车轮车床参数检测的重要性
车轮车床作为轨道交通、工程机械等领域核心加工设备,其性能直接影响车轮加工精度和运行安全性。随着现代工业对产品公差和表面质量要求的提升,对车轮车床的参数检测提出了更高标准。参数检测不仅涉及设备初始安装调试的验收,还贯穿于日常维护、周期性校准及故障诊断的全生命周期管理中。通过科学、系统的参数检测,可确保车床主轴回转精度、导轨直线度、切削稳定性等关键指标符合设计要求,从而保障轮对的尺寸精度、几何公差及表面粗糙度,避免因设备性能偏差导致的安全隐患或经济损失。
核心检测项目及方法
1. 几何精度检测
重点检测主轴径向跳动(ISO 230-7标准)、导轨直线度(激光干涉仪测量)及刀架重复定位精度(千分表多点测试)。需在空载和负载状态下分别测试,对比热变形对精度的影响。
2. 运动性能检测
包括主轴转速均匀性(光电测速仪)、进给系统同步性(双频激光干涉仪)及加减速响应时间(动态信号分析仪)。需验证各轴联动时速度波动是否控制在±2%以内。
3. 切削力与振动分析
采用三向测力仪监测切削力分布,结合振动传感器(频响范围0-10kHz)分析谐波成分。重点检测主振频率是否避开工件-刀具系统的固有频率段,防止共振导致的表面波纹。
