洗井设备检测
实验室拥有众多大型仪器及各类分析检测设备,研究所长期与各大企业、高校和科研院所保持合作伙伴关系,始终以科学研究为首任,以客户为中心,不断提高自身综合检测能力和水平,致力于成为全国科学材料研发领域服务平台。
立即咨询洗井设备检测的必要性与流程解析
洗井设备作为石油开采、水文地质勘探及地下水修复等领域的关键装备,其运行状态直接关系到作业效率与安全性。长期使用过程中,设备可能因磨损、腐蚀、结垢或部件老化等问题导致性能下降,甚至引发井下事故。因此,定期开展洗井设备检测是保障设备稳定运行、延长使用寿命的核心措施。通过系统化的检测项目,可精准识别潜在隐患,优化维护方案,避免因设备故障造成的生产停滞和经济损失。
核心检测项目清单
1. 机械结构完整性检测
重点检查洗井泵、高压管线、喷头组件等核心部件的磨损、变形及裂纹情况。使用超声波探伤仪、磁粉检测仪等工具对金属部件进行非破坏性检测,评估承压能力是否符合行业标准(如API标准)。同时验证法兰连接处密封性,防止高压作业时发生泄漏。
2. 动力系统性能测试
通过加载试验分析柴油机或电动机的输出功率、转速稳定性及燃油效率,监测是否存在异常振动或过热现象。检测液压系统油压波动范围,确保阀门响应速度在0.5秒以内,流量计精度误差不超过±2%。
3. 清洗效率与压力参数验证
