制冷装置用压力容器检测的重要性
制冷装置用压力容器作为制冷系统的核心承压部件,其安全性直接关系到设备运行效率和人员生命财产安全。由于长期承受周期性温度变化、介质腐蚀及交变载荷作用,容器易出现材料疲劳、焊缝裂纹或局部腐蚀等隐患。依据《固定式压力容器安全技术监察规程》(TSG 21)和GB 150《压力容器》标准要求,定期开展系统性检测是预防泄漏、爆炸事故的关键手段。检测过程需覆盖设计、制造、使用全生命周期,尤其对于低温工况下的容器,需重点关注材料的低温脆性转变特性。
主要检测项目及实施要点
1. 材料与结构完整性检测
通过光谱分析验证壳体材质与设计文件的一致性,使用超声波测厚仪测量壁厚减薄量(允许误差≤10%)。对封头过渡区、接管角焊缝等应力集中部位进行磁粉检测(MT)或渗透检测(PT),发现表面裂纹需立即评定处理。
2. 焊缝质量评估
采用X射线检测(RT)或超声相控阵技术(PAUT)对纵环焊缝进行内部缺陷筛查,气孔、夹渣等缺陷应符合NB/T 47013标准验收等级。对返修焊缝需进行200%扩探复查。
3. 耐压试验验证