4. 热稳定性检测
通过红外热像仪连续监测主轴箱、导轨等关键部件温升曲线,评估连续加工4小时后的热变形量。要求温度漂移导致的定位误差≤0.01mm/℃。
5. 数控系统参数验证
检查G代码解析精度(示波器观测脉冲波形)、反向间隙补偿值(激光干涉仪动态测量)及PID控制参数匹配性(阶跃响应测试),确保位置环增益误差<0.005mm。
检测标准与周期管理
检测需依据GB/T 23575-2009《数控车轮车床精度检验》和ISO 13041-6车床测试规范,结合设备使用强度建立分级检测制度:新设备全项检测(72项指标)、大修后重点复检(45项)、季度常规检测(28项)。建议采用数字化检测平台,实现参数趋势分析和预防性维护决策。
结语
车轮车床参数检测是保障设备加工能力的核心手段,需综合运用机械测量、传感器技术及数据分析方法。随着智能检测技术的普及,未来将更多融入在线监测系统和数字孪生模型,实现从被动维护到主动预测的转变,为轨道交通装备制造提供更可靠的技术支撑。
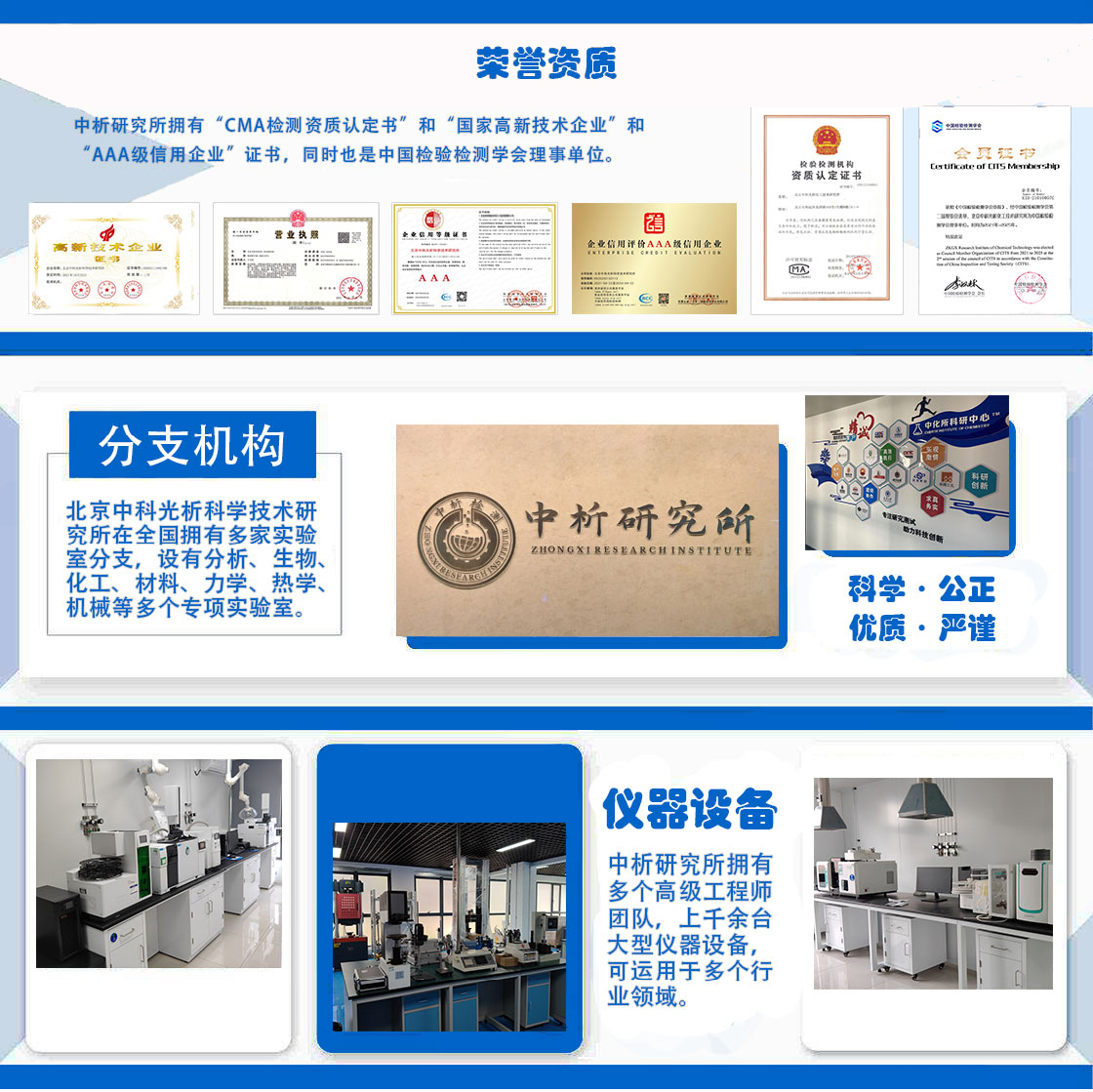
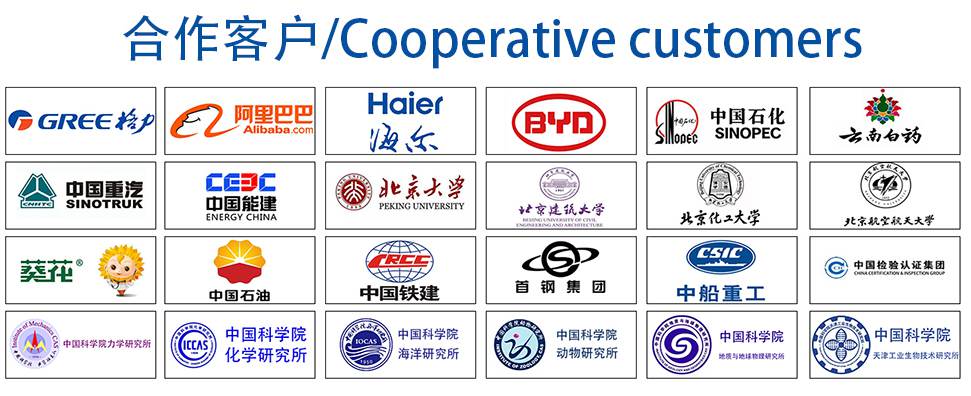