抽油喷焊光杆检测
实验室拥有众多大型仪器及各类分析检测设备,研究所长期与各大企业、高校和科研院所保持合作伙伴关系,始终以科学研究为首任,以客户为中心,不断提高自身综合检测能力和水平,致力于成为全国科学材料研发领域服务平台。
立即咨询抽油喷焊光杆检测的重要性及核心项目分析
抽油喷焊光杆作为石油开采设备中抽油机系统的关键部件,其性能直接影响油井采油效率和设备运行安全性。由于长期承受交变载荷、腐蚀介质和高温高压环境,光杆的焊接质量、材料性能和表面处理工艺必须达到行业标准。定期开展专业检测可有效预防断裂、磨损等故障,延长设备使用寿命并降低维护成本。检测过程需依据API Spec 11B、SY/T 5497等标准,通过科学的检测手段对光杆的物理化学性能进行全面评估。
核心检测项目及技术要求
1. 材料成分与金相组织检测
通过光谱分析仪检测光杆基材和喷焊层的化学成分,验证是否满足35CrMo、42CrMo等合金钢材质标准。同步开展金相显微分析,观察晶粒度、夹杂物分布及喷焊层与基体的熔合状态,确保无未熔合、裂纹等缺陷。
2. 焊接质量综合检测
采用超声波探伤(UT)和磁粉探伤(MT)检测焊道连续性,重点排查热影响区裂纹、气孔等缺陷。使用硬度计测量焊缝区、热影响区和母材的维氏硬度梯度,确保硬度差异不超过HV50,避免应力集中。
3. 几何尺寸与形位公差检测
