直缝电焊管检测的重要性及主要项目
直缝电焊管作为广泛应用于石油、天然气、建筑、机械制造等领域的重要管材,其质量直接关系到工程安全和使用寿命。由于其生产工艺的特殊性(通过高频电流焊接钢板或钢带形成纵向焊缝),焊缝区域的性能及整体管材的均匀性成为关键质量指标。因此,直缝电焊管的检测需涵盖几何尺寸、力学性能、焊缝质量、化学成分等多个维度,以确保其符合国家标准(如GB/T 3091、GB/T 13793)或行业规范(如API 5L)。以下将详细介绍直缝电焊管的核心检测项目。
1. 几何尺寸检测
几何尺寸检测是直缝电焊管的基础检测项目,包括外径、壁厚、长度、椭圆度及焊缝余高的测量。使用卡尺、千分尺、测厚仪等工具,重点检查管材的均匀性是否符合公差要求,尤其是焊缝区域的壁厚是否因焊接工艺波动而产生偏差。椭圆度过大会影响管道连接的密封性,而焊缝余高超标则可能导致应力集中。
2. 焊缝质量检测
焊缝是直缝电焊管的薄弱环节,需通过目视检查、超声波探伤(UT)、X射线探伤(RT)或磁粉探伤(MT)进行全面评估。检测内容包括气孔、裂纹、未熔合、夹渣等缺陷。其中,超声波探伤对内部缺陷敏感,X射线探伤可直观显示缺陷形态,而磁粉探伤适用于表面及近表面裂纹的排查。
3. 力学性能测试
