深孔钻镗床检测项目的专业解析
深孔钻镗床作为机械制造领域的重要加工设备,其加工精度直接影响枪管、油缸、液压阀体等深孔类零部件的产品质量。随着现代工业对深孔加工精度的要求日益严苛,设备精度检测已成为机床维护与生产保障的核心环节。通过系统化的检测项目组合,可精准识别机床精度劣化、部件磨损等隐患,保障加工孔径公差、直线度、表面粗糙度等关键指标满足ISO/DIN标准要求。
一、几何精度检测体系
该模块重点验证机床基准面的空间精度,包含导轨直线度(要求≤0.02mm/m)、立柱垂直度(允差0.03mm/1000mm)、工作台平面度(≤0.015mm)等核心指标。使用激光干涉仪配合电子水平仪进行三维空间补偿测量,特别关注Z轴与B轴(主轴箱)的复合运动轨迹精度,确保深孔加工的同轴度误差控制在0.05mm以内。
二、主轴系统性能验证
采用非接触式振动分析仪检测主轴径向跳动(标准值≤0.008mm),搭配热成像仪监测高速运转时的温升曲线(温升应<35℃)。对于BTA深孔钻床,还需测试2000-8000rpm区间内的动态刚度,使用扭矩传感器记录切削抗力的突变情况,防止因主轴系统谐振导致的振纹缺陷。
三、伺服进给系统检测