按照1.25倍设计压力进行水压试验,保压时间不少于30分钟,观察有无异常变形或渗漏。氨系统容器需额外进行气密性试验,采用氦质谱检漏仪检测微量泄漏(泄漏率≤1×10⁻⁶ Pa·m³/s)。
4. 安全附件校验
压力表精度等级应达1.6级且每半年校验一次,安全阀起跳压力偏差不超过设定值±3%。爆破片装置需核对标定爆破压力与系统最大工作压力的匹配性。
5. 腐蚀与防护检测
对蒸发器、冷凝器等接触冷媒的部件,使用内窥镜检查晶间腐蚀情况。涂层附着力采用划格法测试(达到ISO 2409标准1级),牺牲阳极保护系统需测量保护电位(-0.85~-1.05V vs.CSE)。
检测周期与风险管控
首次全面检验应在投用后3年内进行,后续检验周期根据安全状况等级确定(最长不超过9年)。对R717(氨)系统容器、存在CL-离子腐蚀的沿海设备,应缩短20%检验周期。建立基于风险检验(RBI)的评估体系,运用声发射在线监测技术实现动态预警,确保制冷压力容器全生命周期安全可控。
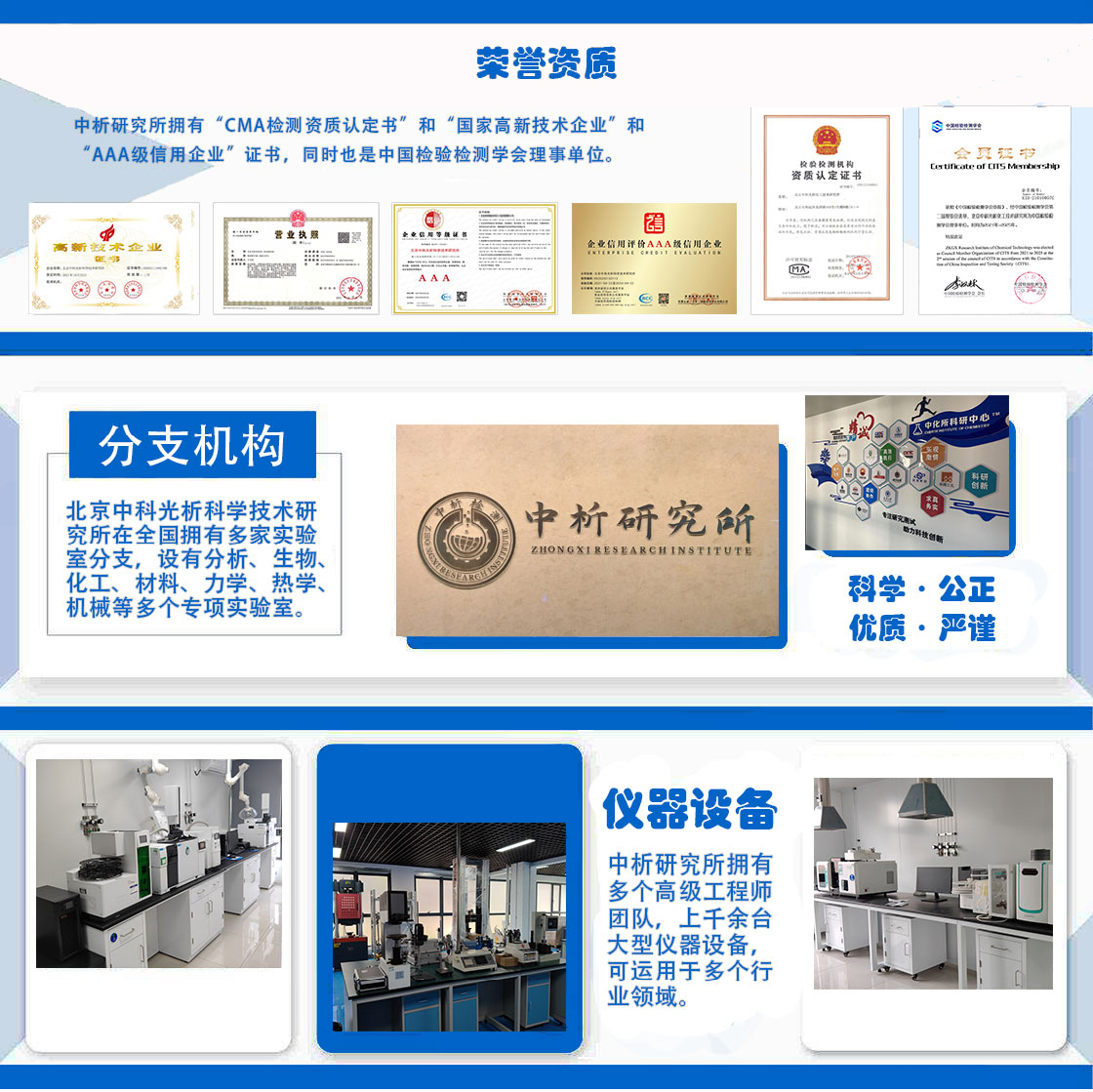
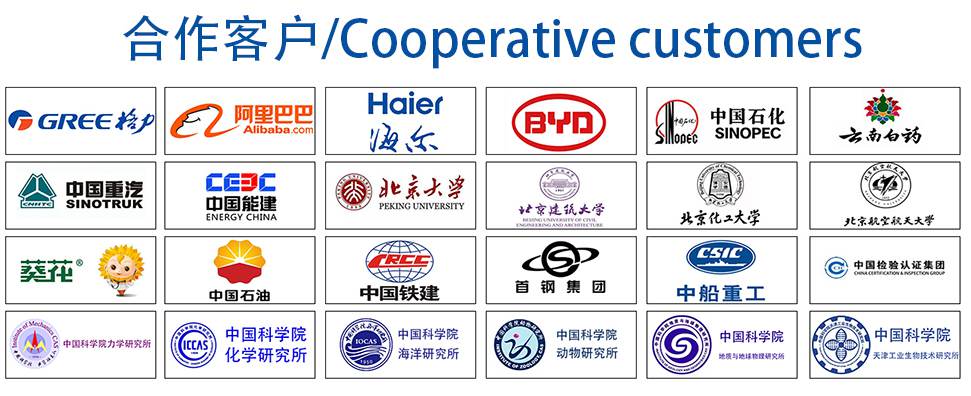