引水压力钢管与蜗壳检测的重要性
引水压力钢管和蜗壳作为水力发电站的核心输水结构,承担着输送高压水流、驱动水轮机组发电的关键作用。由于长期承受高水压、水流冲击及复杂环境腐蚀,其结构安全直接影响电站运行效率与人员安全。据统计,约15%的水电站事故与压力钢管或蜗壳的损伤相关。因此,定期开展系统性检测是确保设备可靠性、延长使用寿命、预防突发性故障的必要措施。检测工作需结合金属材料特性、流体力学特征及环境因素,通过多维度评估实现结构健康状态的精准诊断。
引水压力钢管检测项目
1. 焊缝质量检测:采用超声波探伤(UT)、磁粉检测(MT)等技术,重点检查环缝、纵缝及补强板的焊接质量,发现未焊透、夹渣或裂纹等缺陷。检测精度需达到GB/T 3323标准要求,裂纹检出灵敏度不低于0.5mm。
2. 腐蚀与壁厚监测:使用电磁超声测厚仪(EMAT)进行逐段壁厚测量,配合三维激光扫描建立腐蚀形貌模型。重点关注弯管段、支撑环部位的局部腐蚀,当壁厚减薄量超过设计值10%时需启动修复程序。
3. 应力应变分析:在水压试验过程中布设光纤光栅传感器(FBG),实时监测关键截面的环向应力与轴向应力分布,验证数值模拟结果的准确性。典型工况下实测应力不应超过材料屈服强度的60%。
蜗壳专项检测要点
1. 空蚀损伤评估:通过高速摄像记录水流空化现象,结合涡流检测(ECT)识别内壁蜂窝状空蚀区。对深度超过3mm的空蚀坑需进行堆焊修复,并采用着色渗透检测(PT)验证修复质量。
