管线钢管检测的重要性与应用领域
管线钢管作为石油、天然气、化工等行业输送介质的关键载体,其质量直接关系到能源运输的安全性、效率和环保性能。随着长距离、高压、高腐蚀性介质的输送需求增加,管线钢管的检测成为确保工程安全的重要环节。检测工作贯穿原材料采购、生产加工、安装施工及后期运维的全生命周期,旨在验证钢管的力学性能、耐腐蚀性、焊接质量等核心指标,预防因材料缺陷导致的泄漏、爆裂等安全事故。国际标准(如API、ISO)和国内标准(如GB/T 9711)均对管线钢管检测提出了严格要求,覆盖化学成分、几何尺寸、无损探伤等多个维度。
管线钢管核心检测项目及技术方法
1. 材质性能检测
化学成分分析:通过光谱仪或化学滴定法检测碳、锰、硅、硫、磷等元素的含量,确保符合材料等级要求(如X60、X80)。 力学性能测试:包括拉伸试验(测定屈服强度、抗拉强度、延伸率)、冲击试验(-20℃低温冲击韧性)、硬度测试(布氏/洛氏硬度)等。 金相分析:观察微观组织(如晶粒度、夹杂物分布),评估热处理工艺和材料均匀性。
2. 尺寸与形位公差检测
外径与壁厚测量:使用超声波测厚仪、激光扫描仪或卡尺,检查钢管外径、壁厚的偏差是否符合公差范围(如±0.5%)。 直线度与圆度检测:采用激光干涉仪或光学投影仪,评估钢管的弯曲度及截面形状的均匀性。
3. 表面质量与腐蚀检测
