机械零部件(参数)检测的重要性与核心内容
在机械制造领域,零部件的参数检测是确保产品质量、性能和安全性的关键环节。随着工业自动化水平的提升,机械设备的精密性要求日益严格,任何微小的尺寸偏差、材料缺陷或装配误差都可能导致设备失效、能耗增加甚至安全事故。因此,机械零部件的参数检测贯穿于设计验证、生产加工、成品验收及维护保养的全生命周期,其核心目标是通过科学严谨的检测手段,量化评估零部件是否符合设计规范、行业标准及实际工况需求。
核心检测项目及技术方法
1. 尺寸精度检测
尺寸精度是机械零部件的基础参数,直接影响装配匹配性和功能实现。检测项目包括:
- **几何尺寸**:如长度、直径、孔径、螺纹参数等,使用三坐标测量仪(CMM)、光学投影仪或激光扫描仪进行高精度测量;
- **公差配合**:通过塞规、环规等量具验证孔轴配合间隙,确保符合ISO或GB公差标准。
2. 形位公差检测
形位公差反映零部件的形状与位置偏差,常见检测项包括:
- **平面度**:采用平晶干涉法或激光平面仪;
- **圆度/圆柱度**:使用圆度仪或CMM多点采样分析;
- **同轴度/垂直度**:借助精密转台配合千分表或光学对中仪进行测量。
3. 材料性能检测
材料性能决定零部件的强度、耐磨性和使用寿命,关键检测内容涵盖:
- **力学性能**:如硬度(洛氏/布氏硬度计)、抗拉强度(万能试验机)、冲击韧性(夏比冲击试验机);
- **化学成分**:通过光谱分析仪或X射线荧光仪验证材料元素配比;
