焊缝质量检测的重要性与检测体系
在工业生产中,焊接作为金属结构连接的核心工艺,其质量直接影响设备安全性、使用寿命和运行稳定性。焊缝质量检测通过科学的测试方法和严谨的评判标准,可有效发现裂纹、气孔、未熔合等缺陷,避免因焊接失效引发的重大事故。现代检测技术已形成包含目视检查、无损检测、力学测试等多维度的完整体系,贯穿于焊接前材料检验、焊接过程监控和焊后质量验收全周期。
常规焊缝质量检测项目分类
1. 目视检查(VT):
作为最基础的检测手段,技术人员通过放大镜、焊缝量规等工具对焊缝外观进行评定。重点检测表面裂纹、咬边、焊瘤、余高异常等缺陷,同时验证焊缝尺寸是否符合工艺规范要求。
2. 无损检测(NDT):
• 射线检测(RT):利用X/γ射线穿透工件成像,可精准识别内部气孔、夹渣等体积型缺陷
• 超声波检测(UT):通过高频声波反射信号定位内部缺陷,特别适用于厚板焊缝检测
• 磁粉检测(MT):对铁磁性材料表面及近表面裂纹具有高灵敏度,检测速度较快
• 渗透检测(PT):通过显像剂显现开口缺陷,适用于非多孔性材料表面检测
力学性能专项测试
3. 破坏性试验:
• 拉伸试验:测定焊缝金属抗拉强度和断后伸长率
• 弯曲试验:评估焊缝塑性变形能力和结合面质量
• 冲击试验:检测焊缝在低温环境下的抗脆断性能
• 硬度测试:监控热影响区硬度变化,预防冷裂纹产生
智能化检测技术发展
随着工业4.0技术推进,焊缝检测正朝着自动化、数字化方向升级。相控阵超声检测(PAUT)实现三维缺陷成像,TOFD技术可精确测定缺陷高度,红外热成像技术能实时监测焊接温度场变化。AI算法已开始应用于射线底片智能评片,检测效率提升60%以上。
检测标准与质量评定
检测过程需严格遵循ISO 5817、AWS D1.1、GB/T 3323等标准规范,根据缺陷类型、尺寸、密集度进行等级评定。对于承压设备、船舶、核电等特殊领域,还需执行行业特定的验收准则,确保检测结果的专业性和权威性。
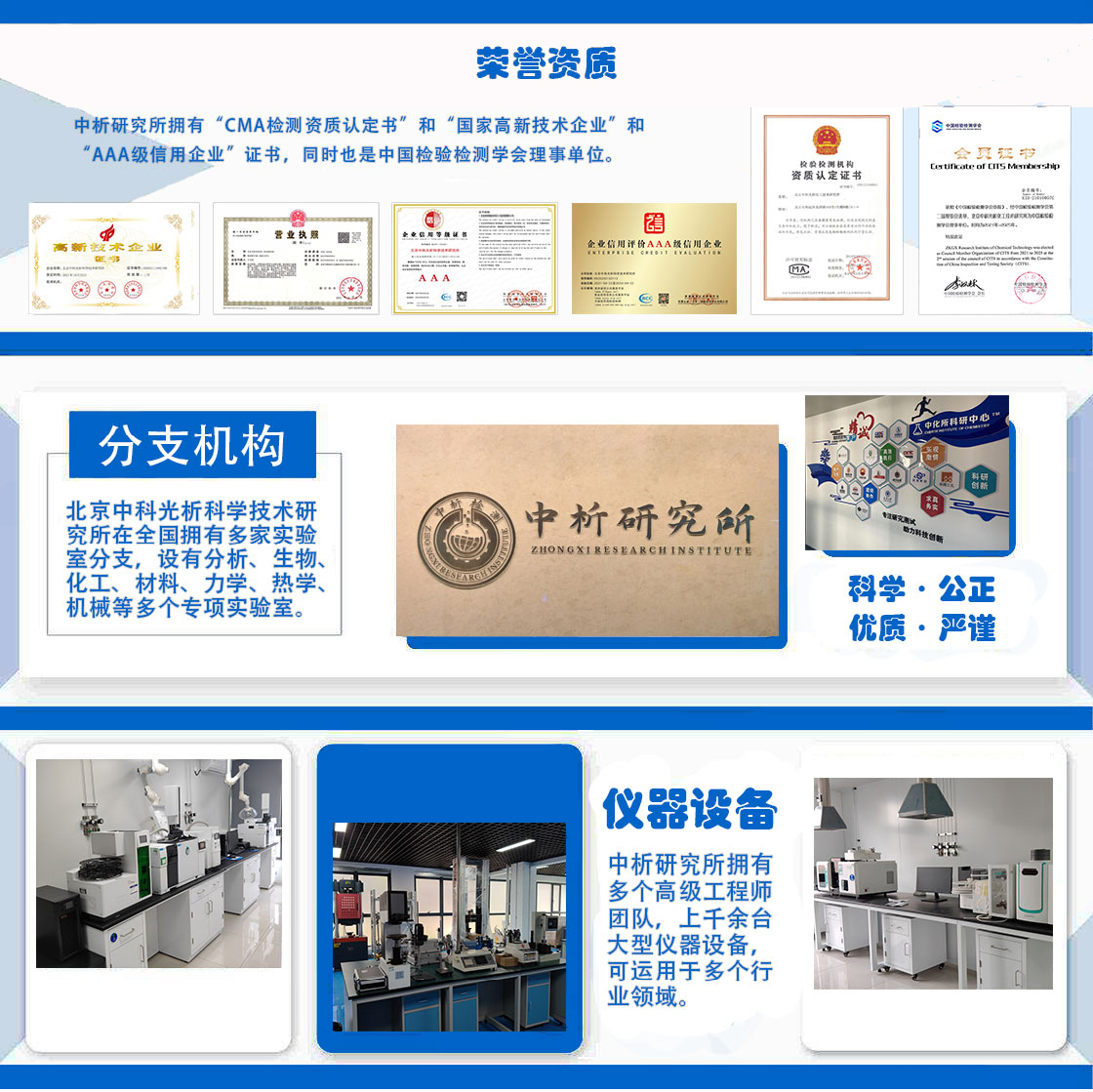
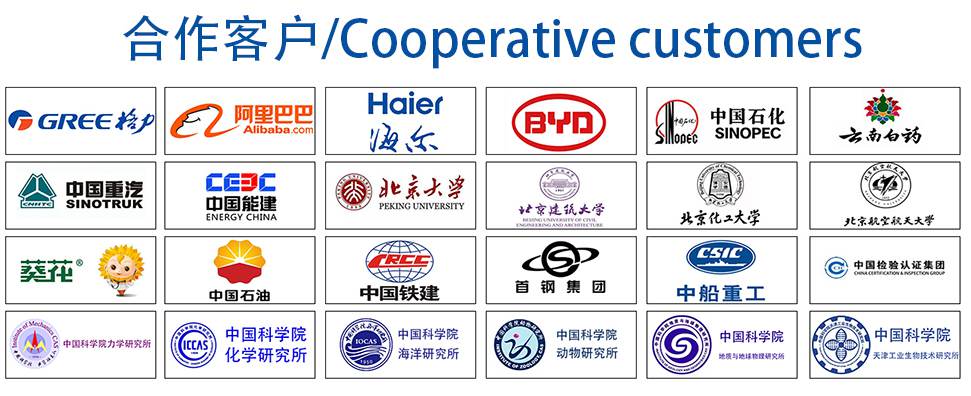