铝合金铸件检测的重要性及核心项目解析
铝合金铸件因其轻量化、高强度、耐腐蚀等特性,在汽车制造、航空航天、电子设备及建筑领域得到广泛应用。为确保铸件的质量符合设计要求并满足实际工况需求,系统化的检测流程至关重要。通过科学的检测手段能够发现潜在缺陷、优化生产工艺,并提高产品可靠性。本文将围绕铝合金铸件检测的核心项目展开详细解读,帮助企业和检测机构建立完善的质控体系。
一、化学成分分析
通过光谱分析仪(OES)或电感耦合等离子体发射光谱(ICP-OES)精确测定Al、Si、Mg、Cu等元素的含量,确保合金成分符合GB/T 1173或ASTM B179标准要求。重点控制Fe、Zn等杂质元素的超标风险,避免影响铸件的耐腐蚀性和机械性能。
二、力学性能测试
采用万能材料试验机进行拉伸试验(测定抗拉强度、屈服强度、延伸率),配合布氏/洛氏硬度计检测硬度值。对于重要承力部件需增加疲劳强度测试,模拟实际工况下的循环载荷承受能力。
三、金相组织检验
通过金相显微镜观察α-Al基体、共晶硅形态及金属间化合物分布,评估晶粒尺寸(ASTM E112标准)和致密度。重点关注气孔率(应<2%)、缩松等缺陷,使用图像分析软件进行定量评估。