2. 疲劳裂纹检测:在蜗壳与座环连接处、导叶端部等应力集中区域,采用相控阵超声(PAUT)进行全聚焦模式扫描,配合断裂力学分析预测裂纹扩展速率。检测周期应每2年实施一次,雨季前后需增加频次。
3. 密封性能测试:在额定水头1.25倍压力下进行保压试验,使用红外热像仪监测法兰连接处的渗漏情况。要求30分钟压降不超过试验压力的0.5%,且无可见水滴渗出。
智能化检测技术应用
随着技术进步,爬壁机器人搭载TOFD检测系统已实现蜗壳内壁的自动化检测,检测效率提升40%以上。同时,基于机器学习的损伤预测系统可通过历史数据建立寿命模型,提前6个月预警高风险区域。2023年某抽水蓄能电站的实践表明,智能化检测使维护成本降低28%,非计划停机时间减少65%。
检测周期与标准规范
根据NB/T 35045-2014《水电站压力钢管安全检测技术规程》,常规检测应每5年开展一次,特殊工况(如地震、洪水后)需立即实施专项检测。检测报告须包含缺陷位置图、剩余寿命评估及维修建议,同时需符合ASME B31.1和IEC 62305的国际标准要求。
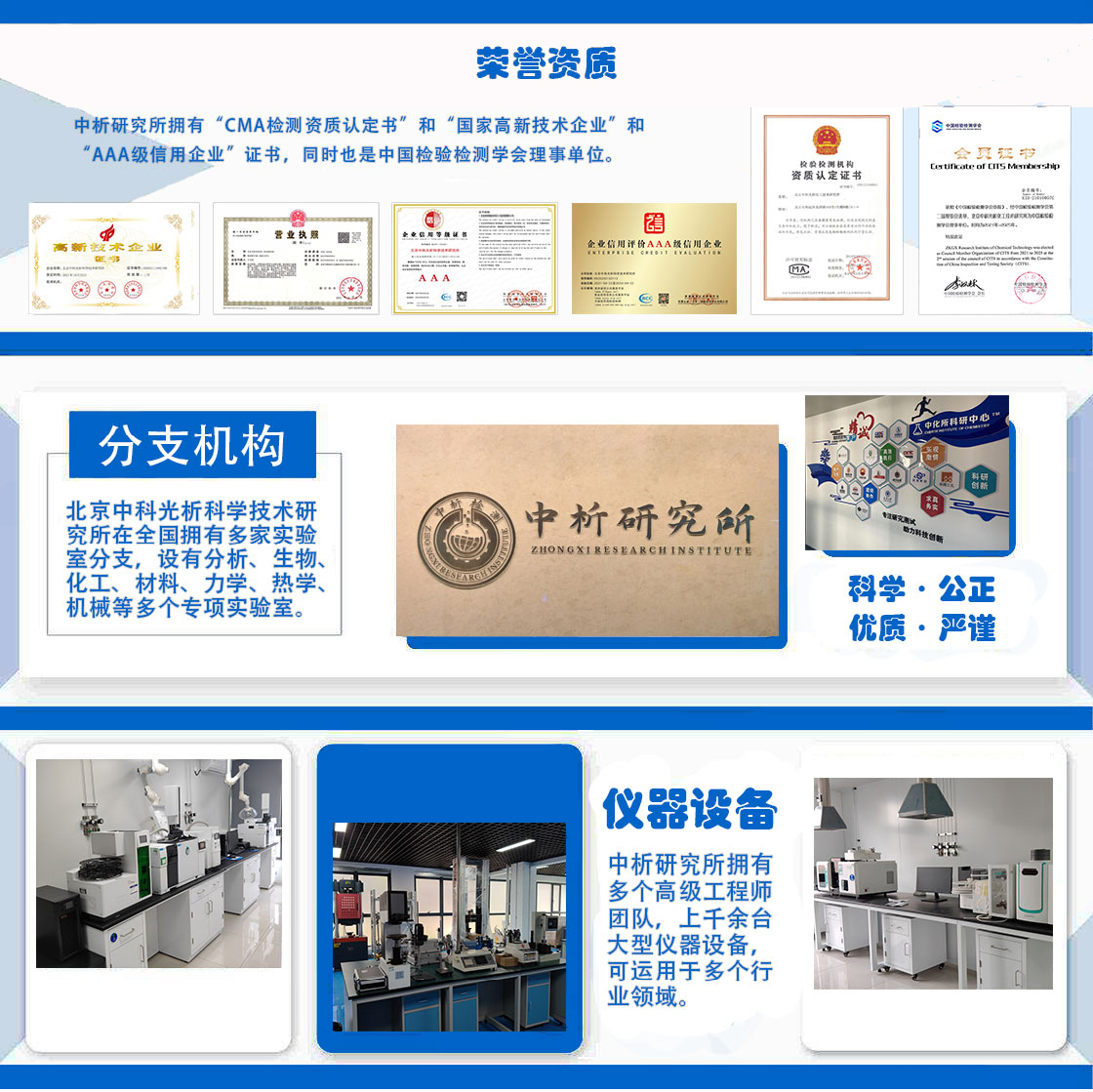
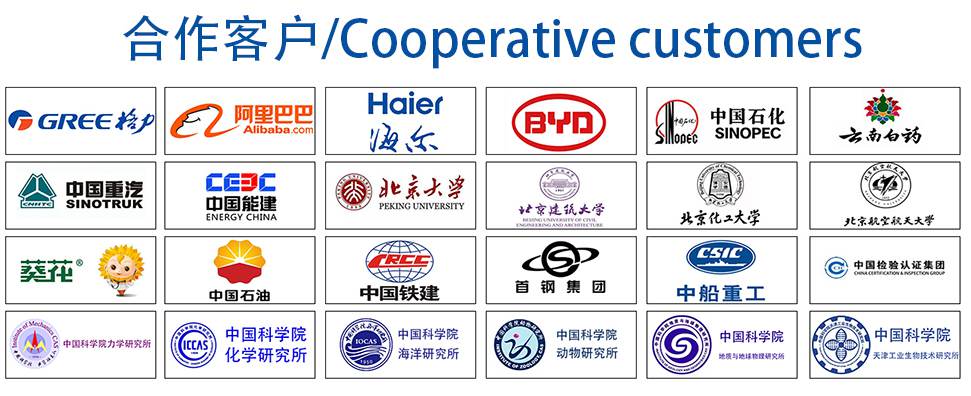