高精度卧式车床检测:关键技术指标与实施流程
高精度卧式车床作为机械制造领域的核心设备,其加工精度直接影响零件质量与工艺稳定性。随着现代工业对微米级甚至亚微米级公差要求的不断提升,车床的综合性能检测已成为保障生产效率和产品质量的关键环节。通过系统性检测,可及时发现床身导轨磨损、主轴跳动、进给系统误差等潜在问题,避免因设备偏差导致的批量性加工缺陷。目前,国际标准ISO 13041和国家标准GB/T 16462系列均对数控卧式车床的检测方法及精度等级作出明确规定,涵盖几何精度、动态性能、热稳定性等十余项核心指标。
一、几何精度检测项目
1. 床身导轨直线度与平行度:采用激光干涉仪或电子水平仪对导轨纵向、横向进行分段测量,误差需控制在0.01mm/1000mm以内。
2. 主轴系统精度检测:包含主轴径向跳动(≤0.005mm)、端面跳动(≤0.008mm)及轴向窜动(≤0.003mm)的精密测试。
3. 刀架运动直线度:通过标准试棒配合千分表进行X/Z轴复合运动轨迹检测,确保刀轨偏差符合H级精度标准。
二、动态性能检测指标
1. 主轴温升与热变形:连续运转4小时后,主轴前端温升不超过25℃,径向热位移量需≤5μm。
2. 进给系统定位精度:使用激光干涉仪执行全行程双向定位测试,重复定位误差应稳定在±1.5μm范围内。
