数控多面切削车床检测的意义与核心内容
数控多面切削车床作为现代精密制造领域的核心设备,其加工精度、稳定性和效率直接影响产品质量与生产成本。随着工业4.0的推进和复杂零件加工需求的增长,定期进行系统性检测成为保障设备性能的关键环节。检测工作不仅能够发现潜在故障风险、延长设备寿命,还能通过数据反馈优化加工参数,提高生产线的智能化水平。检测项目需覆盖几何精度、动态性能、切削能力、电气系统及安全规范等多个维度,形成完整的设备健康状况评估体系。
一、几何精度检测项目
几何精度是车床性能的基础指标,重点包括:主轴径向跳动(0.003mm以内)、轴向窜动(0.002mm以内)的激光干涉仪检测;X/Y/Z轴导轨直线度(每300mm≤0.008mm)的电子水平仪测量;多工位转塔的重复定位精度(±0.005mm)验证。针对多面切削特性,还需使用球杆仪检测联动轴的轨迹精度,确保复杂曲面的加工一致性。
二、动态性能测试
在模拟加工状态下进行动态检测:通过加速度传感器分析主轴在2000-8000rpm范围内的振动频谱,识别轴承磨损或动平衡异常;利用红外热像仪监测连续工作4小时后的热变形量,要求关键部位温升≤12℃;执行G00快速定位冲击测试,验证伺服系统响应速度与制动稳定性,重复定位偏差需控制在0.01mm以内。
三、切削能力验证
