板料折弯机作为钣金加工领域的核心设备,广泛应用于汽车制造、航空航天、家电生产等行业,承担着金属板材成型的重要任务。其性能稳定性、加工精度和安全性直接关系到产品质量和生产效率。随着制造业对加工精度和自动化要求的提升,板料折弯机的定期检测与维护已成为企业设备管理中不可忽视的环节。通过系统化的检测,不仅能及时发现设备潜在故障,避免因机械故障导致的生产停滞,还能延长设备使用寿命,降低维护成本,同时确保操作人员的安全。
一、机械结构及运动精度检测
板料折弯机的机架、滑块、工作台等核心部件的结构完整性是检测的首要内容。需使用激光跟踪仪、千分表等工具测量机架垂直度、平行度及滑块运动轨迹的直线度误差,确保其符合GB/T 14349《板料折弯机精度》标准。同时需检查导轨磨损情况、同步轴传动间隙以及液压缸的同步性,避免因机械偏差导致折弯角度不稳定或工件尺寸超差。
二、液压与电气控制系统检测
液压系统需重点检测油压稳定性、油泵效率、电磁阀响应速度及管路密封性,通过压力传感器记录主缸压力曲线,排查压力波动异常现象。电气控制部分则需验证PLC程序逻辑、触摸屏人机交互功能、位置传感器精度以及伺服电机的动态响应特性,确保折弯角度补偿、后挡料定位等自动化功能正常运作。
三、安全防护装置功能性测试