通过球杆仪进行圆度测试评估X/Y轴联动精度(目标值≤15μm),采用光栅尺闭环检测定位重复精度(允差±0.005mm)。针对油压驱动的深孔钻床,需用压力传感器组监测油缸背压波动(应<0.5MPa),同时检测导轨副的PV值(压力×速度)是否超出润滑膜承载极限。
四、冷却液系统效能评估
建立压力-流量联合测试平台,验证高压泵组在8-15MPa工况下的流量稳定性(波动率<3%)。使用颗粒计数器检测过滤系统的净化能力(目标清洁度NAS1638 6级),并对内排屑通道进行内窥镜检查,确保无铁屑沉积导致的二次划伤风险。
五、智能诊断系统校准
针对配备刀具状态监控系统的数控深孔钻镗床,需使用标准信号发生器校准振动传感器、温度传感器的检测灵敏度(误差<5%)。通过模拟不同切削载荷验证自适应控制模块的响应特性,确保断屑检测系统能在0.5秒内触发保护机制。
系统化的检测流程应结合机床使用频次制定检测周期,通常建议每500小时进行关键项点快速检测,每2000小时执行全项目精度复验。通过构建检测大数据平台,可实现机床精度衰退趋势预测,为预知性维修提供科学依据,将非计划停机时间降低40%以上。
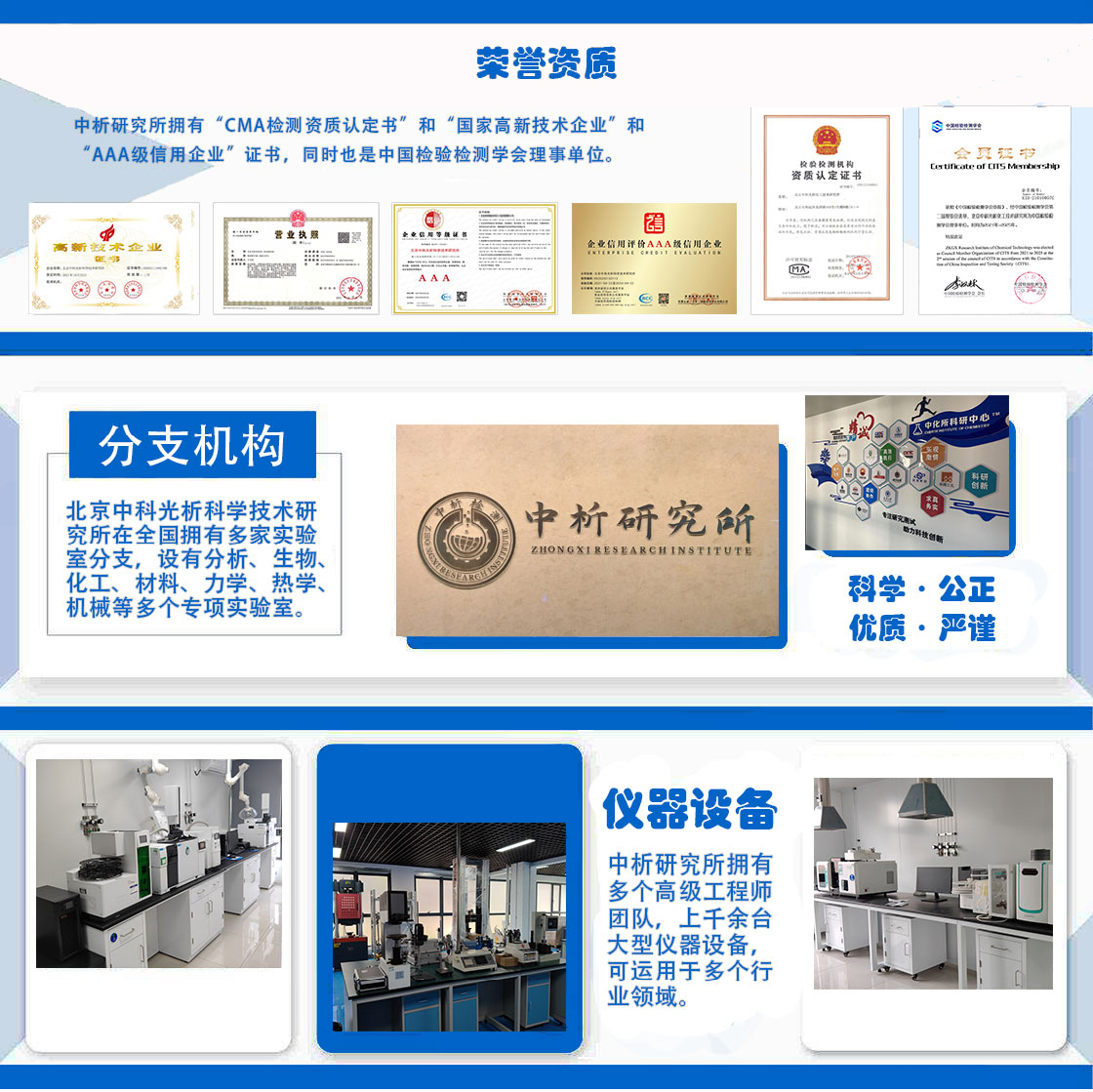
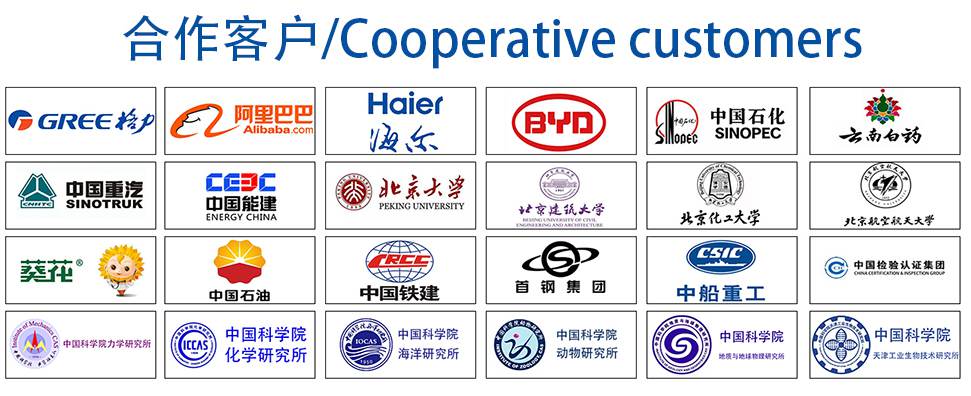