采用标准试件进行实际加工测试:包括阶梯轴多面切削的尺寸公差(IT6级)、表面粗糙度(Ra0.8μm)检测;异形轮廓的形位公差(同轴度≤0.015mm)验证;硬质合金刀具在断续切削工况下的寿命测试(连续加工50件以上无崩刃)。同时监测切削力波动,通过功率传感器分析主轴负载均衡性。
四、数控系统与传感器检测
使用专用诊断软件检查数控系统的I/O信号响应时间(≤2ms)、PLC程序执行周期(≤50ms);对光栅尺/编码器进行定位信号完整性测试,要求信号波动幅度<5%;通过模拟量输入输出校准,确保温度、压力等传感器采集误差率<0.5%。同时验证宏程序调用、刀具补偿等高级功能的执行精度。
五、安全防护与规范性检测
全面检查安全联锁装置:包括急停按钮响应时间(≤0.5s)、防护门光电传感器有效性、液压过载保护阈值(额定值110%触发);测量工作区域噪音等级(≤75dB(A));核查润滑系统油压稳定性(波动值<0.2MPa)。特别针对多面切削的刀具干涉风险,需进行三维空间碰撞模拟验证。
检测周期与标准执行
常规检测应每500小时或每月实施一次,大修后需执行72小时连续运行测试。检测过程需严格参照GB/T 17421.2《机床检验通则》和ISO 10791-7多轴机床标准,同时结合设备制造商的技术规范。建议建立检测数据库,通过趋势分析实现预测性维护,将设备故障率降低40%以上。
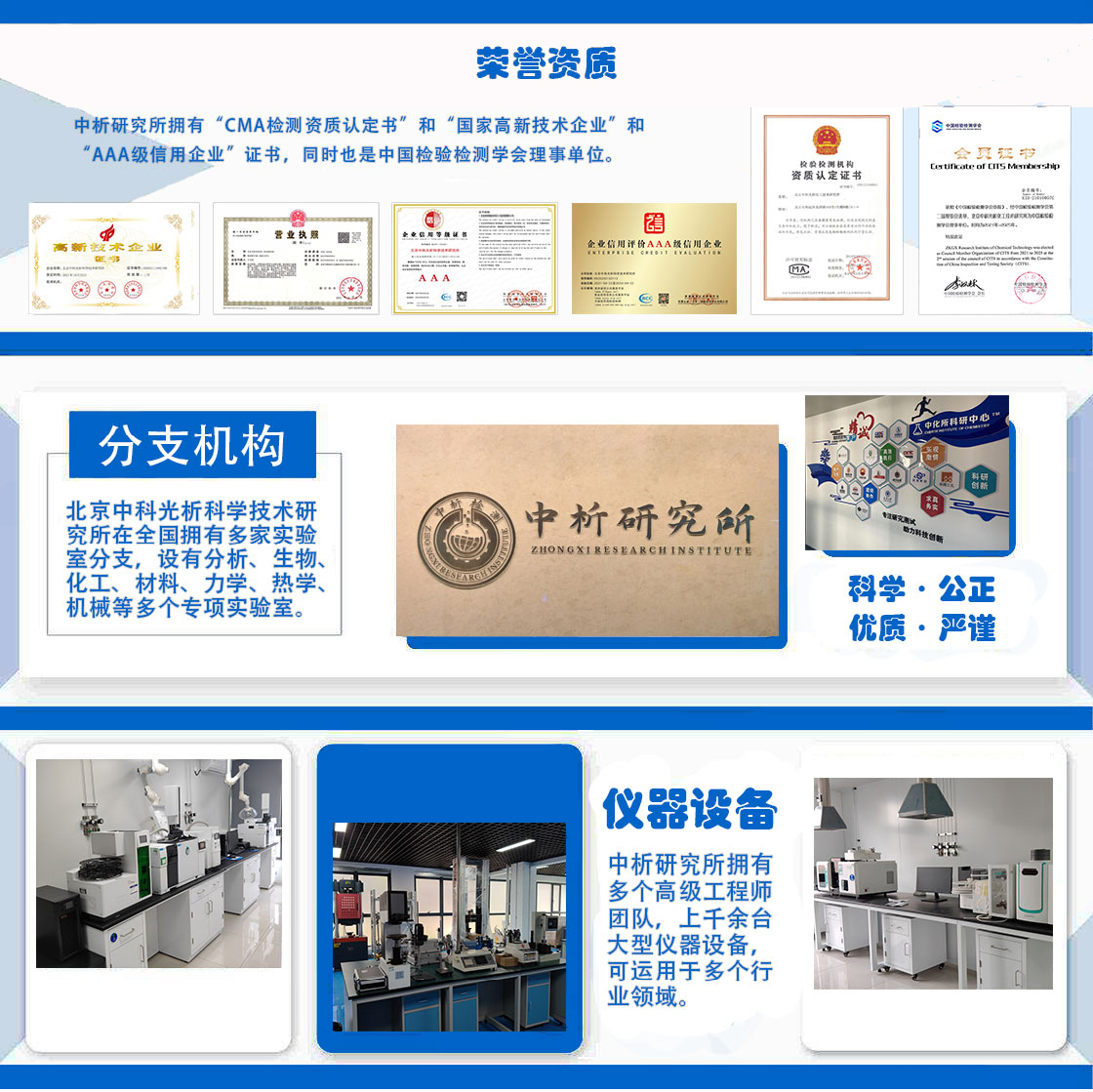
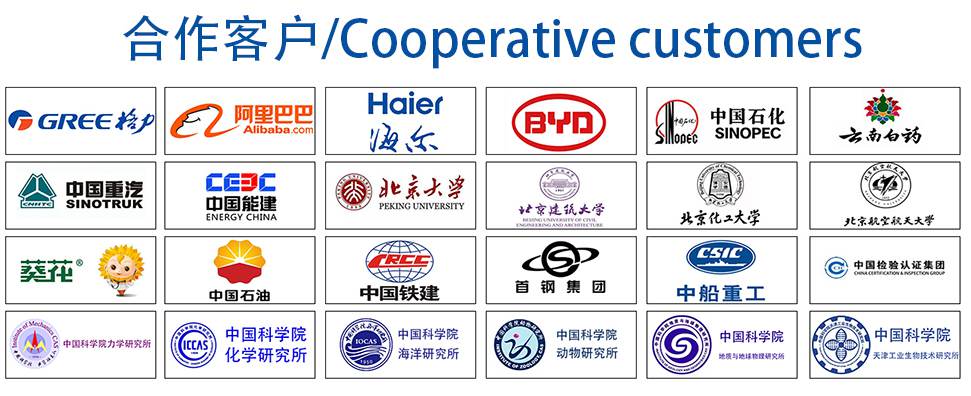