依据GB 27607《机械压力机安全技术要求》,需对急停按钮、双手操作装置、光电保护装置(光栅)、防护罩联锁开关等进行功能性验证。模拟异常工况测试安全系统的响应时间,确保当操作人员进入危险区域或设备出现异常时,系统能在0.5秒内切断动力源并制动滑块,避免机械伤害事故发生。
四、模具与工装适配性检测
检测上下模具的V型开口尺寸匹配度、表面硬度及磨损量,使用三维扫描仪对比模具型面与设计图纸的偏差。针对多工位折弯机还需验证快速换模装置的定位精度,确保不同模具切换时重复定位误差≤0.05mm,避免因模具错位导致的工件报废。
五、加工精度综合验证
采用标准试件进行实际折弯实验,通过三坐标测量机检测折弯角度偏差、直线度误差及回弹量,验证设备整体加工精度是否达到JB/T 8788《板料折弯机技术条件》要求。对于数控机型还需测试后挡料定位重复精度(通常要求≤±0.01mm)、Y轴挠度补偿效果以及多轴联动同步性等关键指标。
科学规范的检测流程应包含日常点检、定期预防性检测和大修期全面检测三个层级。建议企业建立数字化检测档案,结合振动分析、油液检测等预测性维护技术,实时掌握设备健康状态。对于高精度加工场景,可委托第三方检测机构按ISO 9001标准进行年度性能认证,确保设备始终处于最佳运行状态。
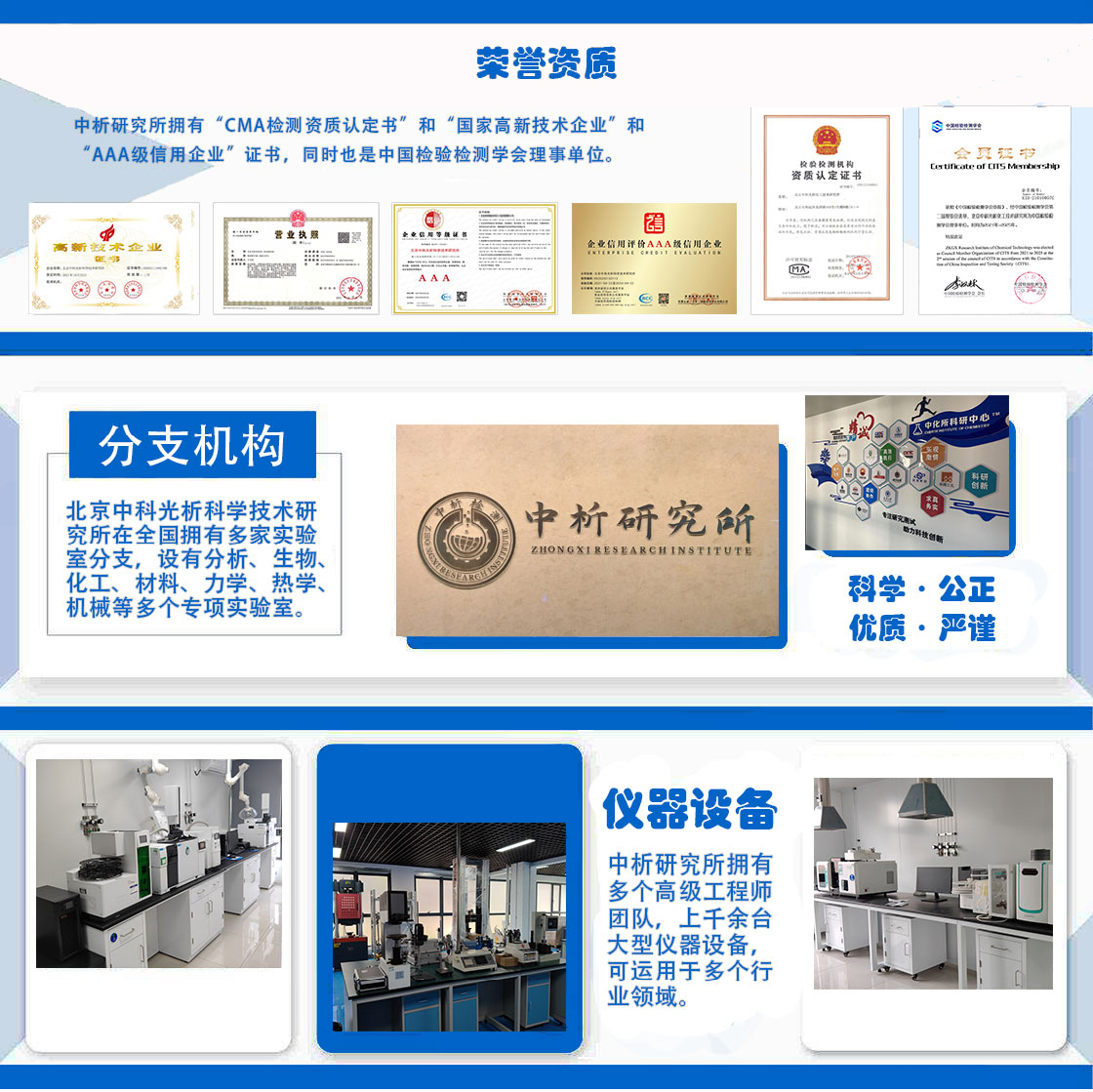
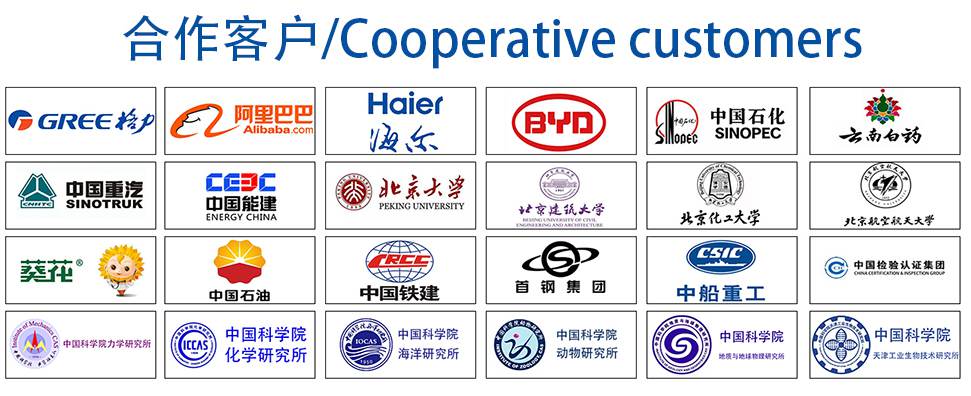