钢铁及合金化学成分检测的重要性
钢铁及合金作为现代工业的基础材料,其性能直接取决于化学成分的配比与纯度。化学成分检测是确保材料满足设计需求、应用场景及国际标准的核心环节。通过精确分析材料中各类元素的含量,可以评估其力学性能(如强度、硬度)、耐腐蚀性、焊接性及加工性能等关键指标。此外,在原材料采购、生产过程控制、成品验收及失效分析等环节中,化学成分检测均起到不可替代的作用,是保障产品质量和合规性的关键手段。
常规元素的检测项目
常规检测元素包括碳(C)、硅(Si)、锰(Mn)、硫(S)、磷(P)五大基础成分。碳含量直接影响钢铁的硬度和强度,例如低碳钢(C≤0.25%)适用于冷加工,而高碳钢(C≥0.6%)多用于工具制造;硅和锰作为脱氧剂和强化元素,可改善材料的热处理性能;硫和磷则是需要严格控制的杂质元素,含量过高会导致热脆性和冷脆性,降低材料韧性。检测方法常采用光谱分析(OES)、化学滴定法及X射线荧光光谱法(XRF)。
合金元素的检测项目
合金钢及特殊钢的检测需重点关注添加的合金元素,如铬(Cr)、镍(Ni)、钼(Mo)、钒(V)、钛(Ti)等。铬是提高耐腐蚀性和抗氧化性的核心元素(如不锈钢中Cr≥10.5%);镍能增强低温韧性及抗酸蚀能力;钼可细化晶粒并提升高温强度;钒和钛则通过形成碳化物改善耐磨性。这些元素的含量需严格遵循国标(GB/T 223系列)、ASTM或ISO标准,通过电感耦合等离子体发射光谱法(ICP-OES)或质谱法(ICP-MS)进行定量分析。