力学性能测试包括拉伸试验、弯曲试验和压扁试验。拉伸试验用于测定抗拉强度、屈服强度和延伸率;弯曲试验通过将管材弯曲至规定角度,检验焊缝与母材的结合强度;压扁试验则模拟管材受径向压力时的变形能力,确保其在实际应用中不发生脆性断裂。
4. 化学成分分析
通过光谱分析仪或化学滴定法,检测管材的碳(C)、锰(Mn)、硅(Si)、硫(S)、磷(P)等元素含量。化学成分直接影响焊接性能和耐腐蚀性,例如硫、磷含量过高会导致焊缝热裂纹,而碳当量(Ceq)过高则可能引起焊接冷裂风险。
5. 表面质量与涂层检测
表面需检查是否存在划痕、锈蚀、结疤等缺陷。对于防腐涂层管材(如镀锌管、环氧涂层管),需测量涂层厚度(磁性测厚仪)、附着力(划格试验)及耐盐雾性能,以确保长期使用中防腐效果达标。
6. 水压试验与气密性试验
水压试验通过向管材内部施加1.5-2倍工作压力的静水压,保压时间不少于5秒,检查是否存在渗漏或永久变形。气密性试验则用于燃气等高压输送场景,通过充入压缩空气并监测压力变化,验证管道的密封性能。
结语
直缝电焊管的检测需贯穿原材料入库、生产过程及成品出厂全环节,结合离线检测与在线监测技术(如自动化探伤系统)。只有严格把控各项指标,才能确保管材在复杂工况下的可靠性和安全性,为工程质量和环境保护提供基础保障。
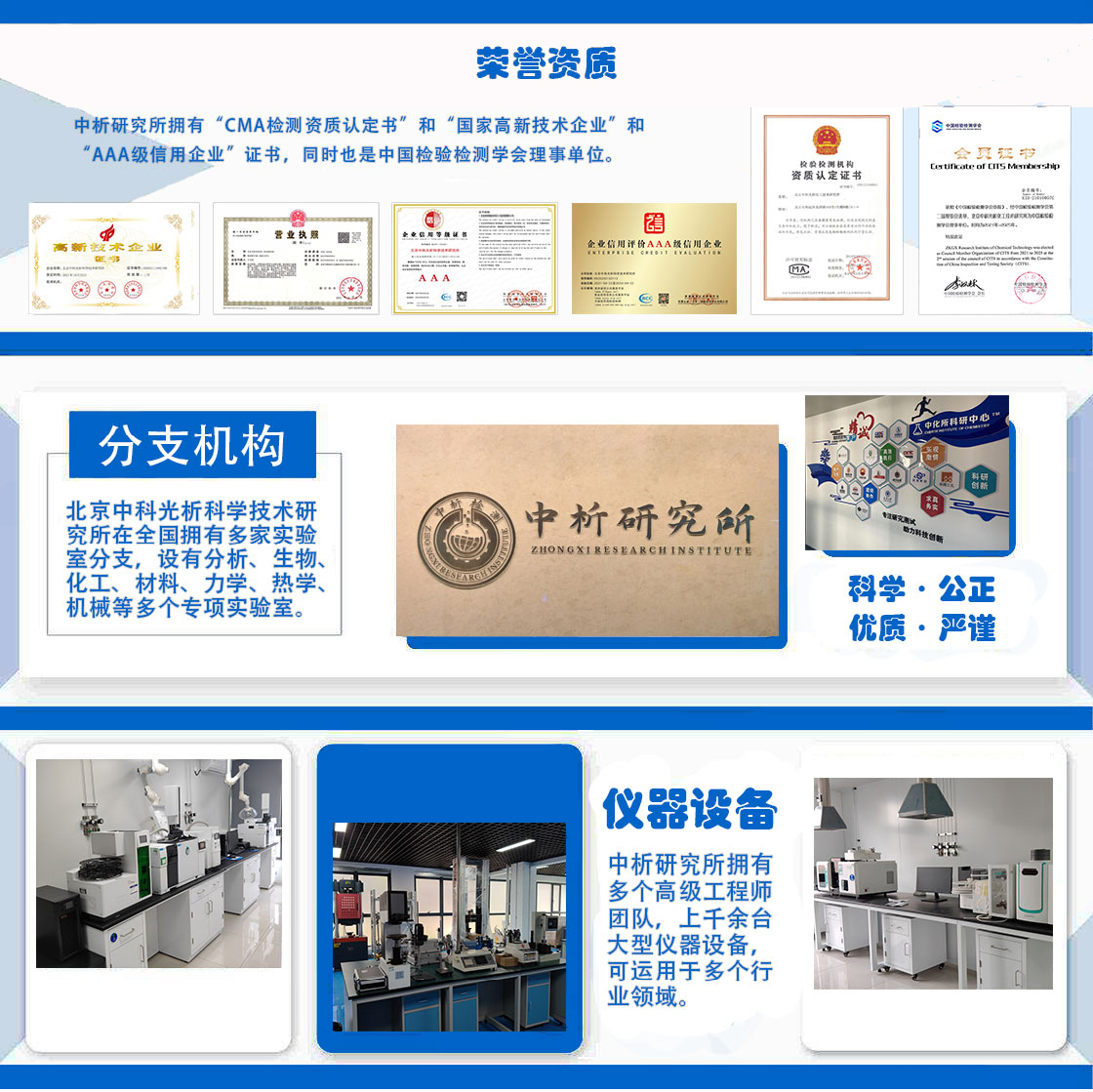
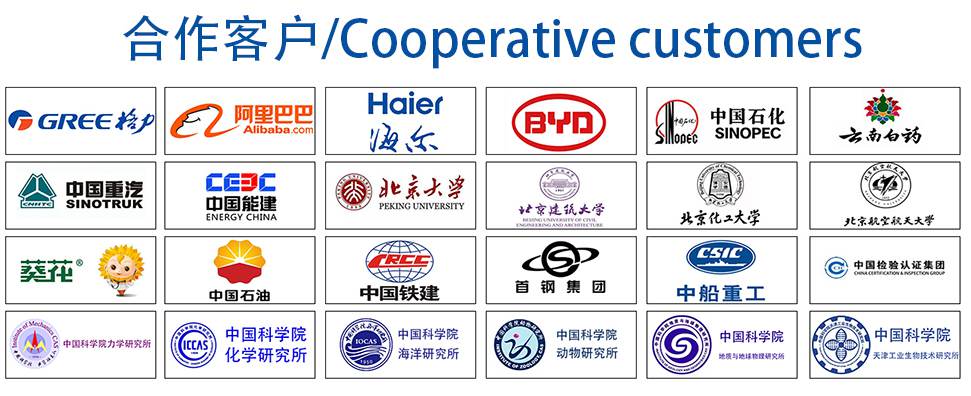