隔热油管检测的重要性及核心内容
隔热油管作为油气田开采中高温高压环境下的关键设备,主要用于油井注汽或输油过程中减少热量散失,提升热能利用效率。其性能直接影响采油效率、作业安全及设备寿命。由于长期处于腐蚀性介质、高温及机械应力环境中,隔热油管易出现结构损伤、隔热层失效、连接部位泄漏等问题。因此,定期开展系统性检测是确保其安全运行、延长使用寿命的核心手段。检测需覆盖外观、材料性能、密封性、隔热效率等多个维度,并依据行业标准(如API、SY/T等)进行规范性评估。
隔热油管检测的核心项目
1. 外观与尺寸检测
通过目视检查与精密测量工具,评估油管表面是否存在裂纹、腐蚀坑、变形等缺陷,同时检测管体直径、壁厚、长度等尺寸是否符合设计要求。重点检查螺纹连接部位的磨损情况,确保装配精度。
2. 隔热性能测试
采用热阻测试仪或稳态热流法,测量隔热层的导热系数和整体热损失率。通过模拟实际工况的高温实验,验证油管在目标温度下的隔热效率是否达标(通常要求导热系数≤0.05 W/m·K)。
3. 材质与力学性能分析
利用光谱分析、金相显微镜等技术检测管材化学成分及微观组织,评估抗腐蚀能力;通过拉伸试验、硬度测试等验证材料的屈服强度、延伸率等力学性能,确保其耐压及抗变形能力。
