弯管机参数检测的重要性及核心内容
弯管机作为金属管材加工的核心设备,其性能参数直接影响加工精度、设备寿命及操作安全性。随着工业领域对管件成型要求的提高,弯管机参数检测已成为设备验收、日常维护和质量控制的核心环节。通过系统性检测,可验证设备是否符合设计标准,确保加工管材的弯曲角度、圆度、壁厚均匀性等关键指标达到工艺要求,同时为优化加工参数和生产效率提供数据支持。
弯管机参数检测的核心项目
1. 几何参数检测
• 弯曲角度精度:使用激光测距仪或三维坐标测量仪,对比实际弯曲角度与设定值的偏差(通常要求公差≤±0.5°)
• 弯曲半径一致性:通过轮廓投影仪测量不同批次产品的半径重复精度
• 管材直径适应性:验证设备对不同规格管材的夹持精度(误差需≤0.1mm)
2. 力学性能参数检测
• 最大弯曲力矩:通过扭矩传感器测试设备在额定载荷下的持续工作能力
• 回弹量测定:采用应变片测量管材卸模后的弹性变形量(需控制≤2°)
• 液压系统压力稳定性:使用压力变送器记录主油缸压力波动(允许偏差≤1.5MPa)
3. 运动控制系统检测
• 伺服电机定位精度:运用光栅尺验证转臂旋转定位精度(目标值≤0.01mm)