使用三坐标测量仪对光杆的直径公差(通常要求±0.1mm)、直线度(≤0.3mm/m)、螺纹配合精度进行三维测量,同时检查喷焊层厚度均匀性(目标值1.5-2.5mm)。
4. 表面处理与耐蚀性检测
通过盐雾试验评估镀层或喷涂层的耐腐蚀性能,要求中性盐雾试验500小时无红锈。使用表面粗糙度仪检测喷焊层Ra值(控制在0.8-1.6μm),并采用涡流检测排查表面微裂纹。
5. 力学性能测试
进行拉伸试验(抗拉强度≥930MPa)、冲击试验(-20℃下Akv≥40J)和扭转试验(扭矩≥6000N·m),验证材料在极端工况下的承载能力。同步开展疲劳寿命测试,模拟10^7次交变载荷下的性能衰减情况。
6. 无损探伤与缺陷评级
综合应用工业CT扫描和相控阵超声检测技术,建立三维缺陷图谱,根据ISO 5817标准对气孔、夹渣等缺陷进行分级评定,确保所有缺陷均符合B级验收标准。
检测结果应用与质量管控
所有检测数据需建立数字化档案,通过SPC统计过程控制分析生产质量趋势。对于失效件应进行断口SEM分析,追溯失效机理。建议每12个月开展周期性检测,在含硫油井等恶劣环境中应缩短至6个月检测周期,确保设备安全高效运行。
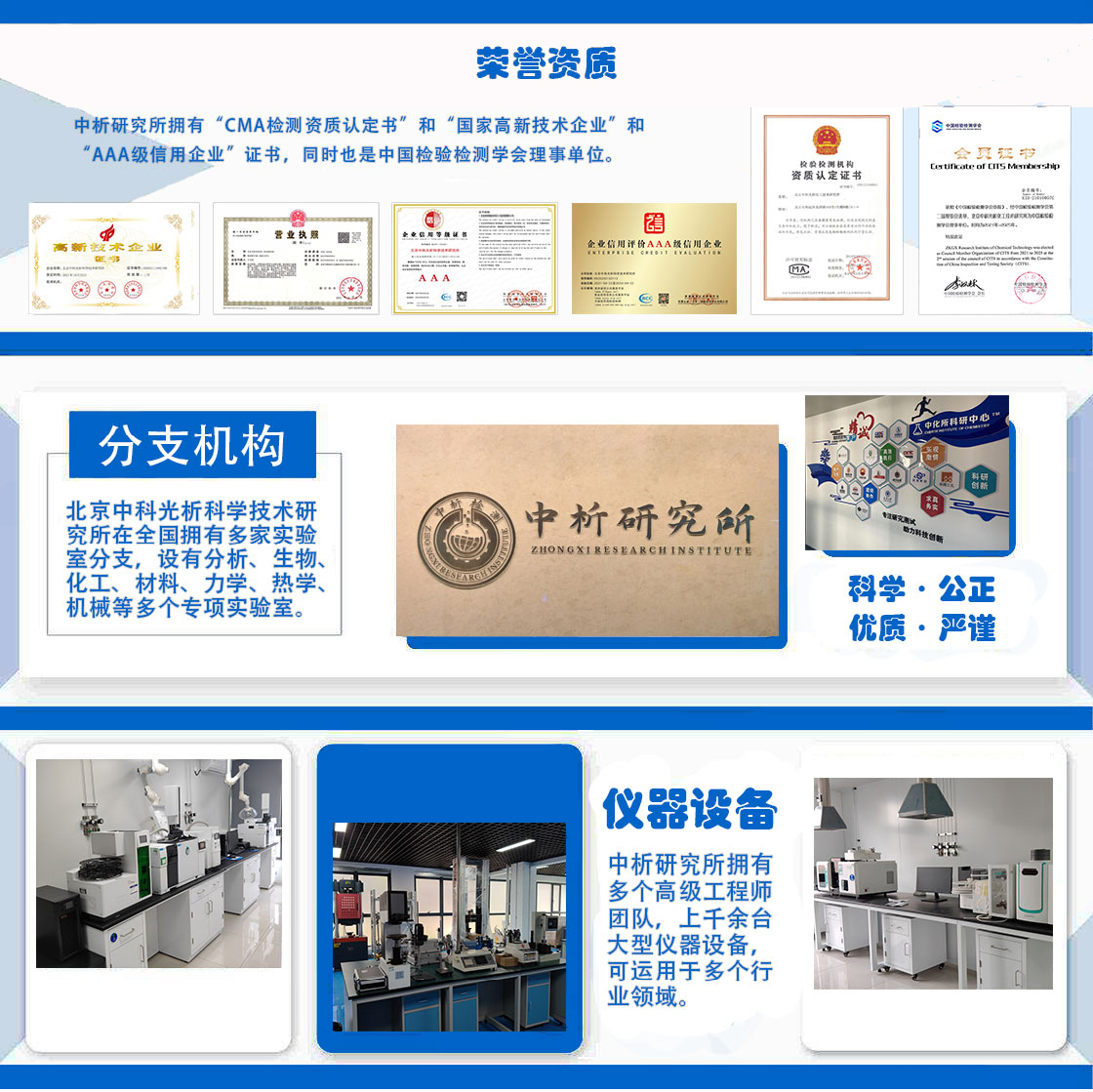
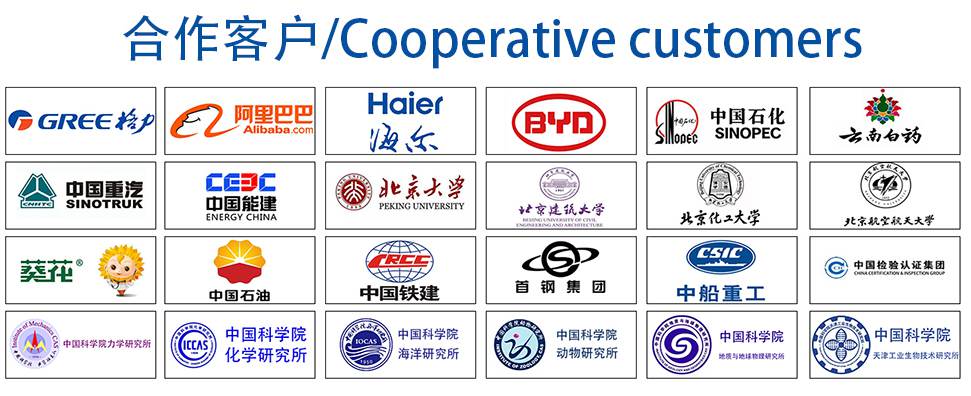