采用流量-压力联测法评估设备清洗能力,要求额定压力下(通常15-50MPa)射流冲击力达到设计值的90%以上。对旋喷装置的覆盖角度进行实地测试,确保井壁清洗无死角,同时记录不同介质(清水/化学药剂)下的清洗效率对比数据。
4. 控制系统与安全装置检测
全面检查PLC控制模块的指令响应速度和逻辑控制精度,测试紧急停机装置在0.3秒内的触发可靠性。校准压力传感器、温度传感器等监测元件,确保误差范围≤1.5%FS,并验证过载保护功能的实际生效阈值。
5. 防腐与材质退化评估
对接触酸碱性介质的部件进行金相分析,检测铬、镍等合金涂层的厚度损耗(应≥设计厚度的80%)。利用电化学工作站测量关键部位的腐蚀速率,结合井下工况预测剩余使用寿命,提出镀层修复或材质升级建议。
检测周期与执行标准
常规检测应每6个月进行一次全面检测,高强度作业环境下需缩短至3个月。检测流程需严格遵循SY/T 5587.5《油田专用车辆及设备检测规程》、GB/T 28911《石油天然气工业井下工具检测与修复》等标准,同时结合设备制造商的技术规范制定个性化检测方案。
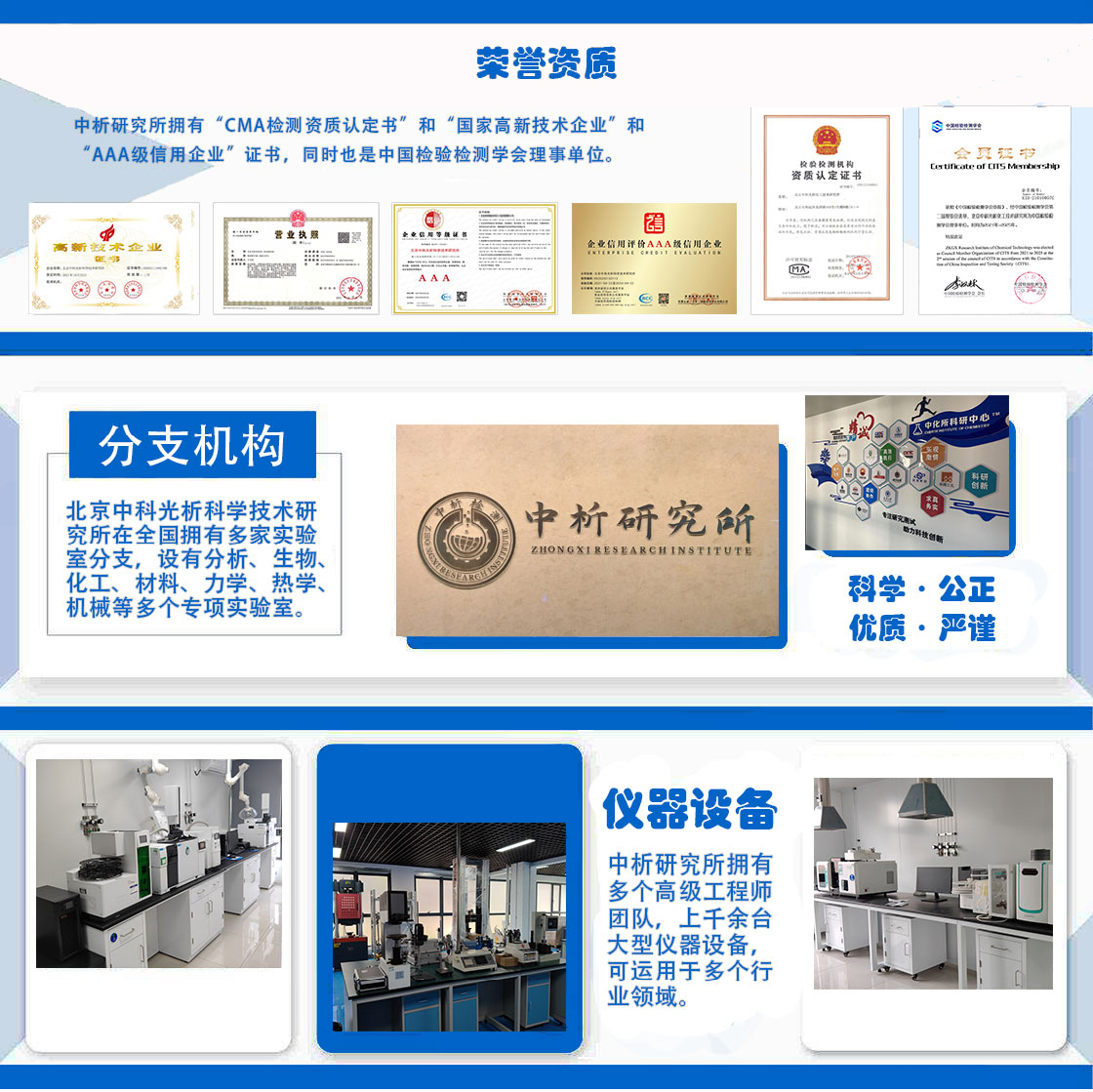
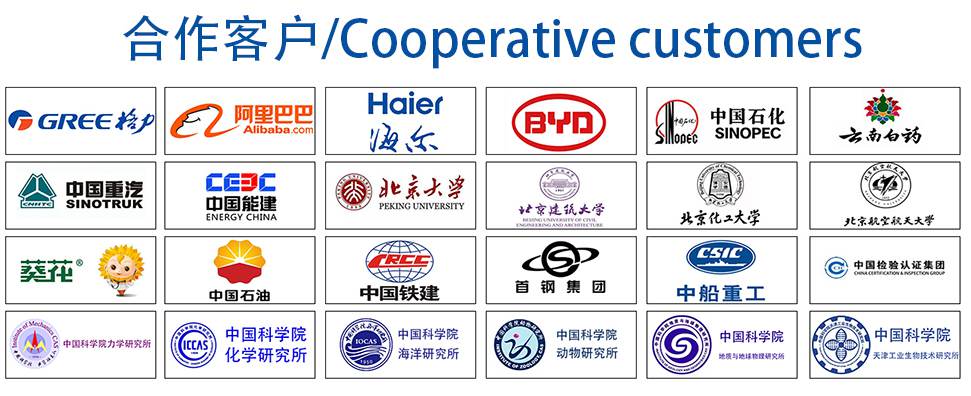