卡盘多刀车床检测的关键项目与技术要点
卡盘多刀车床作为机械加工领域的重要设备,其加工精度、稳定性和安全性直接影响零部件的生产质量。随着工业自动化水平的提升,此类车床通过多刀具协同作业实现了复杂零件的高效加工,但同时也对设备状态提出了更高要求。定期开展系统化检测是保障设备性能的核心措施,能够有效预防刀具异常磨损、加工误差累积等问题,同时降低因设备故障导致的停机风险。检测工作需围绕机械结构、动力系统、控制系统三大模块展开,并结合动态运行参数与静态精度数据进行综合评估。
一、卡盘系统精度检测
作为工件的核心夹持装置,卡盘的同心度与夹持力直接影响加工定位精度。检测时需使用三坐标测量仪或专用检具测量三爪同轴度,误差应控制在0.01mm以内。同步检测液压/气动系统的压力稳定性,确保夹紧力波动范围不超过设定值的±5%。对于长期使用的卡盘,需重点检查导向槽磨损情况,避免因局部磨损导致工件偏移。
二、多刀架定位精度验证
多刀车床的核心优势在于多刀具快速切换能力。检测需通过激光干涉仪验证各刀位坐标重复定位精度,X/Z轴重复定位误差需≤0.005mm。同时进行刀具切换动作的时序测试,记录换刀机构在连续50次操作中的响应时间偏差,要求波动幅度小于0.3秒。刀塔锁紧后的径向跳动量应使用千分表检测,允许公差为0.008mm。
三、主轴系统动态性能测试
