金属切削机床参数检测的重要性
金属切削机床作为现代制造业的核心设备,其性能直接关系到加工精度、效率和产品质量。机床参数的准确性与稳定性是保证加工过程可靠性的关键因素,因此对金属切削机床的各项参数进行系统性检测至关重要。通过科学的检测手段,可以验证机床是否符合设计标准、发现潜在故障隐患,并为设备维护和工艺优化提供数据支持。
检测项目分类与技术要求
金属切削机床的检测项目主要分为几何精度检测、运动精度检测、切削性能检测和动态特性检测四大类。检测需依据国家或国际标准(如GB/T、ISO等)进行,确保检测结果的规范性和可比性。以下为关键检测项目的具体内容:
1. 几何精度检测
通过激光干涉仪、电子水平仪和高精度测微仪等设备,检测机床导轨的直线度、平面度,主轴与工作台的垂直度/平行度等空间几何关系。典型参数包括:主轴径向跳动(≤0.005mm)、工作台平面度(≤0.01mm/m)、导轨直线度(≤0.015mm)。
2. 运动精度检测
采用球杆仪和激光跟踪仪评估机床各轴运动的定位精度与重复定位精度。检测项目包含:轴向定位误差(±0.005mm)、反向间隙(≤0.008mm)、插补圆度误差(≤0.02mm)。需在空载和负载状态下分别测试,验证动态补偿系统的有效性。
