锌及锌合金化学成分检测的意义与要求
锌及锌合金作为重要的工业材料,广泛应用于建筑、汽车、电子、电池制造等领域。其性能直接受到化学成分的影响,例如机械强度、耐腐蚀性、可加工性等。因此,化学成分检测是确保材料质量、控制生产工艺的核心环节。根据相关行业标准(如GB/T 12689、ASTM B240、EN 1179等),锌及锌合金的检测需覆盖主成分、合金元素、杂质元素及有害元素的定量分析,以满足不同应用场景的特定需求。
核心检测项目及方法
锌及锌合金的化学成分检测通常包含以下关键项目:
1. 主成分锌(Zn)含量测定
锌作为基体元素,其纯度直接影响材料性能。采用电感耦合等离子体发射光谱法(ICP-OES)或原子吸收光谱法(AAS)进行高精度检测,检测范围覆盖99.9%~99.995%的高纯锌至含少量合金元素的锌基材料。
2. 合金元素分析
根据合金类型不同,需检测铝(Al)、铜(Cu)、镁(Mg)、铅(Pb)、镉(Cd)等元素的含量:
- 铝(0.5%~4.5%):影响强度和耐蚀性,常用X射线荧光光谱法(XRF)分析;
- 铜(≤1.5%):提升硬度,多用滴定法或ICP-OES检测;
