龙门导轨磨床检测的重要性与核心内容
龙门导轨磨床作为高精度加工设备的核心装备,广泛应用于机械制造、航空航天、模具加工等领域。其性能直接关系到工件的加工精度与表面质量,因此定期开展检测与校准是保障设备稳定运行的关键。通过系统化的检测项目,可及时发现导轨磨损、传动误差、几何精度偏差等问题,避免因设备故障导致的生产停滞或产品质量缺陷。此外,规范的检测还能延长设备使用寿命,降低维护成本,为企业实现高效生产提供技术支撑。
核心检测项目及方法
1. 几何精度检测
包括床身导轨的直线度、平行度、垂直度以及横梁的水平度检测。使用激光干涉仪、电子水平仪等高精度仪器,依据GB/T 17421.1标准对导轨面的平面度误差进行量化分析,确保导轨基础结构的稳定性。
2. 运动精度检测
通过动态检测磨头移动的直线性、重复定位精度及工作台运动的平稳性。采用球杆仪或激光跟踪仪,在X/Y/Z三轴方向进行轨迹扫描,检测反向间隙、定位误差等参数,误差值需控制在±0.005mm以内。
3. 传动系统检测
重点检验滚珠丝杠、齿轮齿条、伺服电机的配合状态。使用百分表测量传动系统的反向间隙,借助振动分析仪检测轴承、联轴器等部件的异常振动频率,确保传动效率与稳定性。
4. 润滑与液压系统检测
