滚动轴承参数检测的重要性
滚动轴承作为机械装备的核心部件,广泛应用于汽车、航空航天、工业设备等领域。其性能直接影响设备运行效率、使用寿命及安全性。据统计,约30%的机械故障源于轴承参数偏差导致的异常磨损或失效。通过系统的参数检测,可精准把控轴承的几何精度、材料性能和运动特性,确保其满足ISO 492、GB/T 307等行业标准要求,同时为故障预测性维护提供数据支撑。
核心检测项目分类
1. 尺寸精度检测
包含内径、外径、宽度等基础尺寸测量,使用精密千分尺、三坐标测量仪(CMM)进行检测,精度需控制在±0.002mm以内。特殊结构的轴承还需检测沟道曲率半径、保持架间隙等参数。
2. 旋转精度检测
采用圆度仪、跳动仪等设备测试径向跳动(ΔR)和轴向跳动(ΔA),其中精密轴承的径向跳动值需≤0.003mm。同步检测端面全跳动和沟位偏差,确保轴承运转平稳性。
3. 游隙参数检测
通过塞尺法、传感器测量法测定径向游隙(Cr)和轴向游隙(Ca)。不同工况对游隙要求差异显著,如深沟球轴承的初始游隙通常设计为0.005-0.02mm,具体需根据预载要求调整。
4. 振动与噪音检测
使用振动分析仪和声级计在标准转速下(如1800r/min)采集振动加速度值(dB)和声压级(SPL)。精密级轴承的振动值需满足V3/V4等级要求,异常高频振动常反映滚道缺陷或润滑失效。
