石油专用管材检测
实验室拥有众多大型仪器及各类分析检测设备,研究所长期与各大企业、高校和科研院所保持合作伙伴关系,始终以科学研究为首任,以客户为中心,不断提高自身综合检测能力和水平,致力于成为全国科学材料研发领域服务平台。
立即咨询石油专用管材检测的重要性与核心内容
在石油工业中,专用管材(如套管、油管、钻杆等)是保障油气开采、运输安全的核心部件。由于石油作业环境具有高温高压、腐蚀性强、地质条件复杂等特点,管材的失效可能导致严重的安全事故和经济损失。因此,石油专用管材检测是确保设备可靠性、延长使用寿命的关键环节。检测覆盖原材料验收、生产过程监控及服役周期评估,需依据API SPEC 5CT、ISO 11960、GB/T 33966-2017等标准体系,通过多维度技术手段对管材进行全面质量评估。
核心检测项目及技术要求
1. 材料化学成分与机械性能检测
通过光谱分析仪检测碳、锰、铬、钼等元素含量,确保符合J55、N80、P110等钢级要求。机械性能测试包括拉伸试验(屈服强度≥552 MPa)、硬度检测(HRC 22-35)、冲击韧性试验(-20℃下≥40 J),以验证管材的抗变形和抗断裂能力。
2. 几何尺寸与形位公差检测
使用激光测径仪、三坐标测量仪对管体外径(公差±0.79 mm)、壁厚(偏差≤±12.5%)、椭圆度(≤1%)进行精准测量。螺纹参数检测涵盖锥度(0.0625 in/ft)、螺距(8牙/英寸)、齿高(0.216 mm)等关键指标,确保API螺纹的密封性和连接强度。
