钻井和修井动力钳、吊钳检测的重要性
在石油钻井和修井作业中,动力钳与吊钳是保障高效、安全作业的核心设备。动力钳主要用于管柱的旋转和紧扣/卸扣操作,而吊钳则承担着管柱的夹持与固定功能。由于作业环境复杂、负载强度高且连续运转时间长,这些设备的性能可靠性直接关系到现场作业的安全性和效率。若动力钳或吊钳出现裂纹、磨损或功能失效,轻则导致停工损失,重则可能引发严重事故。因此,定期开展专业检测是设备管理中不可或缺的环节。
动力钳与吊钳核心检测项目
1. 外观与结构完整性检测
通过目视检查、超声波探伤和磁粉检测技术,评估钳体、牙板、传动部件是否存在裂纹、变形或腐蚀。重点检查受力集中区域(如钳头连接处、液压缸固定点)的结构完整性,同时验证螺栓紧固状态和防松装置的有效性。
2. 动态性能测试
使用扭矩标定装置模拟实际工况,测量动力钳的最大扭矩输出和精度偏差。通过载荷试验验证吊钳的夹持力保持能力,检查牙板在不同管径下的咬合深度和防滑性能。测试需覆盖设备全负荷范围的90%-110%,确保超载保护系统响应灵敏。
3. 液压与控制系统检测