- 铅与镉(≤0.005%):需控制有害元素,采用石墨炉原子吸收法(GF-AAS)。
3. 杂质元素检测
铁(Fe)、锡(Sn)、硅(Si)等微量杂质会降低材料延展性,通过火花直读光谱法(OES)或辉光放电质谱法(GD-MS)实现ppm级检测。
4. 有害元素限量检测
针对环保法规(如RoHS、REACH),需对汞(Hg)、砷(As)、六价铬(Cr⁶⁺)等有毒物质进行痕量分析,检测限可达0.0001%。
检测流程与质量控制
典型检测流程包括样品制备(切割、研磨、酸溶解)、仪器校准、多方法比对验证及数据偏差分析。实验室需通过 /CMA认证,定期使用标准物质(如NIST SRM 872)进行能力验证,确保检测结果的准确性与国际互认性。
行业应用与标准差异
不同领域对锌合金成分要求存在显著差异:电池用锌要求铅含量<0.002%,而铸造锌合金允许含铝至4.3%。检测报告需明确标注执行标准及允许偏差范围,例如压铸锌合金(Zamak系列)需符合ASTM B86的铜、镁配比要求。
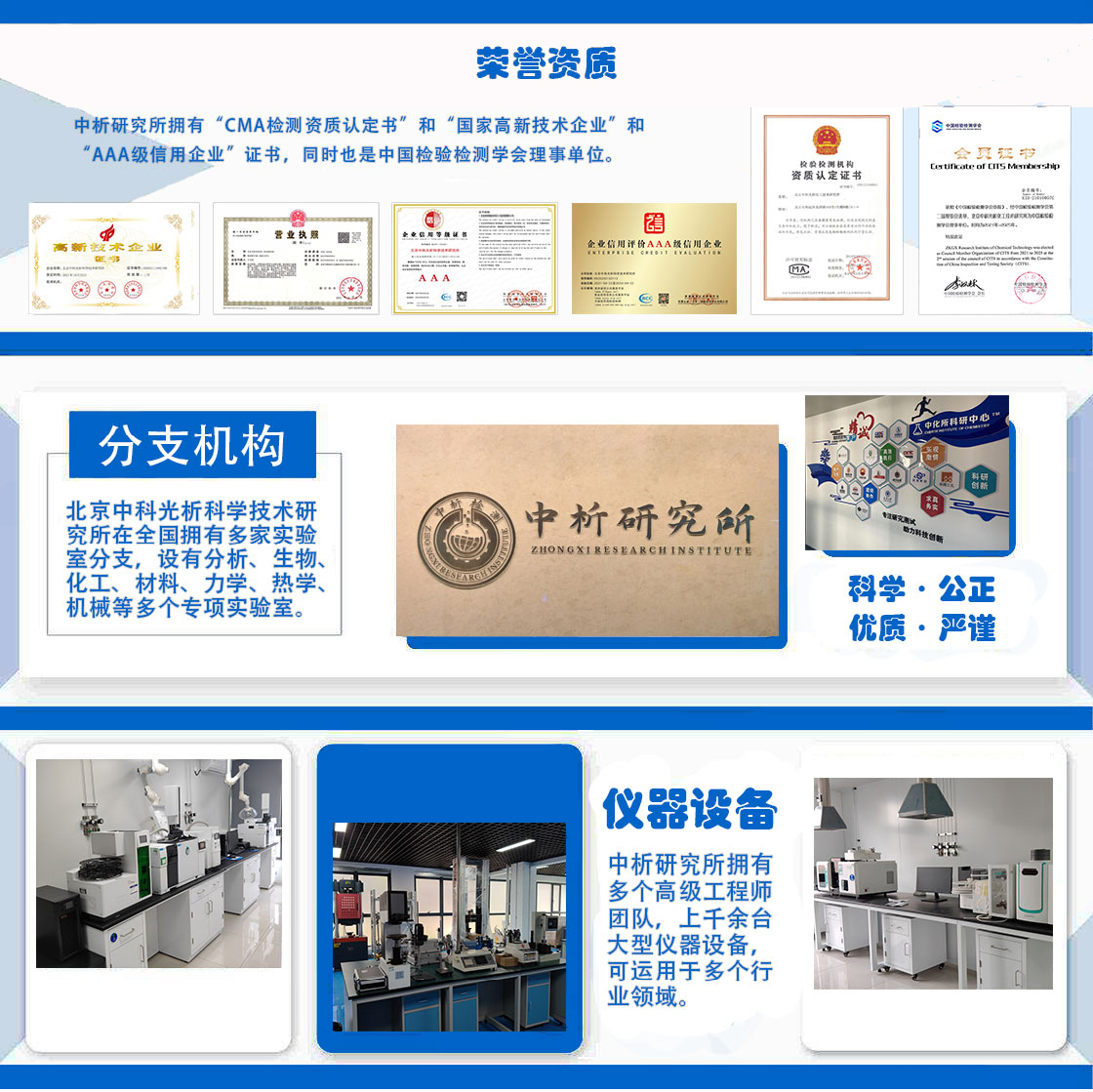
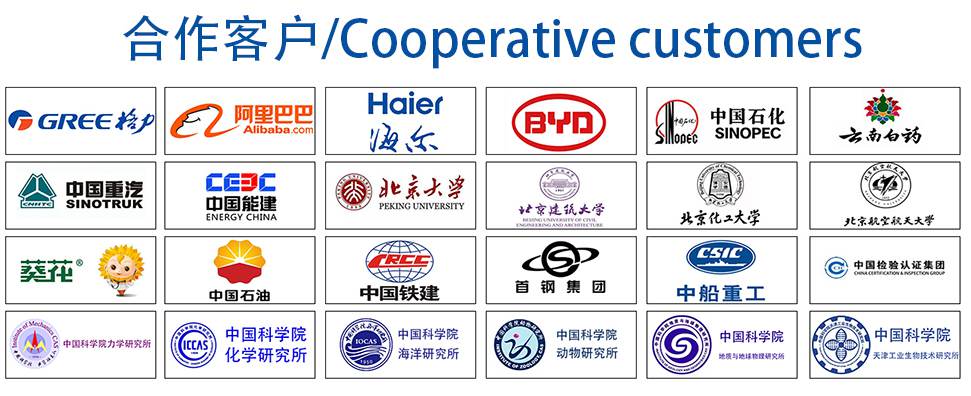