- **金相组织**:利用金相显微镜观察晶粒度、夹杂物分布及热处理效果。
4. 表面质量与处理检测
表面特性影响零部件的耐磨、防腐及疲劳寿命,主要检测项目包括:
- **粗糙度**:使用触针式粗糙度仪或白光干涉仪量化Ra、Rz值;
- **涂层厚度**:通过涡流测厚仪或X射线荧光法检测镀层/涂层均匀性;
- **表面缺陷**:借助工业内窥镜、磁粉探伤或超声波探伤识别裂纹、气孔等缺陷。
5. 功能性及动态性能检测
针对特定工况的零部件需进行功能性验证:
- **密封性测试**:通过气压/液压试验检测阀门、管件的泄漏率;
- **动态平衡**:使用动平衡机校正旋转件的偏心量;
- **疲劳寿命**:在振动台或高频疲劳试验机上模拟长期载荷下的耐久性。
检测技术的发展趋势
随着工业4.0的推进,机械零部件检测正朝着智能化、非接触化方向发展。例如,基于机器视觉的自动测量系统可实时监控生产线上的零件质量,而AI算法能够对检测数据进行趋势预测和异常预警。此外,便携式检测设备(如手持式3D扫描仪)的普及,为现场维护和快速诊断提供了高效解决方案。
结语
机械零部件的参数检测是保障制造质量的核心支撑,其覆盖的检测项目需根据零件功能、行业规范及使用场景动态调整。通过综合运用传统检测手段与新兴技术,企业能够在提升产品可靠性的同时,降低生产成本并缩短交付周期,最终在市场竞争中占据优势地位。
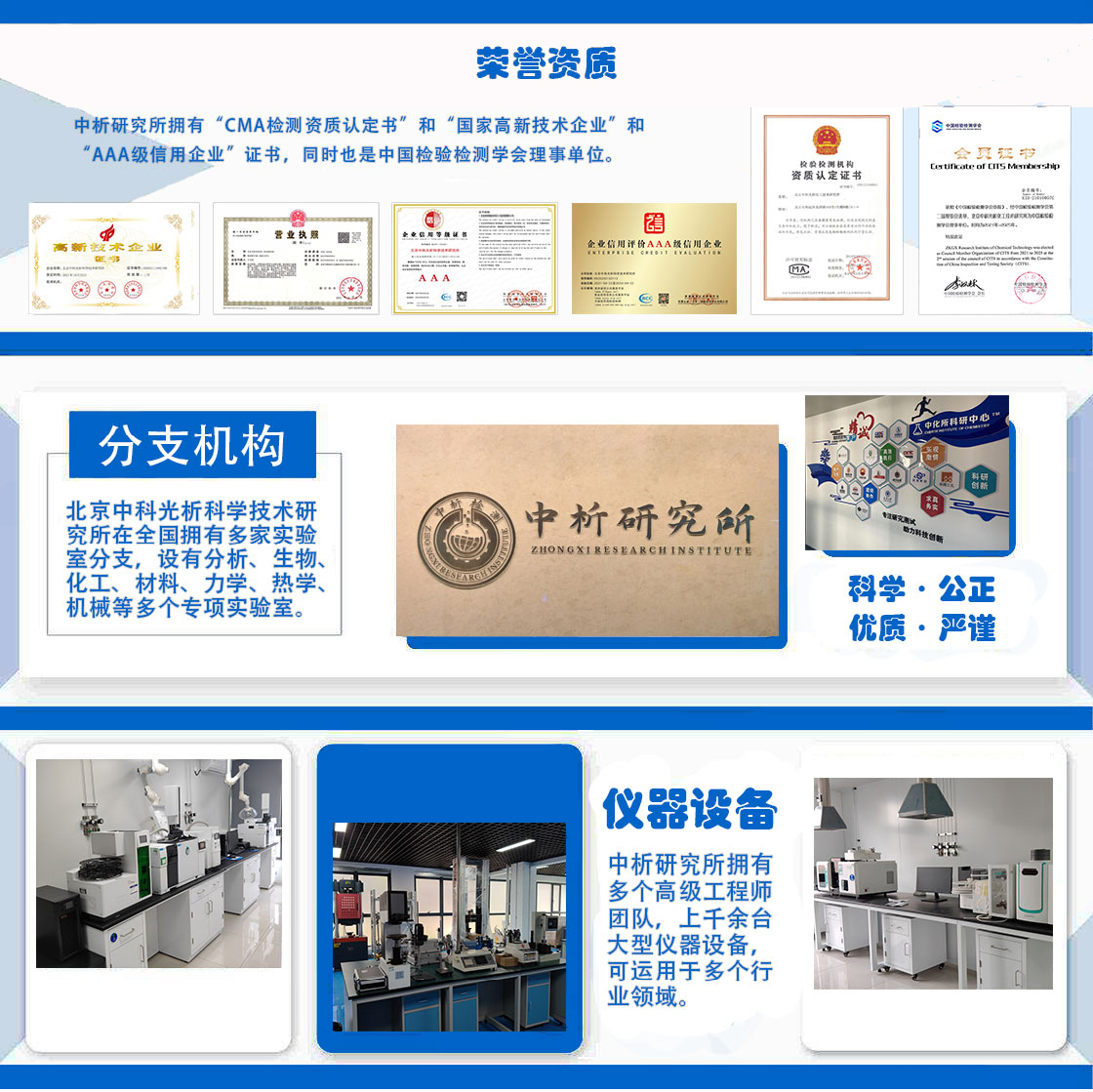
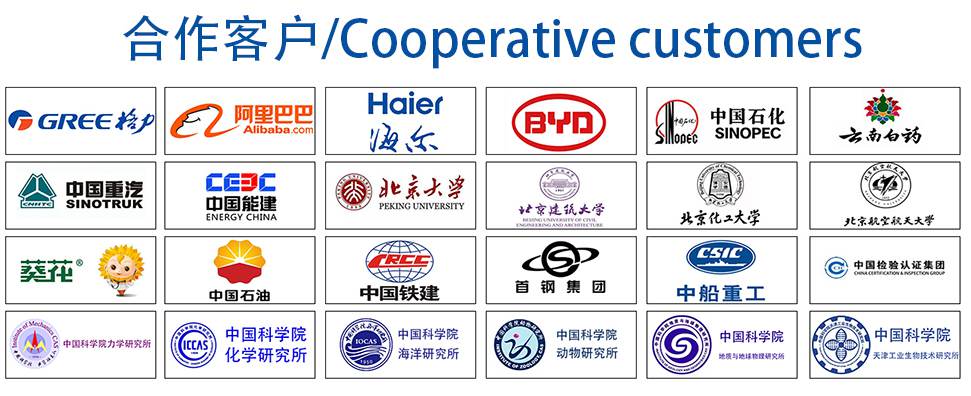