数控芯棒车床检测的重要性与核心项目
数控芯棒车床作为精密机械加工的核心设备,在航空航天、汽车制造、医疗器械等领域发挥着关键作用。其通过高精度切削工艺加工出各类芯棒、轴类零件,直接影响后续装配质量与产品性能。为确保设备长期稳定运行并满足微米级加工精度要求,定期开展系统性检测至关重要。检测工作不仅能发现潜在机械磨损、控制系统偏差等问题,还可通过数据反馈优化加工参数,延长设备寿命,提升生产效率。
核心检测项目及实施方法
1. 几何精度检测
通过激光干涉仪、电子水平仪等工具检测机床导轨的直线度、平行度、垂直度以及主轴径向跳动、轴向窜动等关键指标。重点关注X/Z轴运动轨迹偏差是否在±0.005mm以内,确保加工基准的稳定性。
2. 主轴系统性能检测
使用振动分析仪和温度传感器监测主轴在不同转速下的振动幅度(通常要求≤2μm)与温升情况(≤40℃)。同时检测主轴锥孔与芯棒配合的接触面积(需≥85%),避免因接触不良导致加工振动。
3. 定位精度与重复定位精度测试
采用球杆仪或步距规进行全行程定位误差检测,验证反向间隙补偿参数有效性。重复定位精度需满足ISO 230-2标准,通常要求≤0.003mm,确保批量加工时的尺寸一致性。
4. 刀具系统动态检测
通过刀具预调仪校准刀尖高度偏差(≤0.002mm),配合在线测量系统验证自动换刀装置(ATC)的定位重复性。同时检测刀塔分度精度(±2角秒以内),防止因分度误差导致加工特征错位。