3. 无损探伤与腐蚀评价
采用超声波探伤(UT)检测内部裂纹,磁粉检测(MT)发现表面缺陷,渗透检测(PT)识别微米级开口缺陷。腐蚀试验包含H2S应力腐蚀试验(NACE TM0177标准)、盐雾试验(500小时无红锈),评估管材在酸性环境下的耐蚀性能。
4. 密封性能与耐压测试
通过水压试验验证管体承压能力(如P110钢级需承受103 MPa压力),气密封检测使用氦质谱仪检测泄漏率(≤1×10⁻⁶ Pa·m³/s)。螺纹连接需通过上卸扣试验(3次循环无粘扣)和复合载荷试验(轴向拉力+内压)考核密封可靠性。
5. 涂层与表面处理检测
对防腐涂层进行附着力测试(划格法≥4B级)、厚度测量(环氧涂层250-400 μm)、耐阴极剥离试验(48小时剥离半径≤8 mm)。内衬双金属管需检测冶金结合强度(≥140 MPa),避免层间剥离风险。
检测技术发展趋势
随着智能检测技术的应用,数字射线成像(DR)、相控阵超声波(PAUT)、在线自动检测系统(如管端自动分选设备)逐步普及。同时,基于大数据分析的剩余寿命预测、微区腐蚀电化学监测等新技术,正在推动石油管材检测向智能化、精准化方向发展。
石油专用管材检测贯穿产品全生命周期,通过系统化的检测流程和齐全的技术手段,可有效预防因材料缺陷或性能退化引发的失效事故,为油气田安全高效开发提供技术保障。
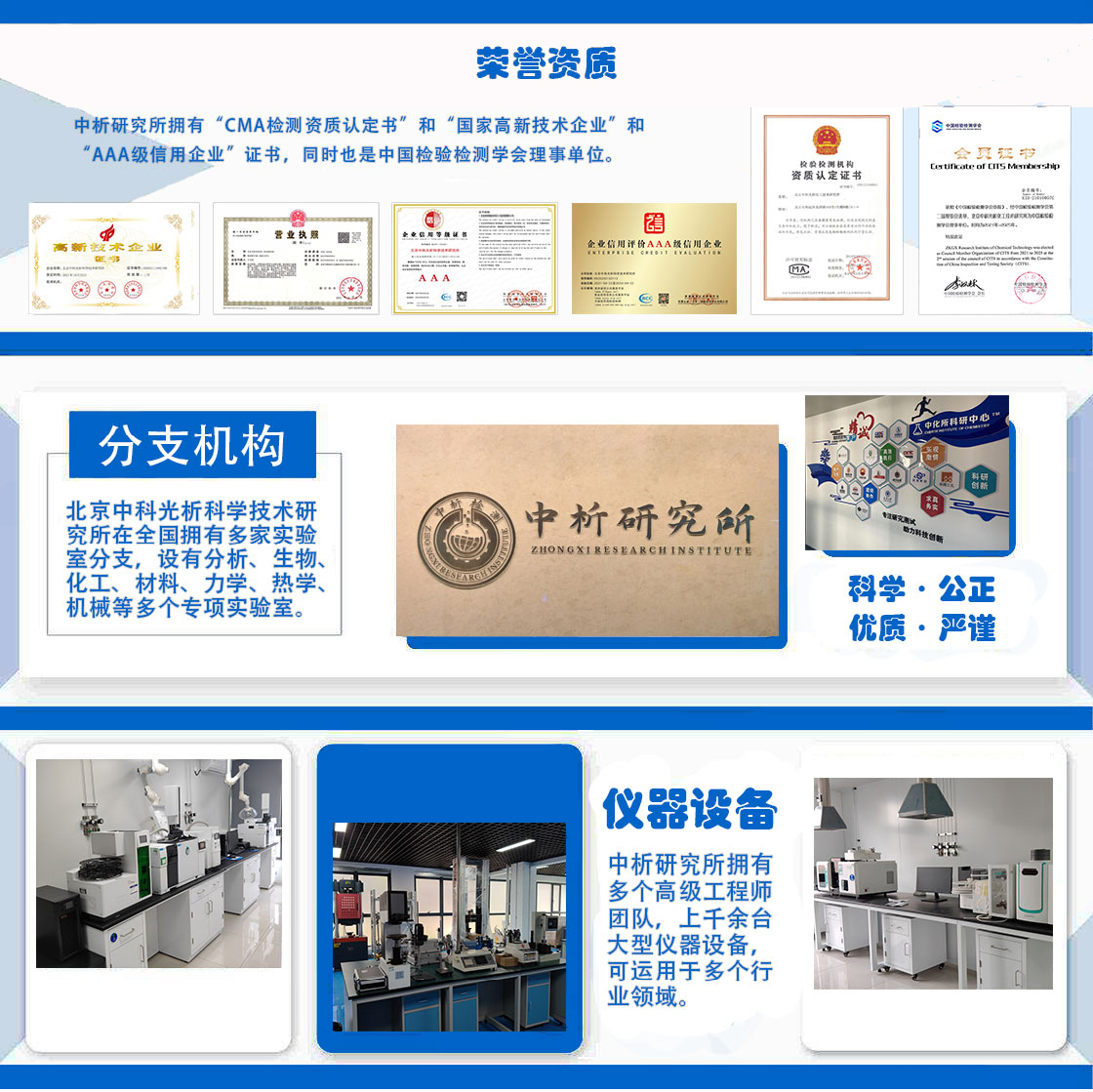
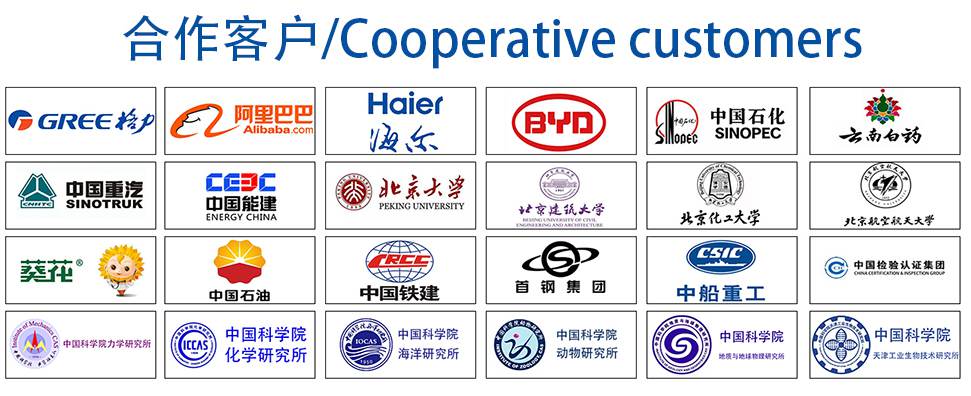