5. 材料及硬度检测
采用洛氏硬度计(HRC)检测套圈和滚动体硬度(通常58-62HRC),金相显微镜分析材料晶粒度(ASTM 8级以上)。同时进行渗碳层深度检测(0.8-1.2mm),确保材料疲劳强度。
6. 润滑性能检测
通过粘度计测量润滑剂运动粘度(40℃时68-100cSt),红外光谱仪检测油液污染度(NAS等级≤8级)。对于密封轴承还需验证脂填充率(20-35%)及密封件耐压性(≥0.05MPa)。
7. 动态特性检测
在轴承试验台上模拟实际工况,检测极限转速(DN值)、额定动载荷(C值)和寿命(L10)。采用热电偶实时监测温升曲线,异常温升(ΔT>45℃)提示设计缺陷或装配问题。
检测技术发展趋势
当前行业正从传统接触式检测向智能化方向发展,激光扫描、机器视觉技术可实现轴承参数的在线实时监测,而基于机器学习的故障诊断系统可提前300小时预测轴承失效。同时,X射线衍射技术(XRD)等非破坏检测方法的应用,使材料应力分析精度提升至±5MPa级别。
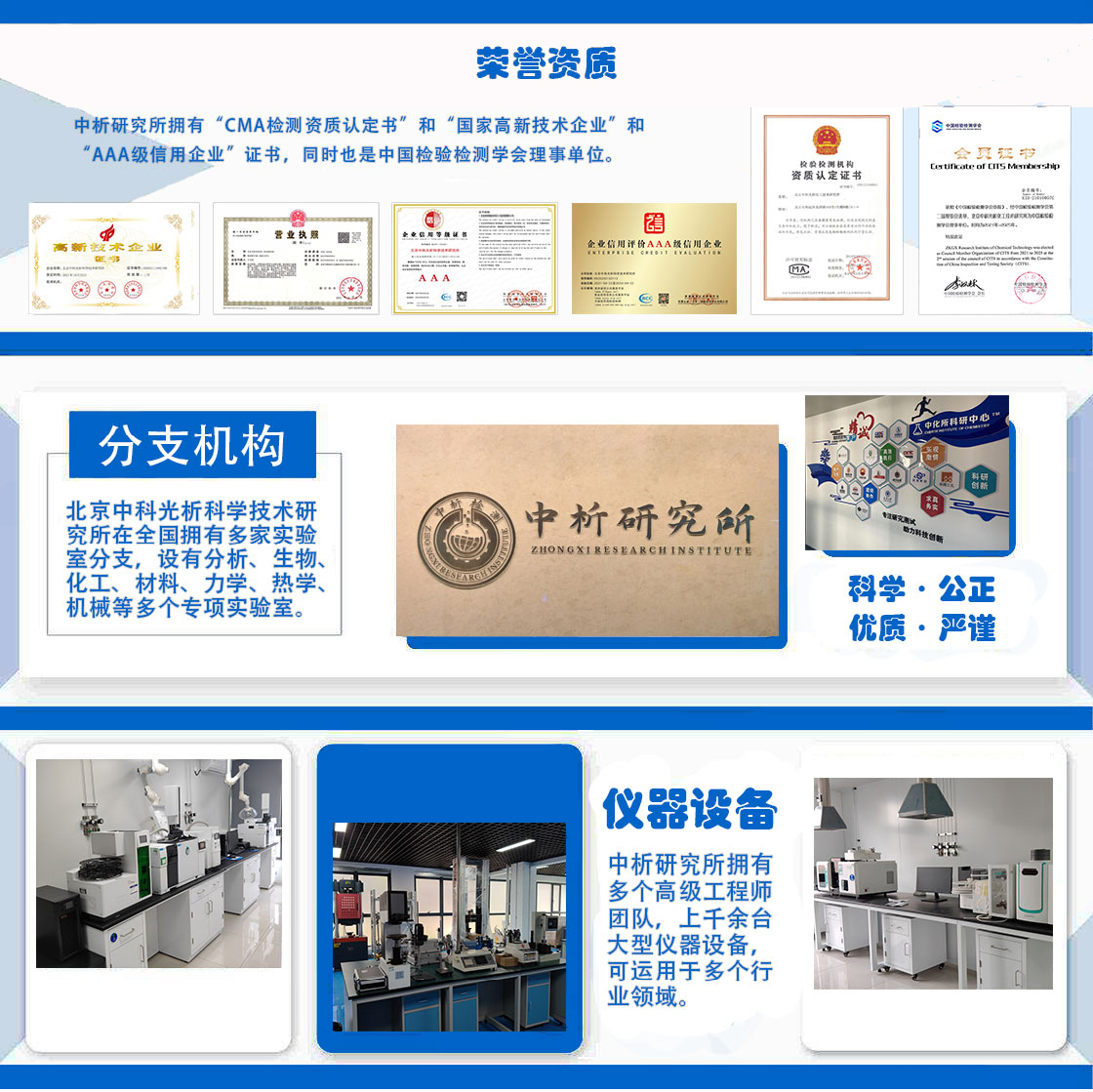
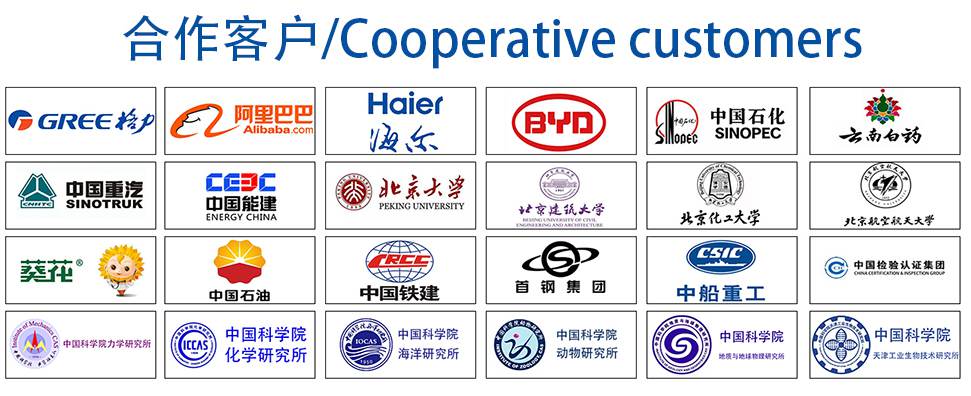