4. 密封性与耐压试验
对油管连接端进行气密性检测(如氦气检漏),并施加1.5倍工作压力的水压试验,持续保压5分钟以上,观察是否出现渗漏或异常变形,验证其在极端工况下的可靠性。
5. 防腐层与涂层检测
使用电火花检漏仪检测防腐涂层完整性,测量涂层厚度(如环氧树脂层≥300μm);通过附着力试验、耐化学试剂浸泡实验评估涂层的耐久性,防止介质腐蚀导致管体破损。
6. 综合性能模拟试验
在实验室模拟井下高温(≤350℃)、高压(≤25MPa)及交变载荷环境,连续运行72小时以上,监测隔热油管的整体性能衰减情况,为实际应用提供数据支撑。
结语
通过系统化的检测项目组合,可全面评估隔热油管的服役状态,及时发现潜在失效风险。建议结合智能化检测技术(如红外热成像、超声波探伤)建立数据化档案,实现预测性维护,最大限度降低非计划性停机损失,保障油气田高效安全生产。
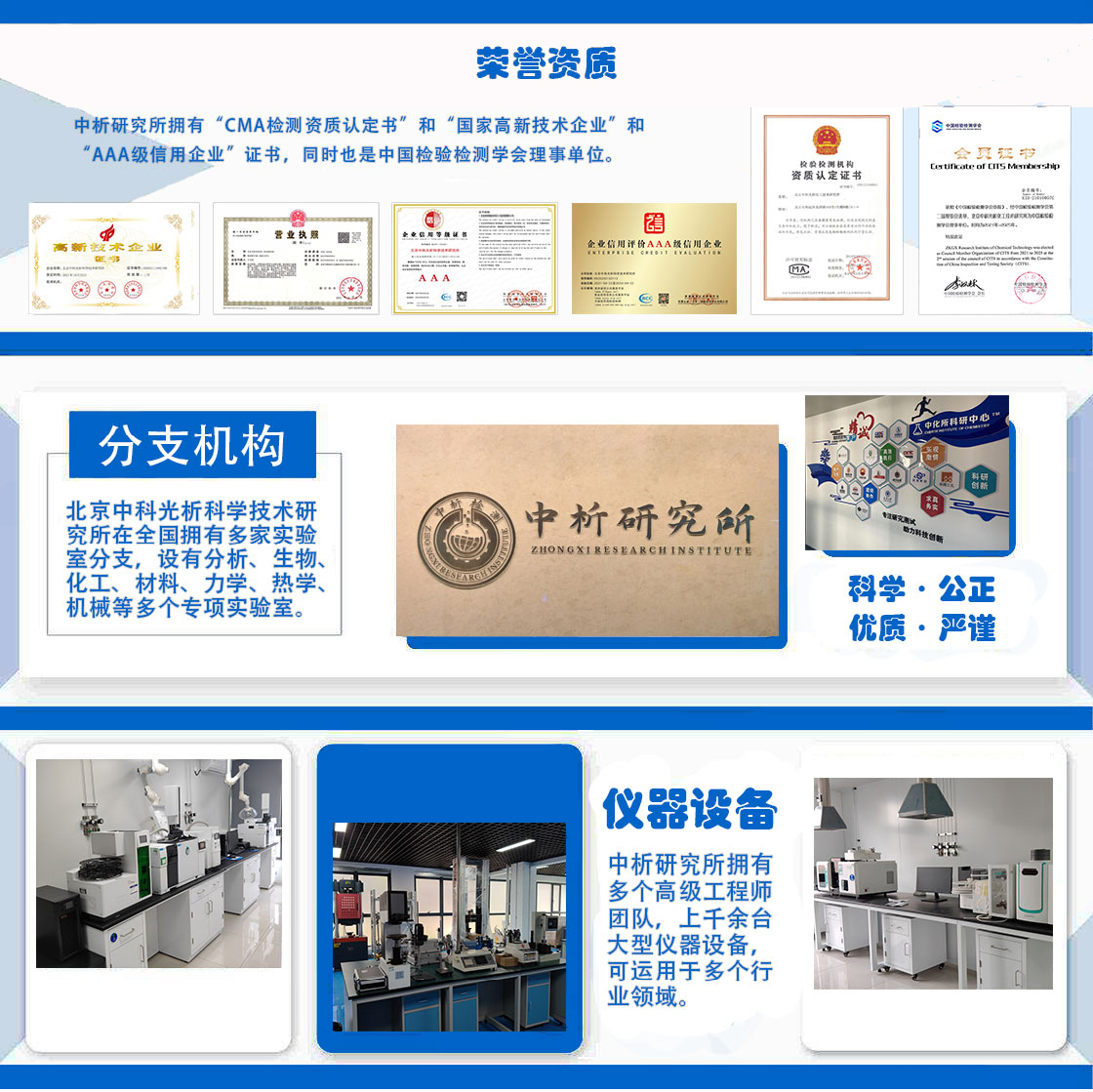
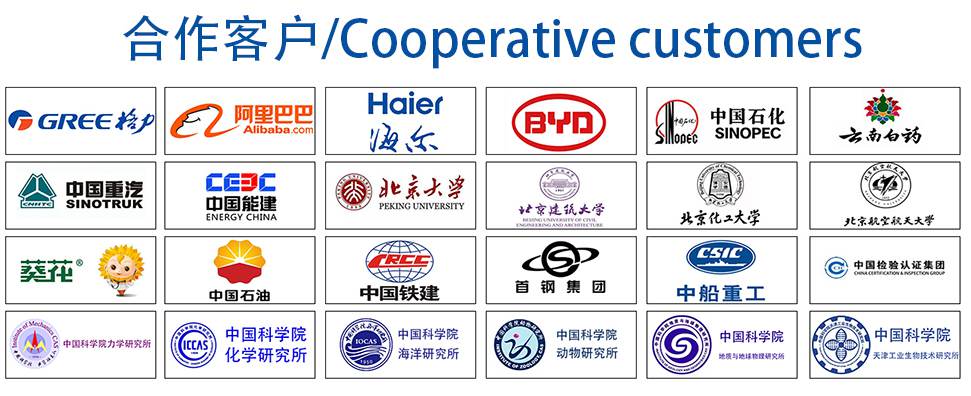