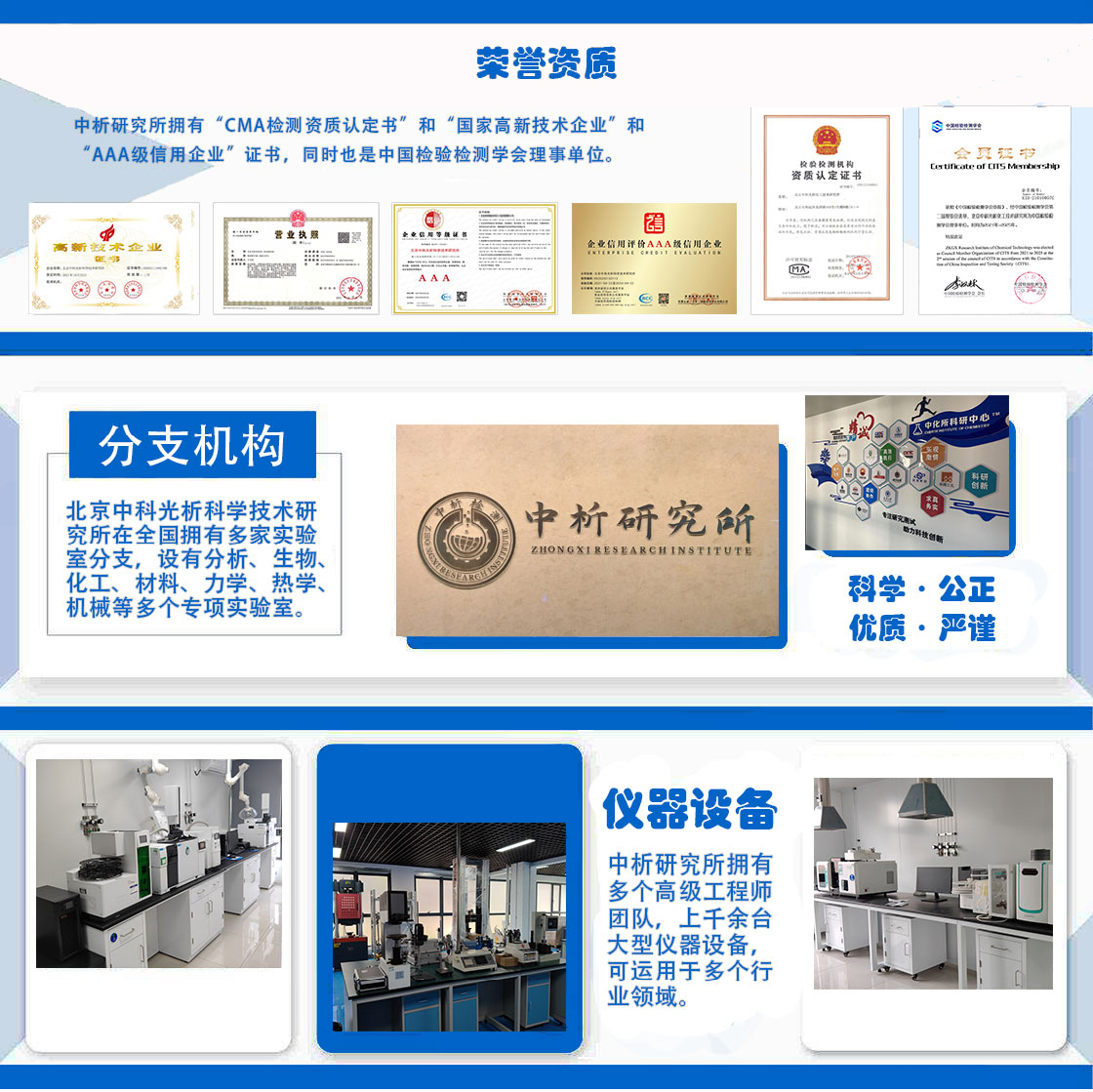
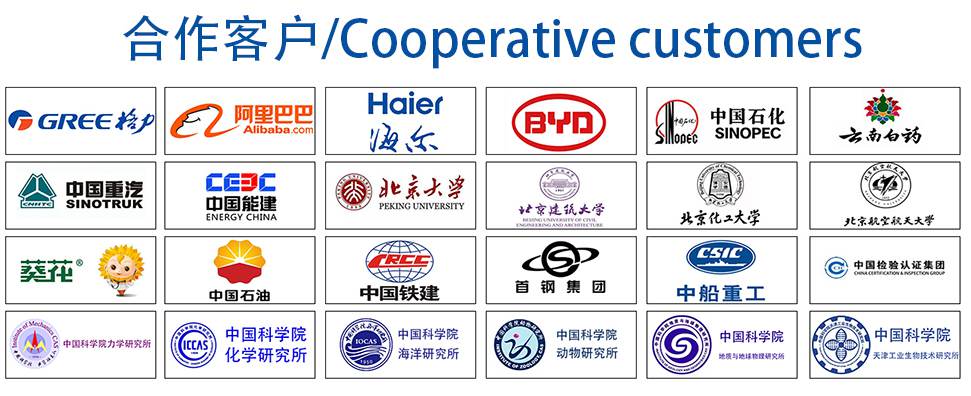