• 送料机构重复定位:采用激光干涉仪检测送料行程重复性(要求≤±0.05mm)
• 多轴同步性能:通过运动控制器分析弯曲轴与助推轴的协同误差
4. 安全装置检测
• 过载保护响应时间:模拟超载工况测试安全阀开启速度(≤0.3秒)
• 紧急制动性能:测量急停按钮触发后设备完全静止所需时间
• 防护装置有效性:验证光栅安全门与设备联锁功能的可靠性
5. 综合性能测试
• 连续工作稳定性:进行8小时不间断加工测试,记录参数漂移情况
• 能耗效率评估:对比不同工况下的电能/液压能转换效率
• 噪声与振动检测:使用声级计和振动分析仪测量设备运行时的物理环境影响
检测标准与周期管理
检测过程需参照GB/T 28761-2012《数控弯管机》等国家标准,结合设备制造商的技术规范执行。建议新设备安装后进行全项目检测,日常生产每500小时开展关键参数检测,每年实施一次全面性能评估。通过建立数字化检测档案,可实现设备状态的可视化监控与预测性维护。
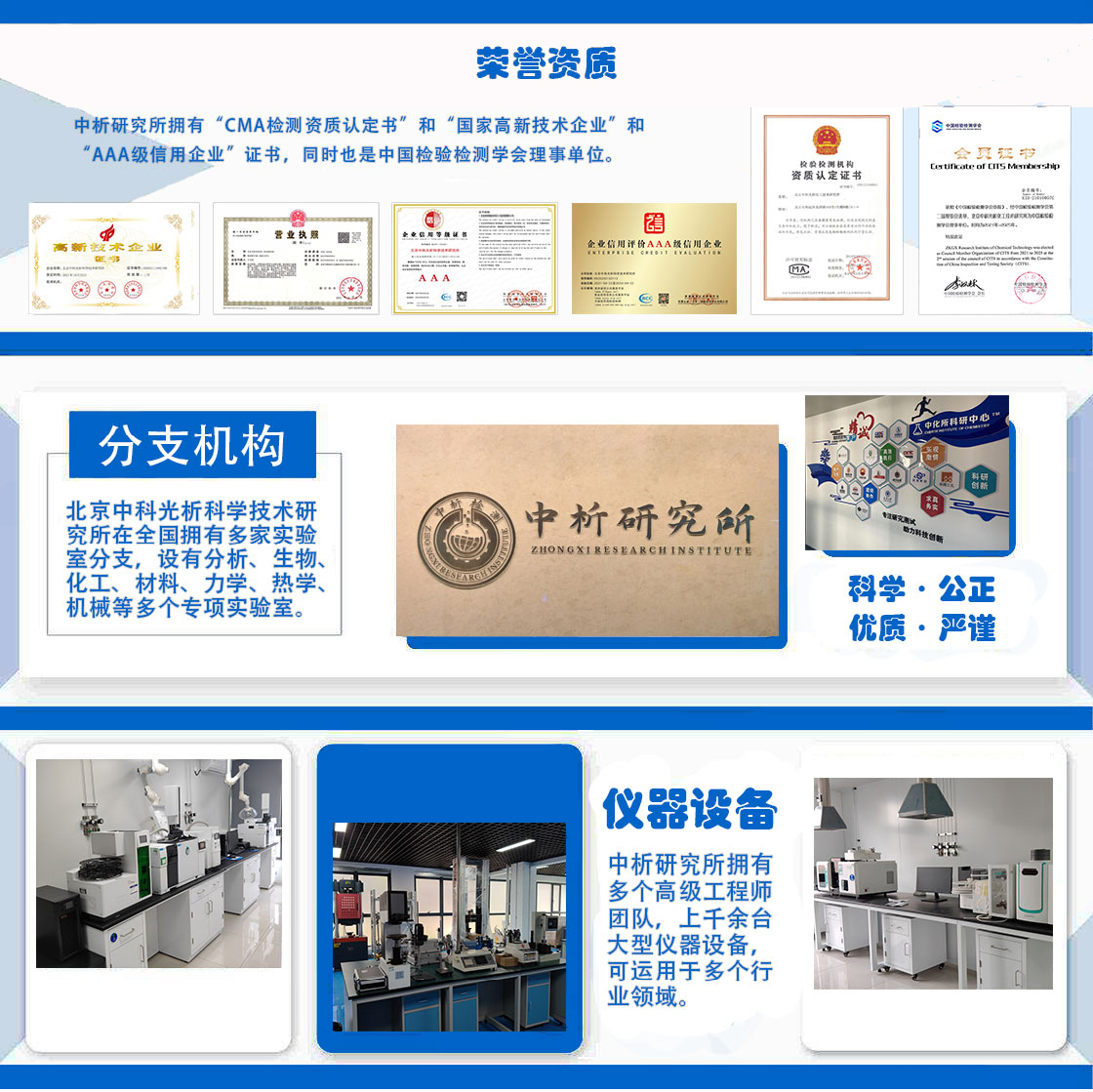
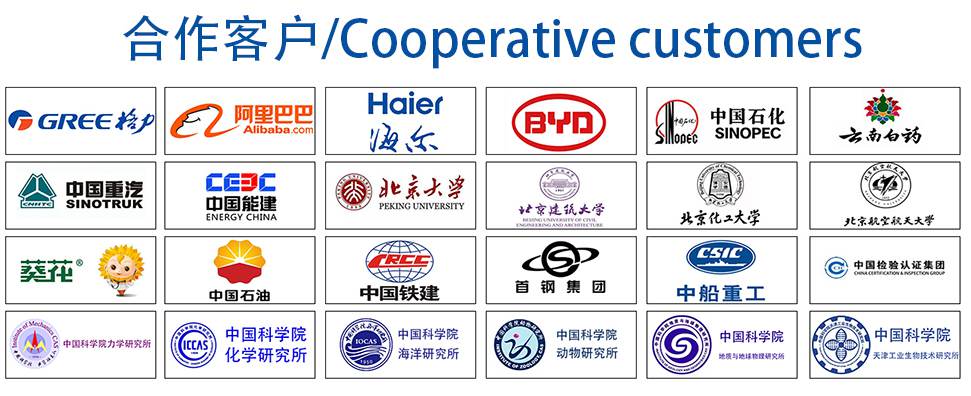