检查导轨润滑油膜厚度、油路通畅性及液压缸压力稳定性。通过油液颗粒度分析仪监测油液污染度,同时验证液压系统保压性能,防止因润滑不足导致的导轨异常磨损。
5. 电气与控制系统检测
测试数控系统、编码器、限位开关的响应精度与同步性。利用PLC诊断工具验证程序逻辑,并检测伺服驱动器的电流波动,确保控制指令的精确执行。
6. 外观与附属装置检测
包括防护罩密封性、冷却液喷射均匀性、磨轮夹持机构刚性等。通过目视检查与压力测试,排除机械结构变形或功能性失效风险。
检测周期与标准参考
建议每6个月开展一次全面检测,高负荷工况下需缩短至3个月。执行标准应参照《GB/T 17421.1-2013 机床检验通则》及设备制造商的技术规范,结合加工精度要求制定个性化检测方案。
结语
龙门导轨磨床的精准检测是保障加工质量的核心环节。企业需建立完善的检测体系,通过专业化设备与数字化分析手段,实现从静态精度到动态性能的全维度把控。对于关键参数的超差问题,应及时调整补偿参数或更换磨损部件,确保设备始终处于最佳工作状态。
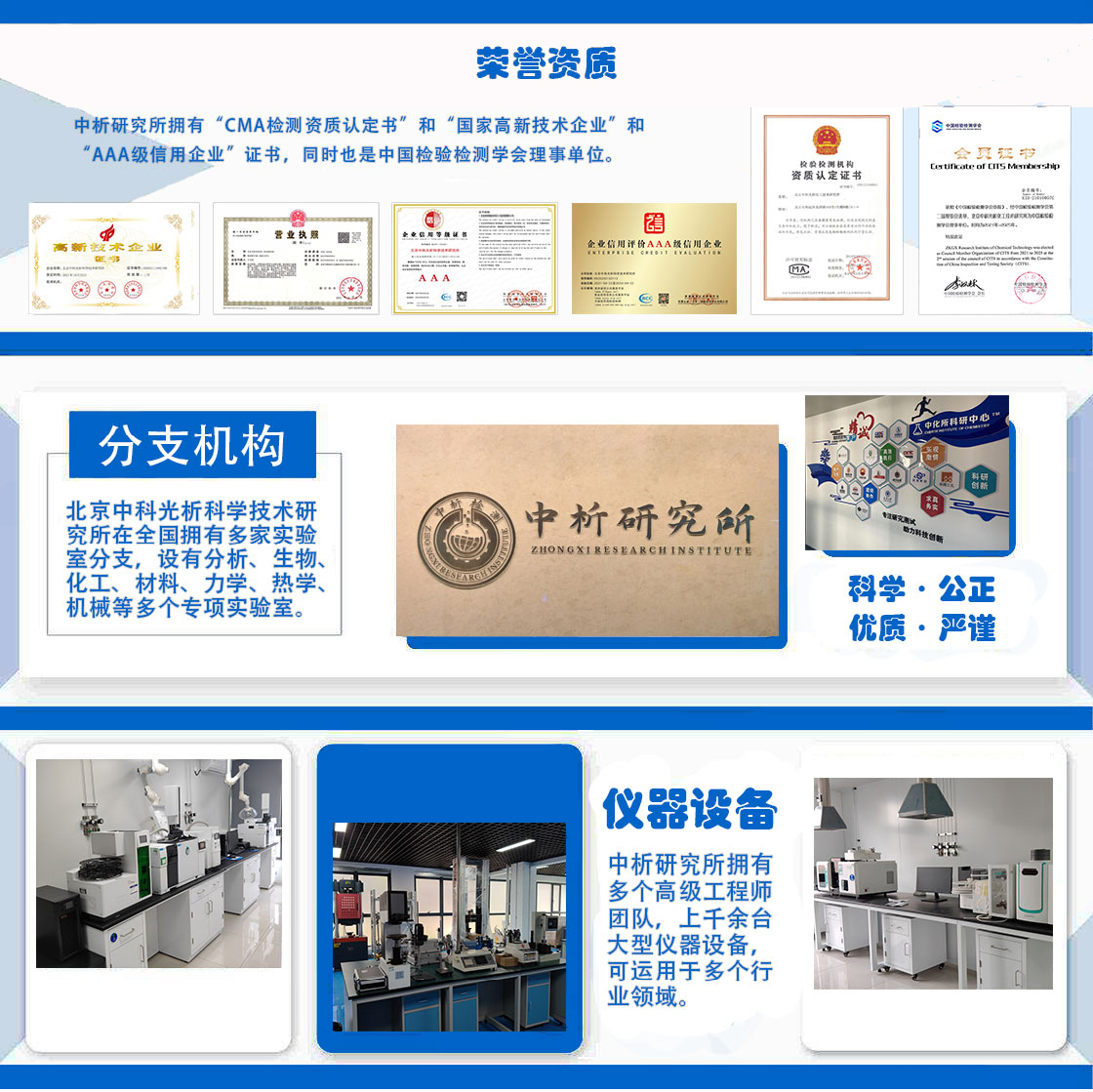
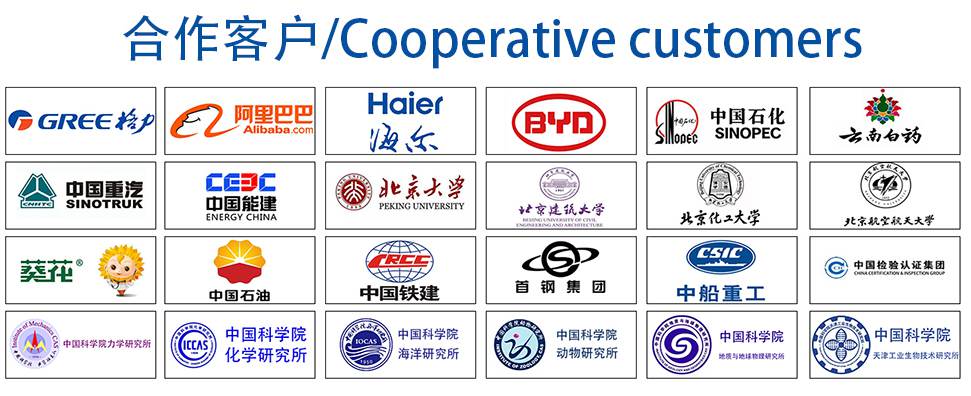