四、尺寸精度检测
运用三坐标测量机(CMM)检测关键部位的尺寸公差(通常要求CT6-CT8级),配合轮廓投影仪验证复杂曲面精度。需特别关注分型线错位、模具磨损导致的尺寸偏差问题。
五、表面质量检查
目视检查结合电子显微镜分析表面光洁度(Ra≤6.3μm),检测冷隔、流痕、粘砂等表面缺陷。采用涡流检测仪排查皮下气孔,通过荧光渗透检测(PT)发现微裂纹(灵敏度可达0.01mm)。
六、无损检测(NDT)
1. X射线检测(RT):识别内部缩孔、夹杂等缺陷,数字化成像系统可实现缺陷三维定位
2. 超声波检测(UT):适用于厚壁件内部缺陷检测,可识别≥φ2mm的缺陷
3. 工业CT扫描:进行全三维结构分析,检测精度达到微米级
随着智能制造的发展,当前检测技术正向智能化、在线化方向升级。建议企业建立包含上述六大模块的检测体系,并依据铸件用途(如汽车增压器壳体需增加热疲劳测试)调整检测重点,确保质量控制的全方位覆盖。
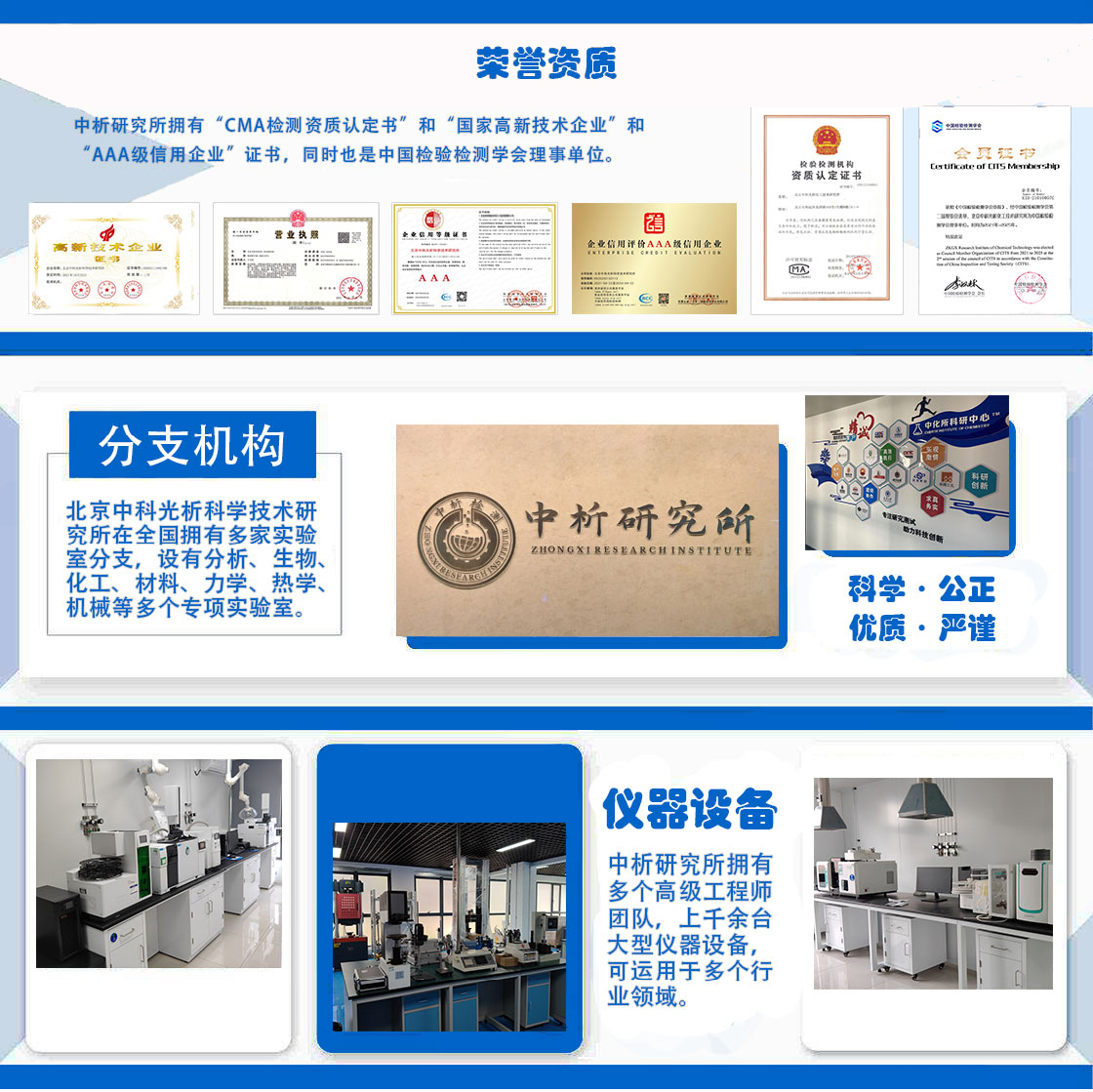
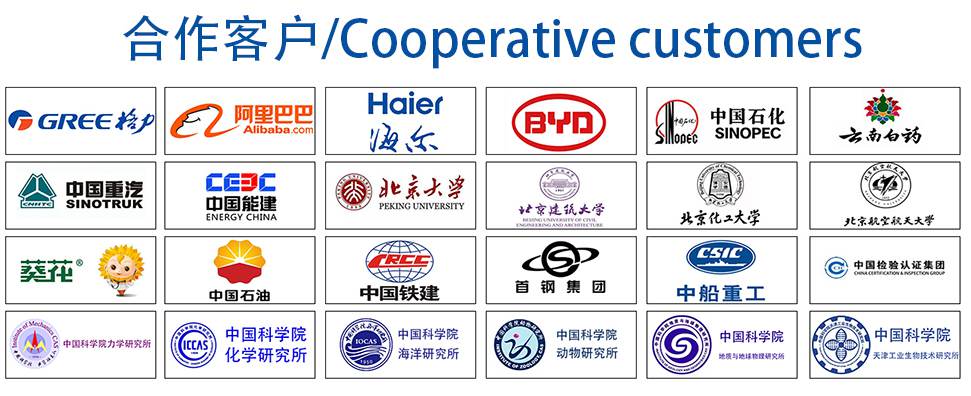