高速摆动自润滑关节轴承检测的重要性
高速摆动自润滑关节轴承是航空、航天、机械设备等领域中动力传递系统的核心部件,其性能直接影响设备运行的稳定性、承载能力及使用寿命。由于这类轴承需要在高速旋转、高频率摆动及复杂工况下保持稳定的自润滑功能,对其材料特性、结构设计及制造工艺提出了严苛要求。为确保其在实际应用中的可靠性,必须通过系统性检测验证其动态性能、润滑效果、抗磨损能力等关键指标,避免因轴承失效导致的设备故障或安全隐患。
主要检测项目及方法
1. 动态负载与摆动性能测试
通过高频试验台模拟实际工况,检测轴承在高速摆动(通常>1000rpm)时的承载能力及运动精度。需记录径向/轴向载荷下的扭矩变化、摆动角度误差及振动频谱,评估轴承的动态稳定性是否符合ISO 14272或GB/T 24610标准要求。
2. 自润滑层摩擦系数检测
采用四球摩擦试验机或专用摩擦磨损仪,测定轴承在干摩擦与边界润滑状态下的摩擦系数。重点观察润滑膜在连续摆动中的保持能力,并通过SEM分析磨损表面形貌,验证聚四氟乙烯(PTFE)复合材料等自润滑层的均匀性与附着力。
3. 温升与热稳定性试验
在恒温箱内进行加速寿命测试,监测轴承在连续运行中的温度变化曲线。利用红外热像仪捕捉局部热点,分析材料热膨胀对间隙配合的影响,确保工作温度不超过润滑层分解阈值(通常<260℃)。
