放喷管线检测的重要性及背景
放喷管线是石油天然气行业中用于控制井喷、泄压及应急处理的关键设备,通常由高压管道、阀门、连接件等组成。在钻井、完井或修井作业中,放喷管线直接承受高温、高压、腐蚀性介质(如硫化氢、二氧化碳)以及砂粒冲刷的复杂工况。若管线存在缺陷或失效,可能导致严重的安全事故,如泄漏、爆炸或环境污染。因此,定期对放喷管线进行系统性检测是保障作业安全、延长设备寿命的核心环节。
放喷管线检测的核心项目
放喷管线的检测需覆盖材料完整性、连接可靠性及功能稳定性等多个维度,具体包括以下关键项目:
1. 管线壁厚与腐蚀检测
通过超声波测厚仪或射线检测技术,测量管线关键部位的剩余壁厚,评估腐蚀、冲蚀或机械损伤程度。重点检测弯头、焊缝及阀门连接处等易损区域,结合历史数据判断腐蚀速率,确定是否需要补强或更换。
2. 焊缝质量与缺陷分析
利用渗透检测(PT)、磁粉检测(MT)或相控阵超声(PAUT)等技术,检查焊缝是否存在裂纹、未熔合、气孔等缺陷。对高压段焊缝需进行100%全覆盖检测,确保其承压能力符合API 16C或行业相关标准。
3. 密封性能与压力测试
通过液压试验或气密性试验验证管线的密封性。通常采用1.25倍工作压力进行保压测试,监测压力降是否在允许范围内。同时检查法兰、螺纹接头及阀门密封面是否泄漏,确保紧急情况下能够可靠封堵。