主轴作为动力输出核心,检测需涵盖转速稳定性与热变形控制。通过振动传感器采集不同转速(500-3000rpm)下的振幅值,空载运行时振动速度有效值应≤2.5mm/s。连续运行2小时后,采用红外热像仪监测主轴温升,轴承部位温度不得超过环境温度+35℃。同步使用动平衡仪检测主轴-卡盘组件的动态平衡等级,残余不平衡量需满足G2.5标准。
四、数控系统参数校准
针对数控型多刀车床,需对伺服系统进行闭环检测。通过球杆仪检测各轴运动轨迹圆度误差,半径偏差应≤15μm。检查反向间隙补偿值设定,使用步距规测量实际间隙与系统补偿值的匹配度,误差需控制在0.002mm内。同时验证G代码执行过程中各轴加减速曲线与设定参数的吻合度,避免因动态响应滞后导致的轮廓误差。
五、润滑与冷却系统效能评估
检测导轨润滑油膜厚度是否达到3-5μm标准,使用油液颗粒度分析仪判定油品污染等级,NAS等级需≤8级。冷却液流量需通过流量计实测,对比理论值与实际值的偏差应<10%。重点检查多刀位切削时的冷却覆盖均匀性,使用试纸法检测各刀具加工区域的冷却液覆盖率,要求达到95%以上。
通过以上系统性检测,可精准掌握卡盘多刀车床的综合状态,并为设备维护提供量化依据。建议结合生产强度制定三级检测机制:日常点检(8小时/次)、周期保养(200小时/次)、深度检测(2000小时/次),从而在保障加工精度的同时实现设备全生命周期管理。
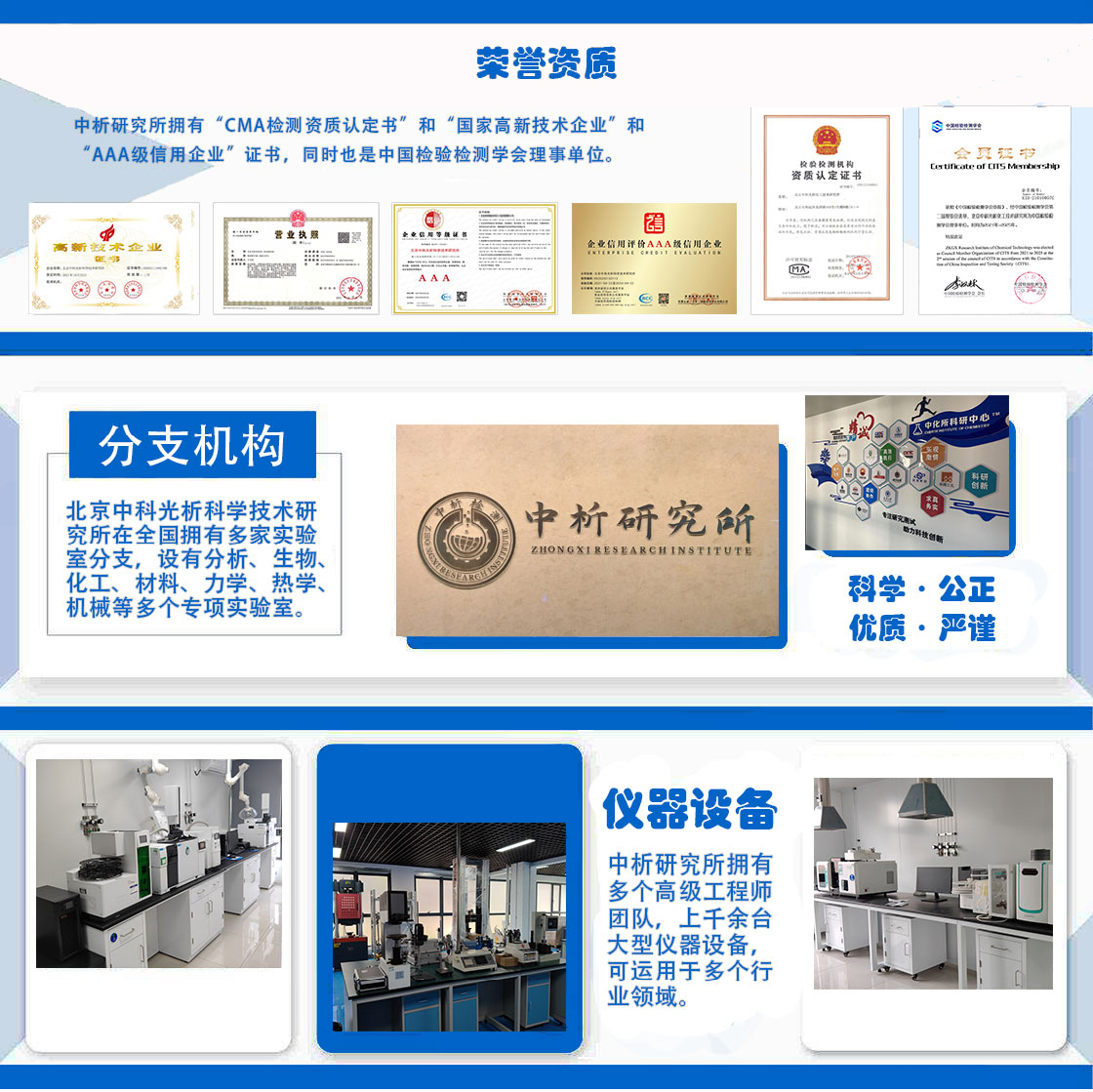
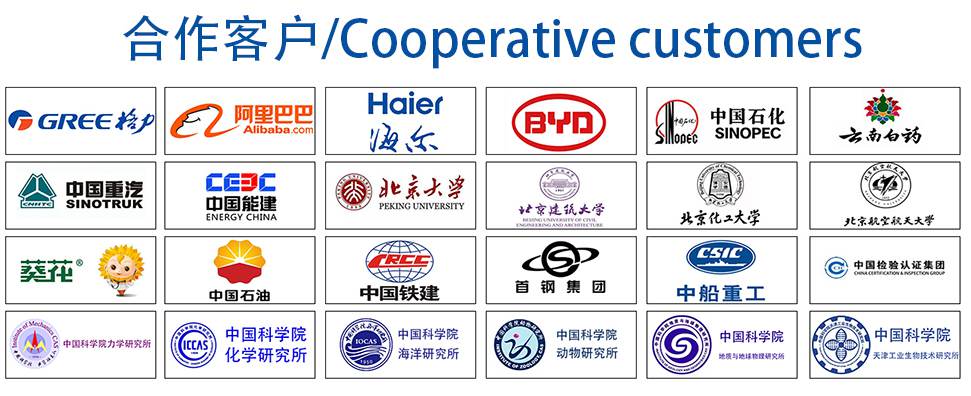