3. 振动与噪声测试:主传动系统在最高转速工况下,振动速度有效值≤2.8mm/s,噪声级不高于75dB(A)。
三、加工精度验证体系
通过典型试件切削实验完成最终精度验证:
- 圆柱试件圆度误差:直径≤100mm时允差0.005mm
- 端面平面度:直径200mm范围内≤0.008mm
- 螺纹中径误差:需符合ISO 1级精度标准
检测过程需使用三坐标测量机(CMM)和表面粗糙度仪进行多维度数据采集。
四、智能化检测技术应用
现代检测方案已集成在线监测系统(如嵌入式传感器网络)和AI数据分析平台,实现:
1. 实时监测主轴轴承预紧力变化
2. 自动补偿导轨磨损引起的定位偏差
3. 预测性维护提醒功能,降低设备突发故障风险
高精度卧式车床的全面检测应遵循"静态检测-动态测试-加工验证"三位一体的评估体系,建议每500工作小时或重大工艺调整后执行系统性检测。通过严格执行检测规范,可确保设备长期保持标称精度,同时降低加工废品率30%以上,为企业创造显著经济效益。
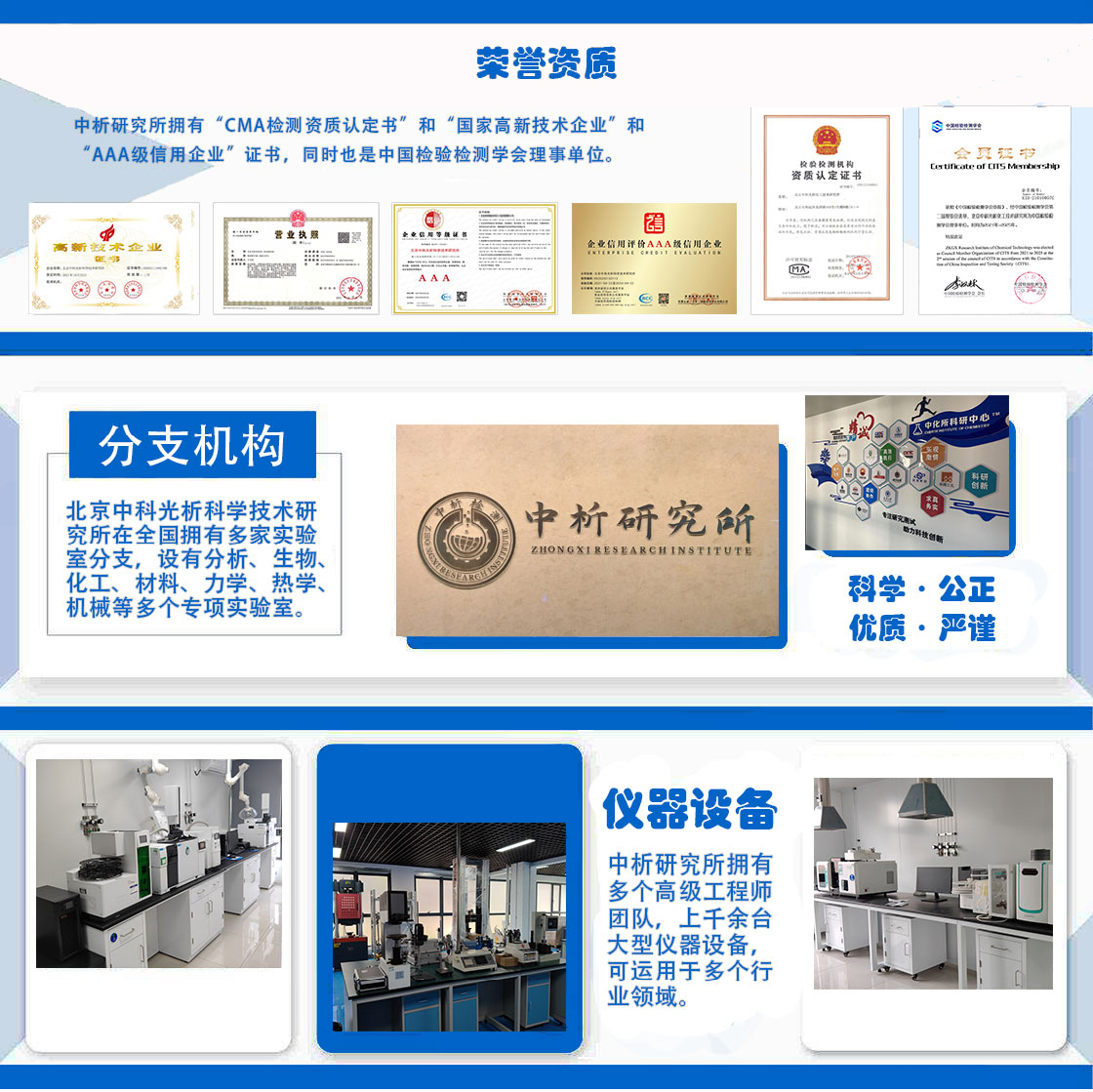
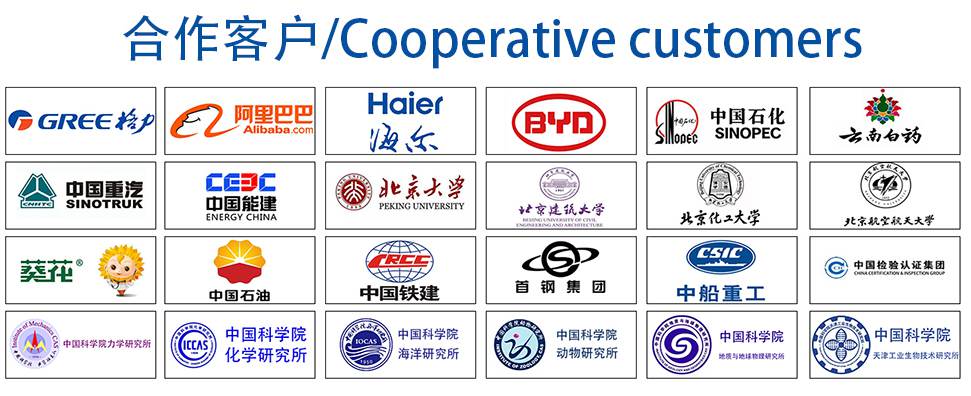