4. 支撑结构与固定装置检查
评估管线支架、地脚螺栓及固定卡箍的稳固性,确认其是否因振动或地基沉降发生位移或变形。支撑结构失效可能导致管线弯曲应力集中,进而引发疲劳裂纹。
5. 材质性能退化评估
针对长期服役的管线,采用硬度测试、金相分析或光谱检测等方法,判断材料是否因氢脆、硫化物应力腐蚀开裂(SSCC)或高温蠕变导致性能下降。必要时取样进行实验室理化分析。
6. 附属设备功能性验证
检查放喷管线配套的节流阀、阻火器、火炬头等设备的工作状态,测试阀门启闭灵活性及远程控制系统的响应能力,确保应急情况下能快速启动泄压流程。
检测周期与标准依据
根据API RP 53、SY/T 5323等标准,常规检测周期为1年(高风险工况缩短至6个月)。检测后需形成详细报告,标注缺陷位置、等级及修复建议,并建立全生命周期管理档案,为后续维护提供数据支持。
通过系统化的检测与维护,可显著降低放喷管线失效风险,保障油气田作业安全,同时减少非计划性停机带来的经济损失。
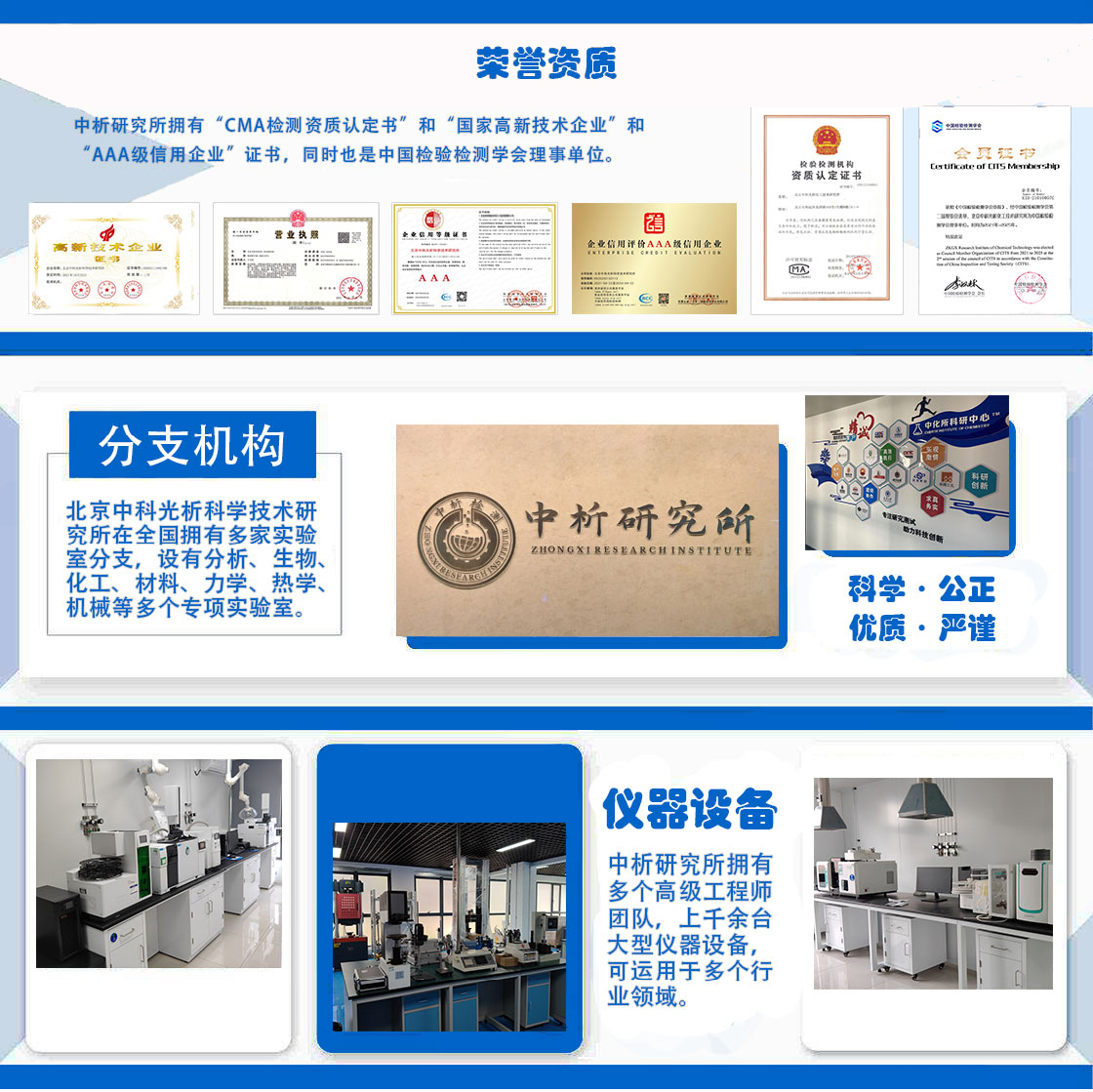
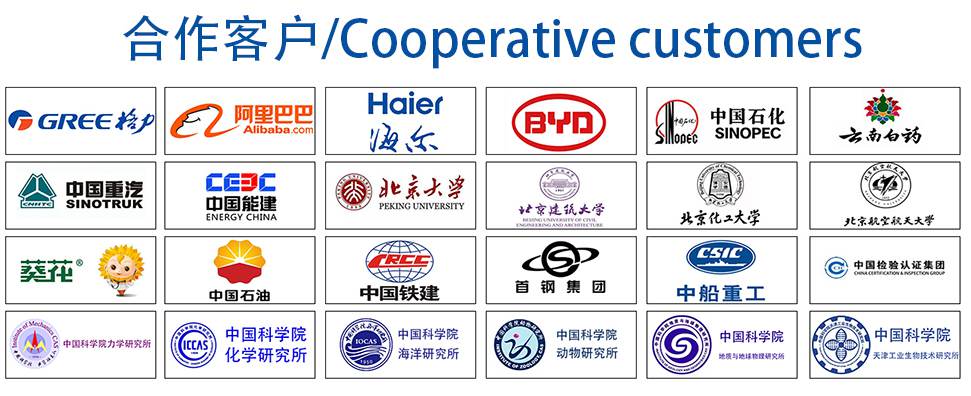