3. 切削性能检测
通过切削力测试系统监测主轴扭矩(±1%FS)和功率波动(≤5%),结合表面粗糙度仪(Ra≤1.6μm)分析加工表面质量。同时评估切削振动频谱特征,判断刀具-工件系统的稳定性,防止颤振现象发生。
4. 热变形与温升检测
使用红外热像仪监测机床关键部位温升梯度(≤15℃/h),配合位移传感器记录热变形量(≤0.03mm)。重点检测主轴轴承、滚珠丝杠和床身的温度场分布,验证热平衡设计是否合理。
5. 振动与噪声检测
基于加速度传感器和声级计,测量机床在空转和切削状态下的振动加速度(≤2.5m/s²)和声压级(≤85dB(A))。分析频谱特征可诊断轴承磨损、齿轮啮合异常等机械故障。
检测结果的应用价值
完整的参数检测数据不仅可用于设备验收和定期维护,还能为工艺参数优化提供科学依据。例如,通过分析切削力与振动的关系,可确定最佳切削用量;结合热变形数据能优化加工节拍,提高设备利用率。随着工业物联网技术的发展,在线检测与预测性维护正成为提升机床效能的新趋势。
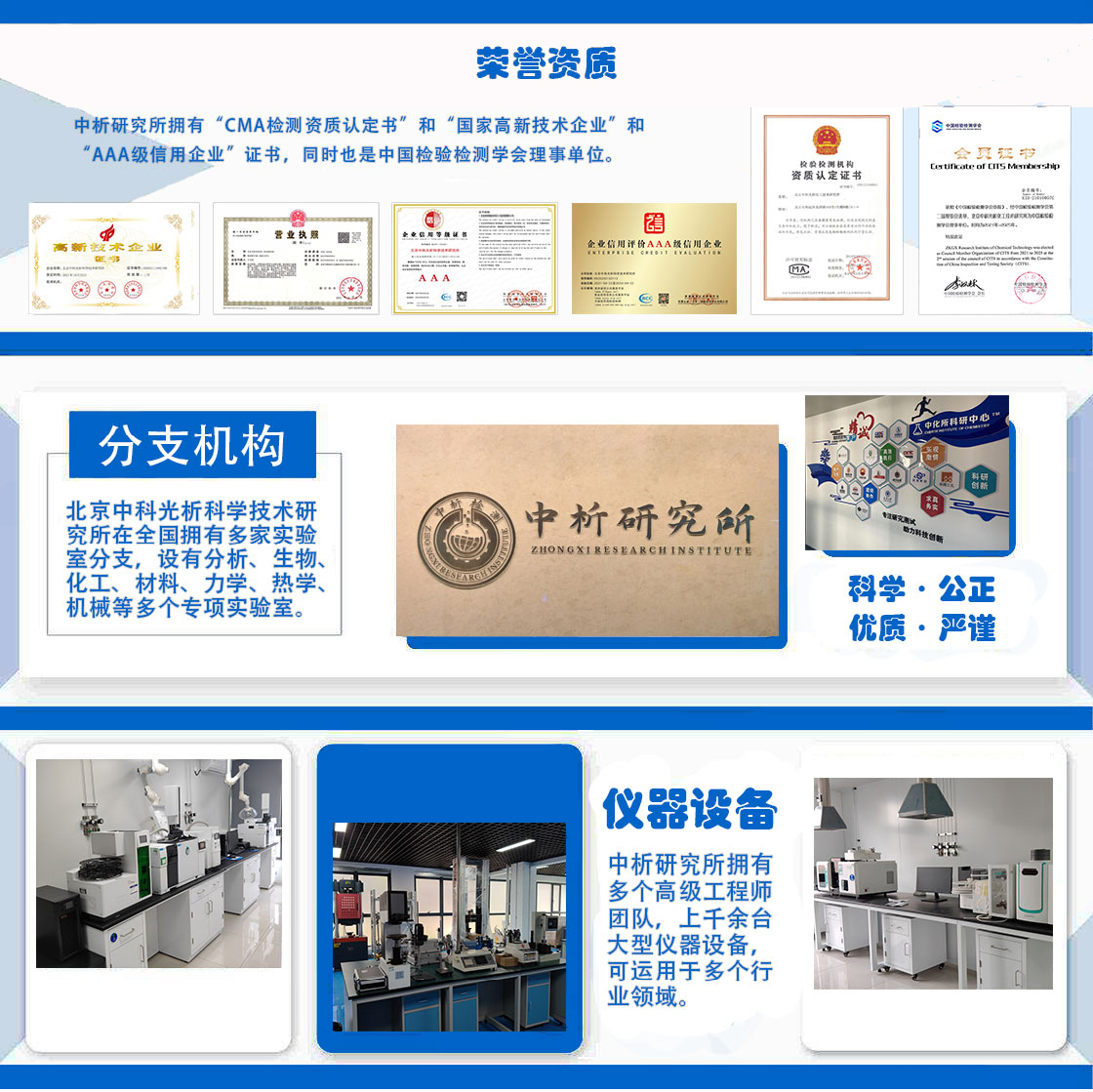
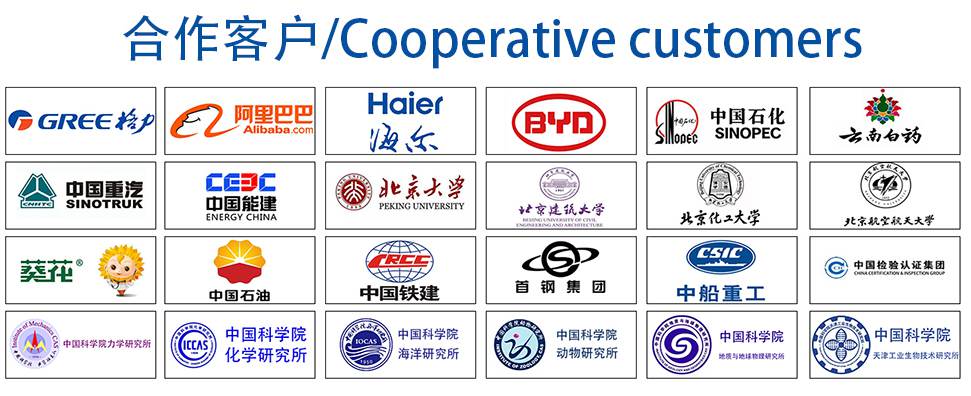