5. 冷却润滑系统效能评估
检测切削液压力(0.5-1.2MPa)、流量(≥20L/min)及过滤精度(≤25μm),使用红外热像仪监测加工区域散热效果。重点排查油雾回收装置密封性,避免环境污染与设备腐蚀。
6. 数控系统功能验证
全面测试G代码/M代码执行准确性,验证圆弧插补、螺纹切削等特殊指令的运行精度。同步检查伺服驱动器电流波动(±5%以内)、反馈系统分辨率(≤0.1μm),确保控制系统响应灵敏无滞后。
7. 加工试件综合精度检测
选用标准试件(如NAS 979圆柱-圆锥试件)进行实际切削测试,使用三坐标测量机(CMM)检测尺寸公差(IT6级)、圆度(≤0.005mm)及表面粗糙度(Ra≤0.8μm),全面验证机床综合加工能力。
检测周期与数据管理建议
建议建立三级检测机制:日常点检(每班次)、定期维护(每月)与年度精度校准。采用数字化管理平台记录历史检测数据,通过趋势分析预判部件磨损周期,实现预防性维护。对于关键参数应建立动态公差带模型,当检测值超出预警阈值时自动触发维修工单。
通过系统化的检测与维护,数控芯棒车床可长期保持出厂精度的85%以上,有效降低废品率并提升复杂零件的加工合格率,为智能制造提供可靠保障。
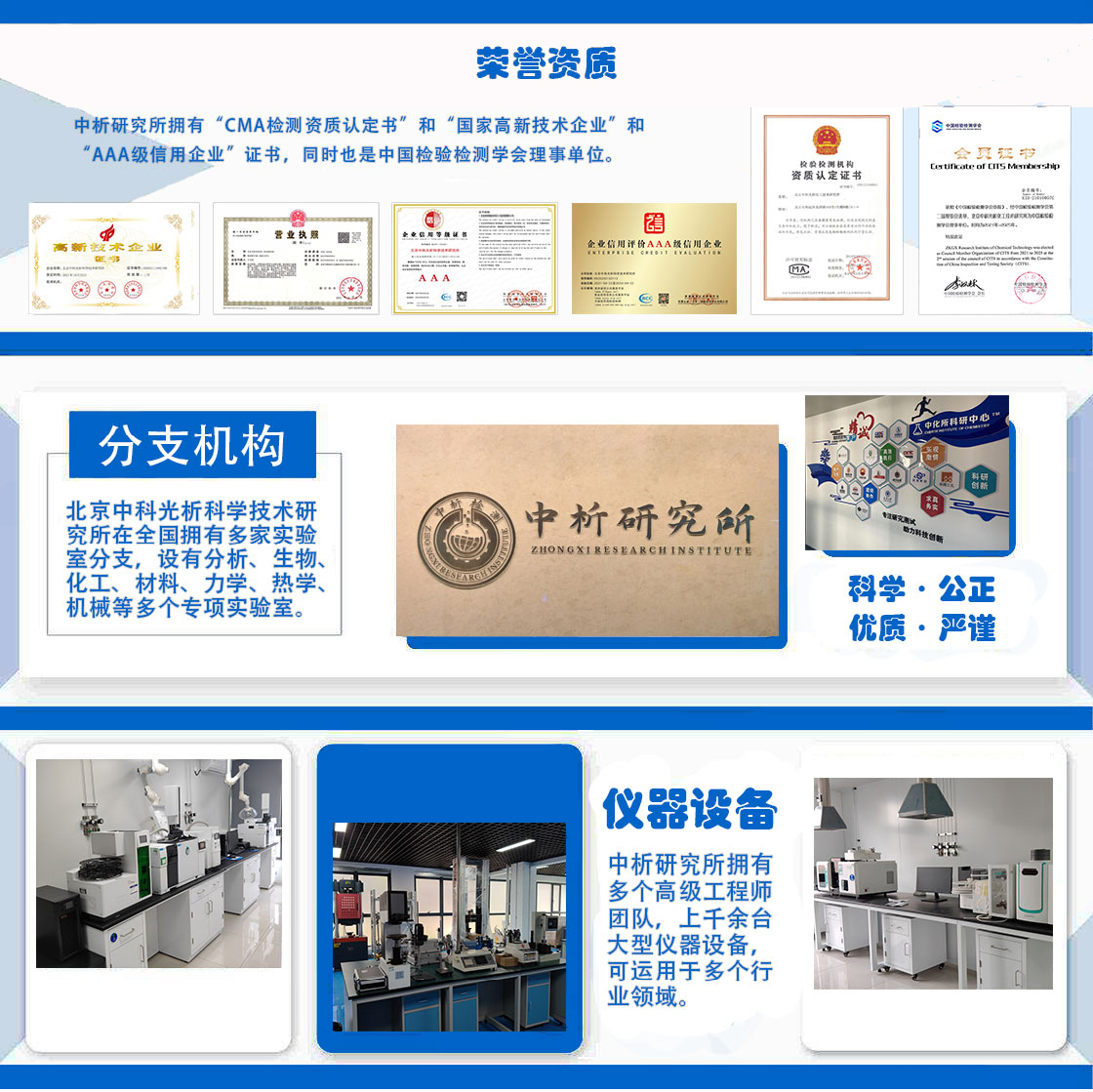
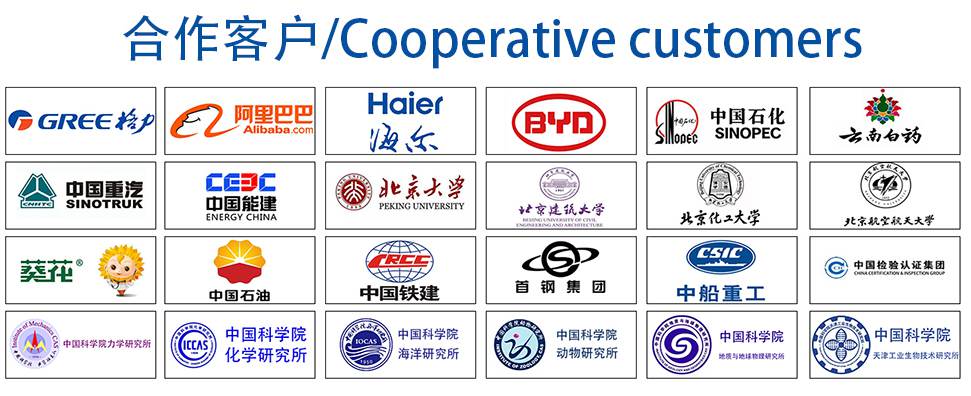