4. 耐腐蚀与密封性能验证
通过盐雾试验(ASTM B117)评估轴承在恶劣环境下的耐蚀性,同时利用氦质谱检漏法检测密封结构的泄漏率。对于航空应用场景,还需增加真空冷焊倾向性测试,确保极端温度下的功能完整性。
5. 微观结构与材料成分分析
采用EDS能谱分析、X射线衍射(XRD)等技术,检测基体金属的晶粒度、表面硬化层深度及润滑材料成分比例。结合金相显微镜观察轴承滚道表面粗糙度(Ra≤0.2μm),确保制造工艺符合图纸设计要求。
检测标准的综合应用
需整合ASTM F1820(关节轴承标准)、SAE AS81820(航空轴承规范)等行业标准,结合具体工况制定检测方案。例如,航空领域需额外增加疲劳寿命测试(>10^7次循环),而工业机器人关节轴承则更关注重复定位精度(±0.01mm)的长期稳定性。
通过上述多维度的检测体系,可全面评估高速摆动自润滑关节轴承的综合性能,为产品选型、质量改进及故障诊断提供科学依据,有效延长设备维护周期并降低运维成本。
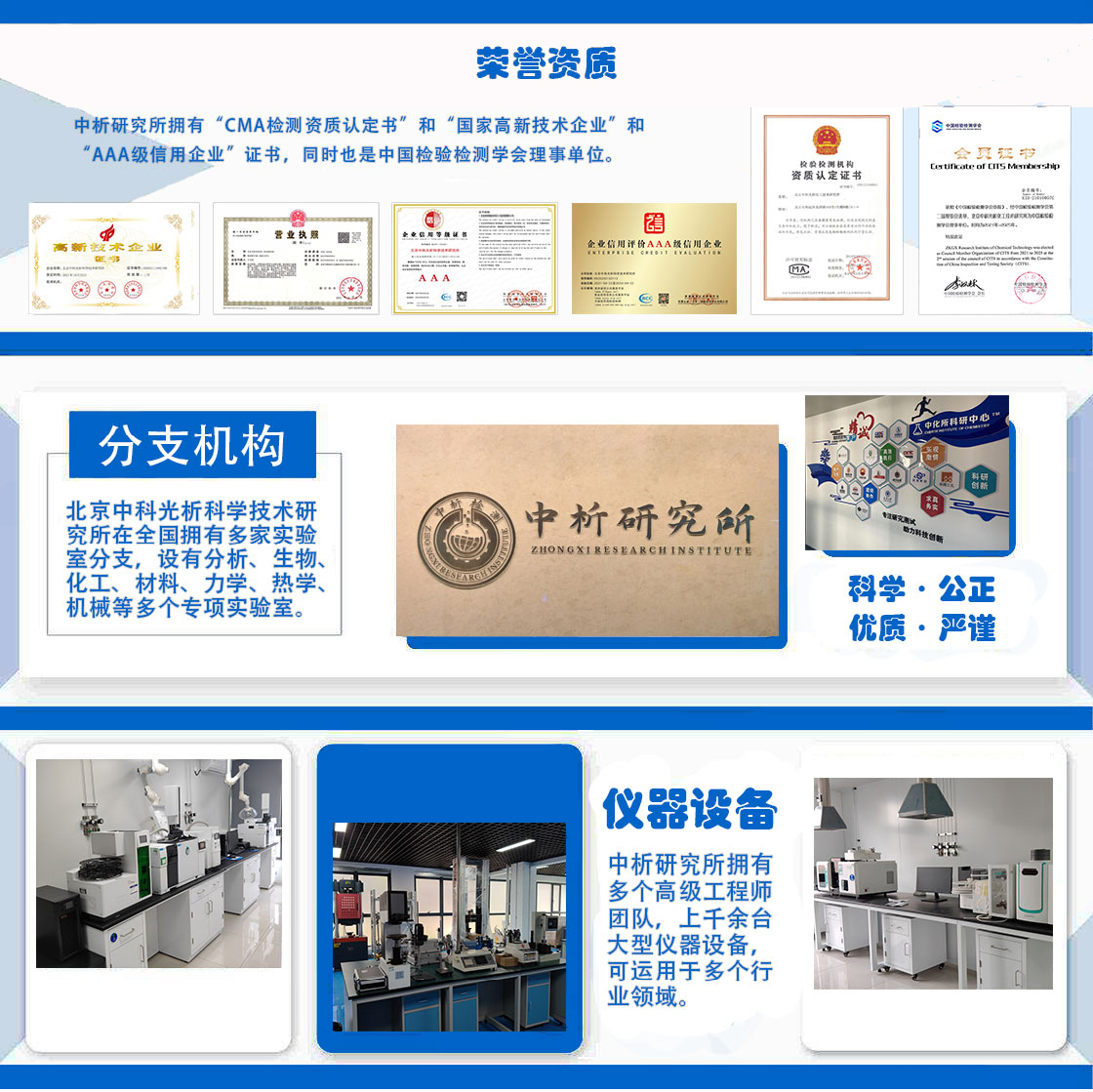
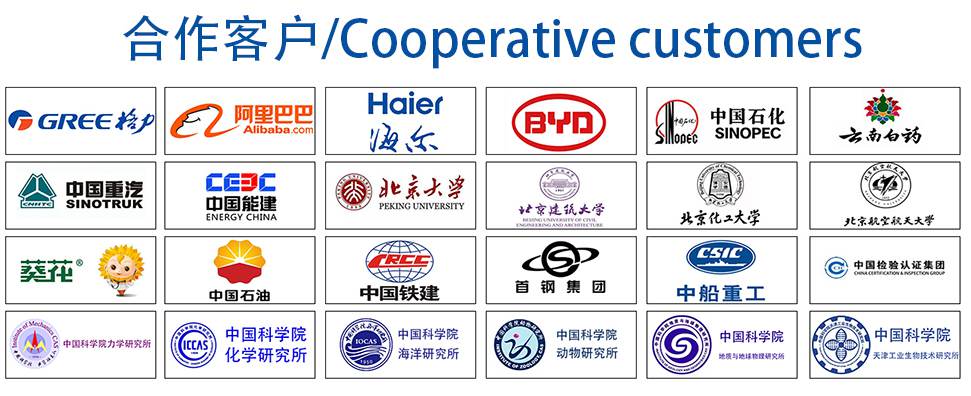