有害元素与痕量元素的检测
有害元素如砷(As)、锡(Sn)、锑(Sb)、铅(Pb)等需进行痕量检测(通常要求≤0.005%)。这类元素在高温或应力环境下易引发晶界偏析,导致材料脆化或腐蚀加速。例如,残余铜(Cu)在热轧过程中可能引起表面裂纹。痕量检测需使用高灵敏度仪器,如辉光放电质谱(GD-MS)或原子吸收光谱(AAS)。此外,气体元素(氢、氧、氮)的检测对高端合金(如轴承钢、航空航天材料)尤为重要,氢含量超标会导致氢脆失效。
其他检测项目与标准依据
除元素分析外,还需结合材料用途进行综合评估,例如通过碳当量(CE)公式预测焊接性能,或计算铬当量/镍当量以评估不锈钢的相组成。检测标准依据包括GB/T 223(中国)、ASTM E415(美国)、ISO 4948(国际)等。检测机构需配备CMA/ 资质,并采用标准物质进行数据校准,确保结果准确可靠。
综上所述,钢铁及合金的化学成分检测是材料科学与工业应用的关键纽带。通过全面覆盖基础元素、合金成分及痕量有害物质的检测,可精准把控材料性能,为研发、生产及质量控制提供科学依据。
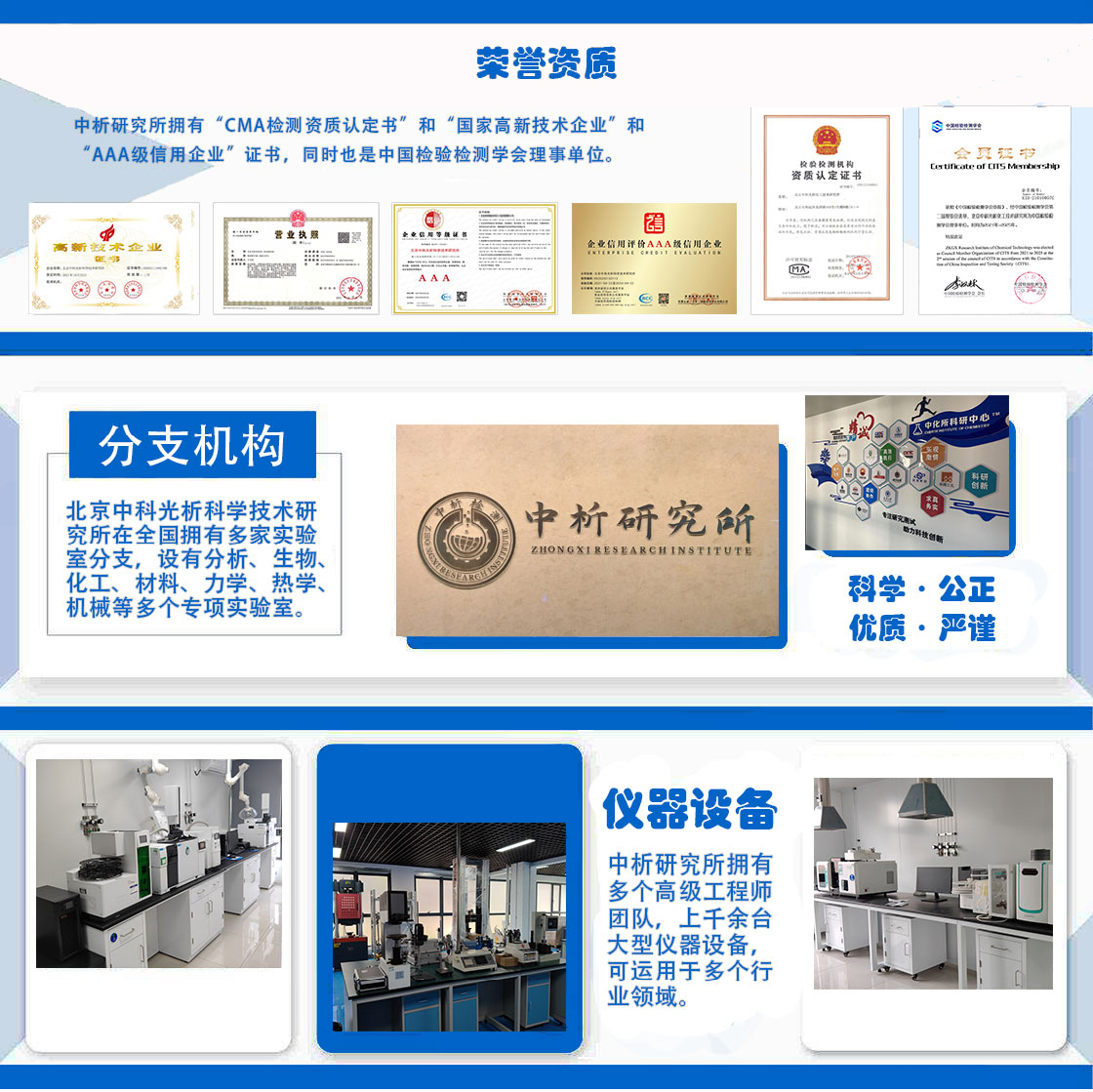
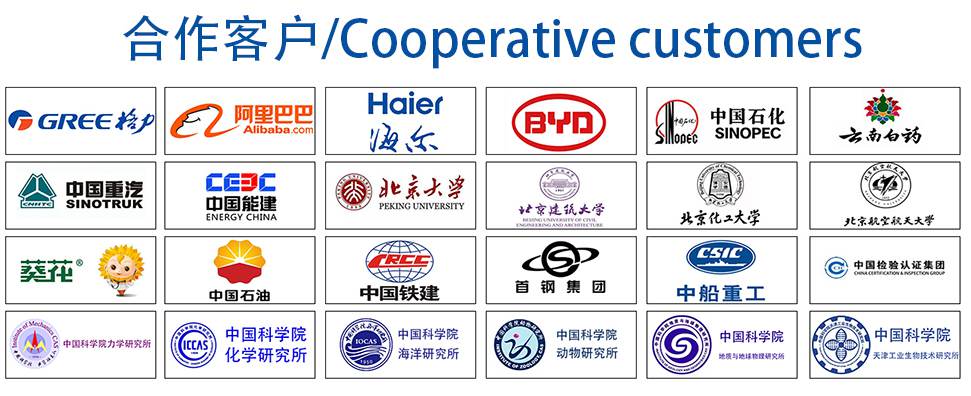