目视检查与磁粉探伤:发现表面裂纹、折叠、划痕等缺陷,尤其关注焊缝区域。 腐蚀速率评估:通过盐雾试验或电化学方法模拟服役环境,预测钢管耐蚀性能。
4. 无损检测(NDT)技术
超声波检测(UT):识别内部分层、夹杂、气孔等缺陷,精度可达毫米级。 射线检测(RT):利用X射线或γ射线成像技术检测焊缝内部质量。 涡流检测(ECT):适用于表面及近表面缺陷的快速筛查。
5. 压力与密封性测试
水压试验:按标准压力(如1.5倍设计压力)保压检查钢管抗压强度及泄漏情况。 气密性试验:采用氦气质谱检漏法检测微小漏点,灵敏度达10-9 mbar·L/s。
6. 特殊环境适应性检测
低温冲击试验:模拟极寒环境(如-45℃)验证材料脆性断裂风险。 氢致开裂(HIC)测试:评估钢管在含硫化氢介质中的抗氢损伤能力。
检测标准的动态发展与智能化趋势
随着数字孪生、AI图像识别等技术的应用,管线钢管检测逐步向自动化、智能化方向发展。例如,基于机器视觉的缺陷分类系统可实时分析超声检测信号,而物联网传感器可实现服役期钢管的健康状态监测。未来,检测数据将与全生命周期管理平台深度融合,为管线的安全运维提供科学依据。
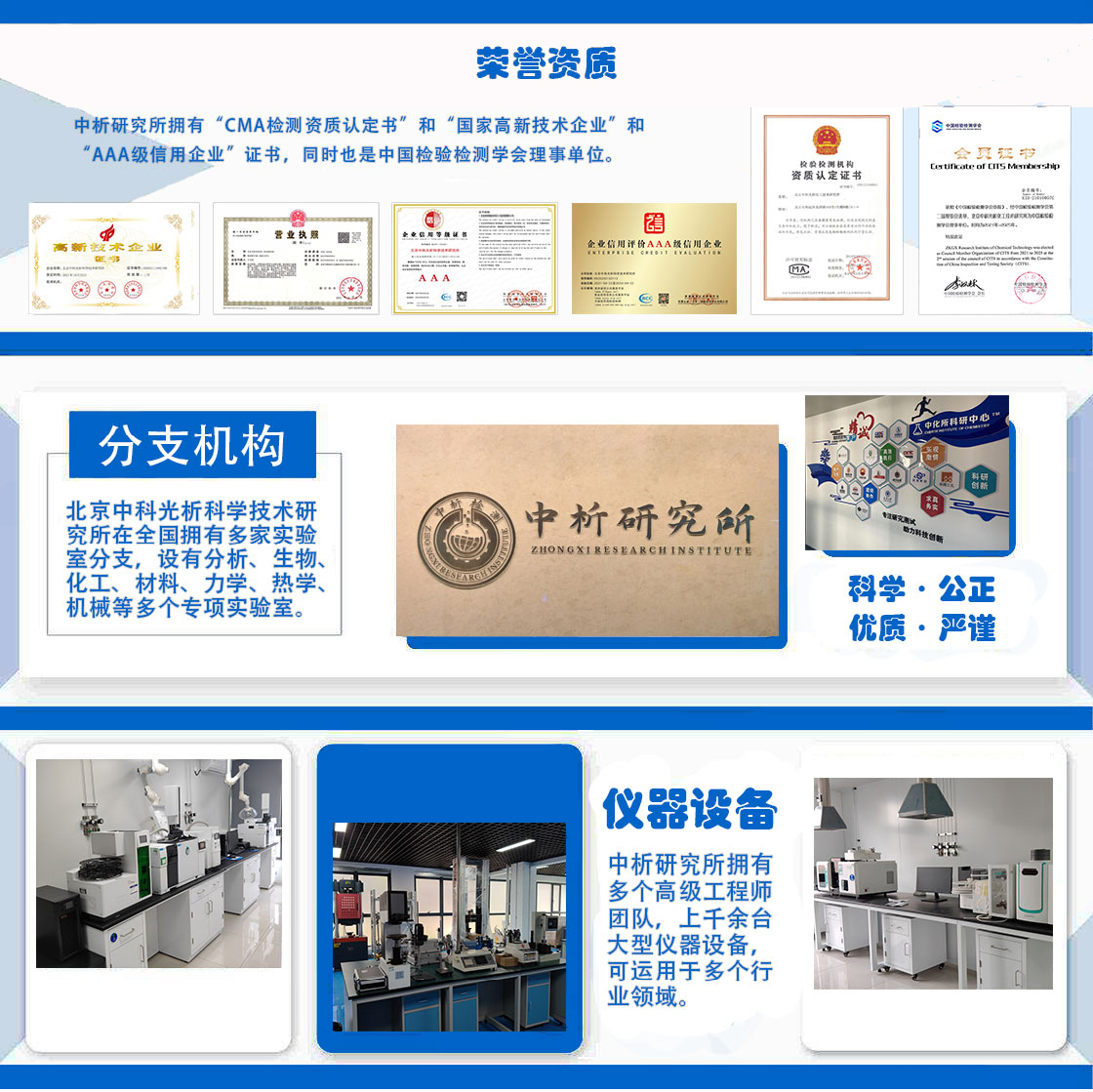
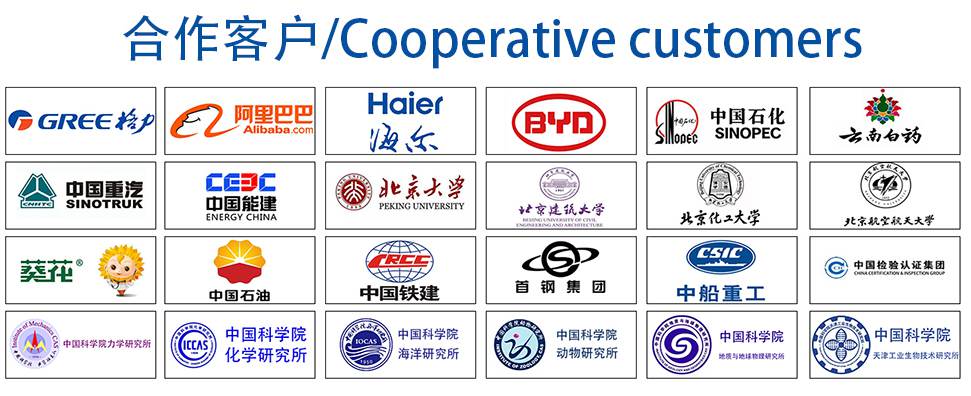