数控立式钻床检测项目概述
数控立式钻床作为现代机械加工领域的重要设备,其精度、稳定性和可靠性直接影响加工件的质量与生产效率。定期对设备进行系统性检测是保障其性能的关键措施。检测项目需覆盖机械结构、数控系统、加工精度、安全防护等多个维度,通过量化数据评估设备状态,及时发现潜在问题,确保设备长期稳定运行。
核心检测项目及方法
1. 几何精度检测
通过激光干涉仪或电子水平仪检测机床导轨的直线度、平面度及垂直度误差,验证X/Y/Z轴的运动精度是否符合GB/T 17421标准。同时检测主轴轴线与工作台面的垂直度,误差需控制在0.02mm/300mm范围内。
2. 主轴性能检测
使用转速表测量主轴实际转速与设定值的偏差,检查加速/减速响应时间。通过振动测试仪分析主轴在最大负载下的径向跳动(≤0.01mm)和轴向窜动(≤0.008mm),评估轴承磨损状态。
3. 定位精度与重复定位精度
采用球杆仪或光栅尺反馈系统,按ISO 230-2标准执行双向定位精度测试。重复定位精度需满足±0.005mm要求,反向间隙补偿后残留误差不超过0.003mm。
4. 加工性能验证
通过试切标准化试件(如NAS试件),检测孔距精度、孔径公差及表面粗糙度(Ra≤1.6μm)。同时监测切削过程中的主轴功率波动,异常振动需及时排查。
辅助系统专项检测
1. 数控系统功能测试
验证G代码执行准确性、刀具补偿功能有效性及急停响应速度(≤0.5秒)。检查伺服驱动系统过载保护功能,模拟断刀、超程等故障时的报警灵敏度。
2. 液压与气动系统检测
检测主轴松刀压力稳定性(波动≤0.2MPa),测量刀具夹持力衰减情况。气动系统需进行保压试验,10分钟内压力下降不超过初始值的5%。
3. 安全防护装置检查
测试防护门互锁功能、紧急停止按钮响应及冷却液泄漏防护性能。安全光栅的有效检测距离误差需控制在±10mm以内。
检测流程与周期建议
推荐每年实施一次全面检测,重点企业可缩短至6个月。检测流程需遵循:设备预热→基础精度校准→动态性能测试→数据对比分析→故障诊断与调修的标准化路径。建立设备精度档案,通过趋势分析预判部件寿命,实现预防性维护。
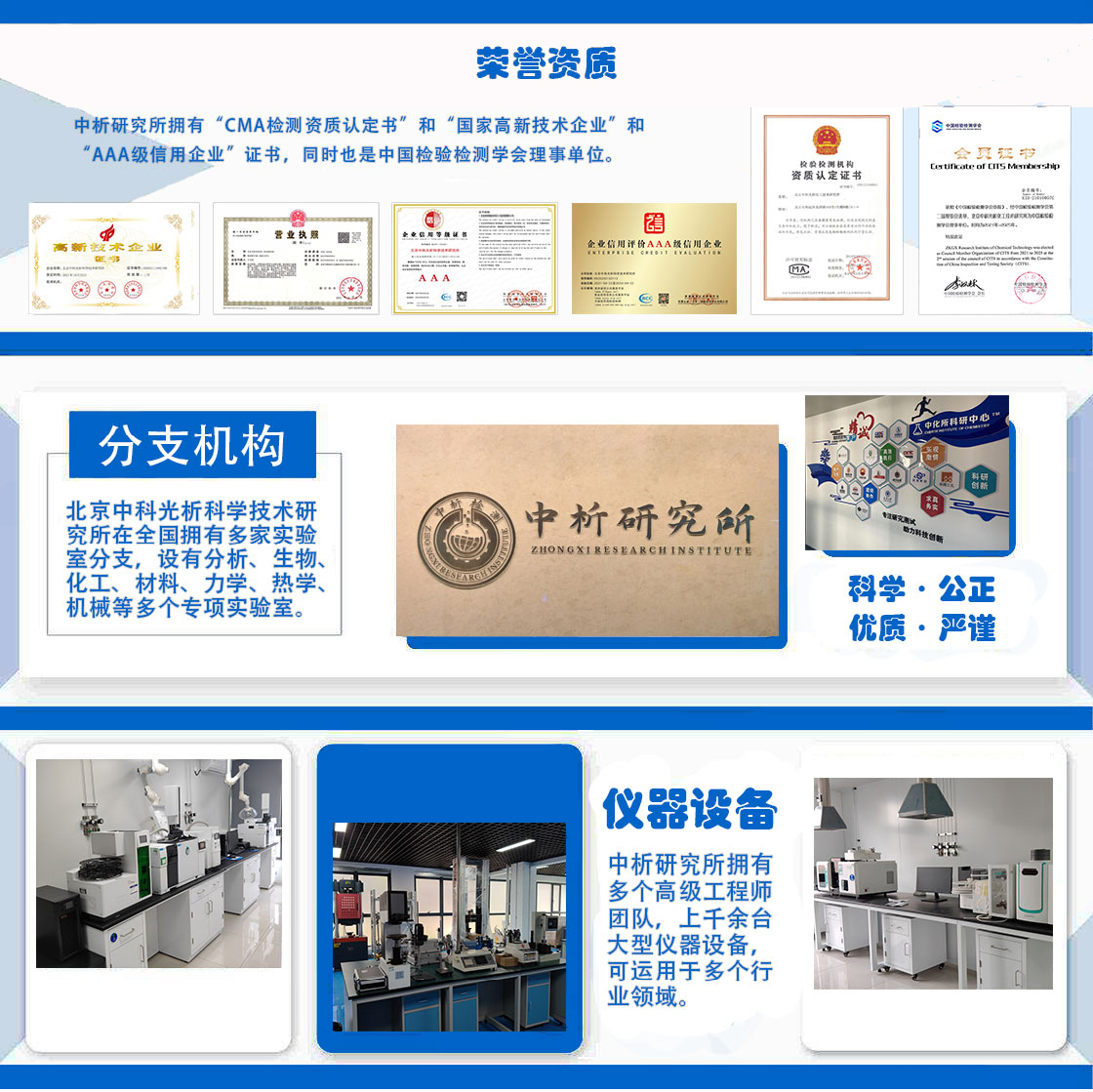
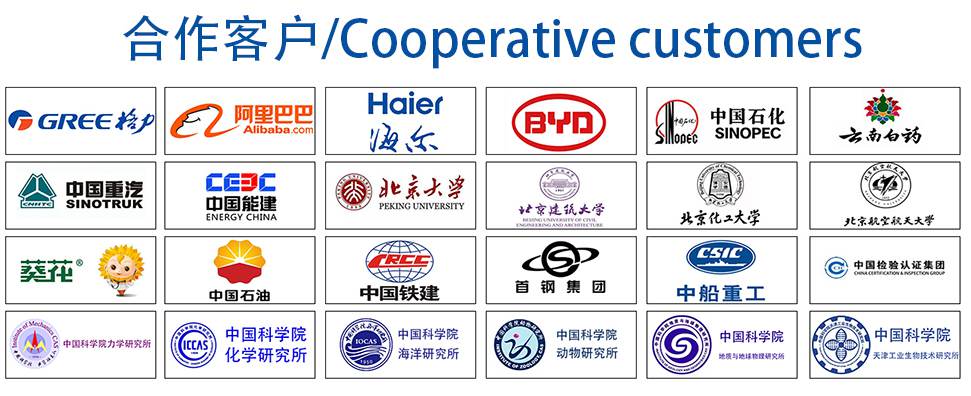