对液压动力单元的油压稳定性、流量匹配性进行动态监测,检查密封件是否存在渗漏。通过控制阀组响应测试,验证操作手柄的灵敏度及换向功能的可靠性。针对电控型设备,还需检测PLC系统逻辑控制和故障诊断功能。
4. 安全防护装置验证
系统测试安全销、过载泄压阀、紧急制动装置等保护机构的触发阈值和动作时效性。模拟突发断电、液压失压等异常工况,确认防反转装置和机械自锁功能的可靠性,评估二次防护系统的有效性。
检测流程与技术规范
标准化检测应按照API 7K(钻井设备规范)和SY/T 5532(石油钻采设备检测规程)执行,采用三维应力分析、动态应力测试仪等齐全手段。检测周期需结合设备使用频率,常规作业条件下建议每600小时或单井作业结束后进行全面检测,极端工况需缩短至300小时。
检测结果分析与应用
专业机构出具的检测报告需包含设备健康评级、剩余寿命预测和维修建议。对于关键部件(如钳牙、主轴承)的磨损量超过原尺寸5%的情况,应强制更换。通过大数据分析历史检测数据,可建立设备性能衰退模型,为预防性维护提供科学依据。
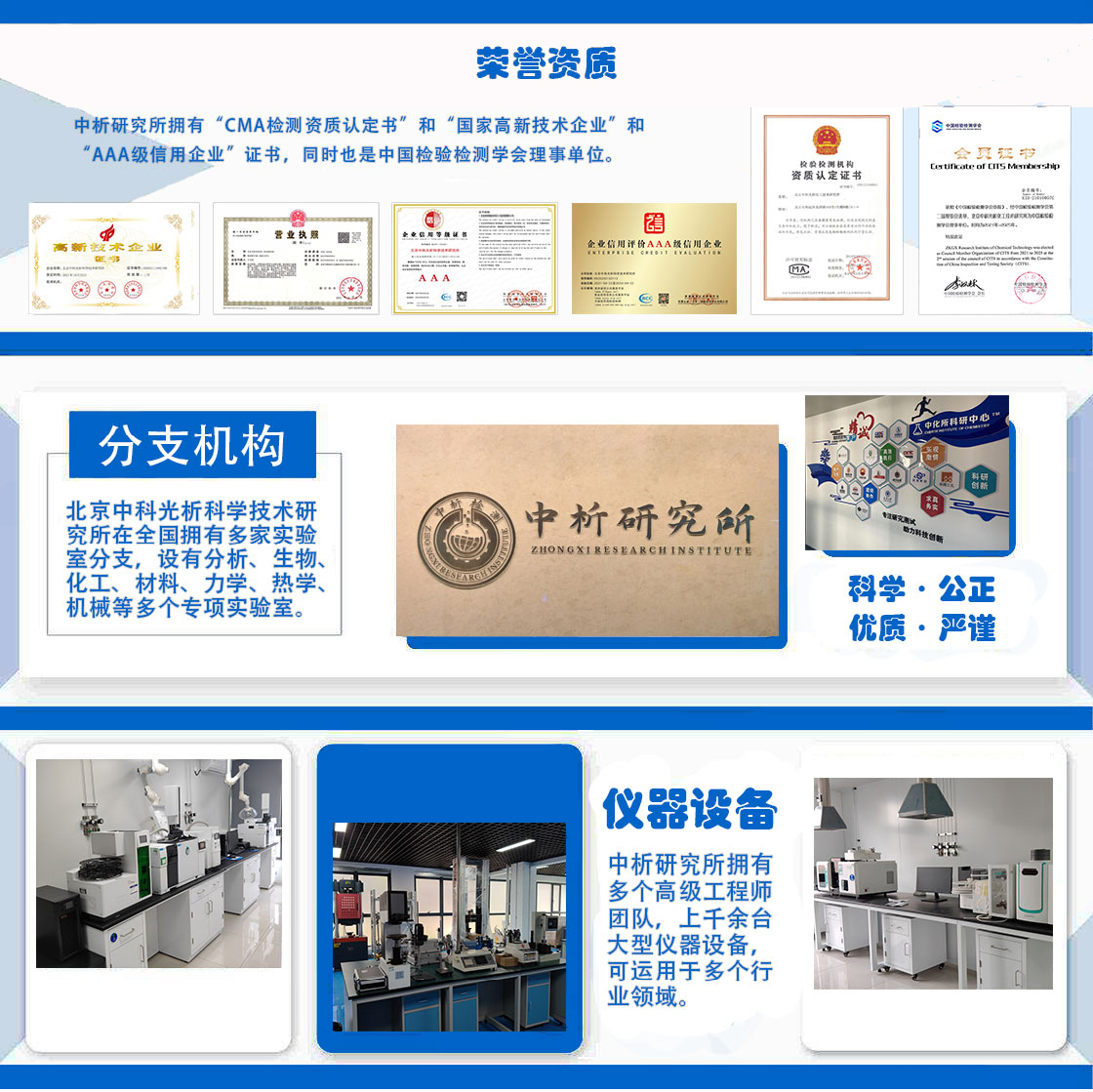
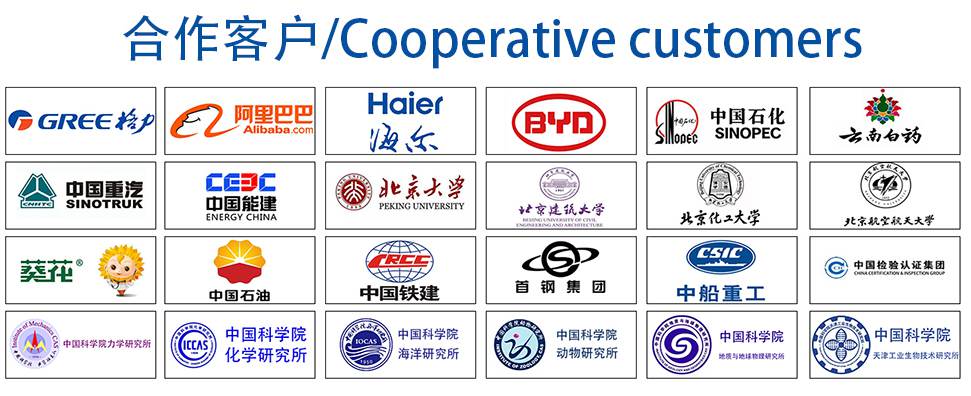