精密数控卧式车床与车削中心检测的核心价值
在高端装备制造领域,精密数控卧式车床和车削中心作为复杂零部件加工的核心设备,其性能直接关系到航空航天、汽车制造、精密模具等行业的加工精度与生产效率。随着现代制造业对μ级甚至纳米级精度的严苛要求,系统性检测成为确保设备稳定性、延长使用寿命的核心环节。通过科学的检测流程,可精准识别设备误差源,优化切削参数,降低废品率,为高附加值产品提供技术保障。
几何精度检测体系
几何精度检测是评价设备基础性能的首要环节,包含主轴系统、导轨系统及传动系统的综合检测。关键项目包括:主轴径向/轴向跳动(ISO 230-1标准)、滑板移动直线度(激光干涉仪测量)、X/Z轴垂直度(方形规配合千分表)、尾座轴线与主轴同轴度(三点接触法)。对于车削中心还须检测B/C轴回转定位精度(球杆仪测试),确保多轴联动时空间轨迹的几何一致性。
位置精度与动态性能检测
通过激光干涉仪执行ISO 230-2标准的位置精度检测,测量内容包括各轴定位精度、重复定位精度及反向间隙补偿。动态检测则聚焦于加减速特性(圆度测试)、伺服系统响应频率(频响分析)以及多轴联动轮廓精度(NAS 979标准试件加工)。特别针对车削中心的动力刀具系统,需验证换刀重复定位精度(≤0.005mm)和刀具端面跳动(≤0.008mm)。
热稳定性与振动分析
构建温度-形变关联模型,采用红外热成像仪监测主轴温升曲线(连续8小时空载试验),通过位移传感器记录关键部件的热膨胀量。振动检测涵盖主轴箱固有频率分析(FFT频谱仪)和切削工况下的振动烈度检测(三向加速度传感器),确保设备在宽频域范围内的动态刚性。
智能化检测技术拓展
近年兴起的数字孪生技术为设备检测开辟新路径,通过植入式传感器网络实时采集振动、温度、电流等多维度数据,结合AI算法实现磨损预测与精度补偿。例如利用数字双轴自准直仪进行在线导轨磨损量监测,或通过声发射技术识别刀具崩刃等异常工况,显著提升检测时效性与预测准确性。
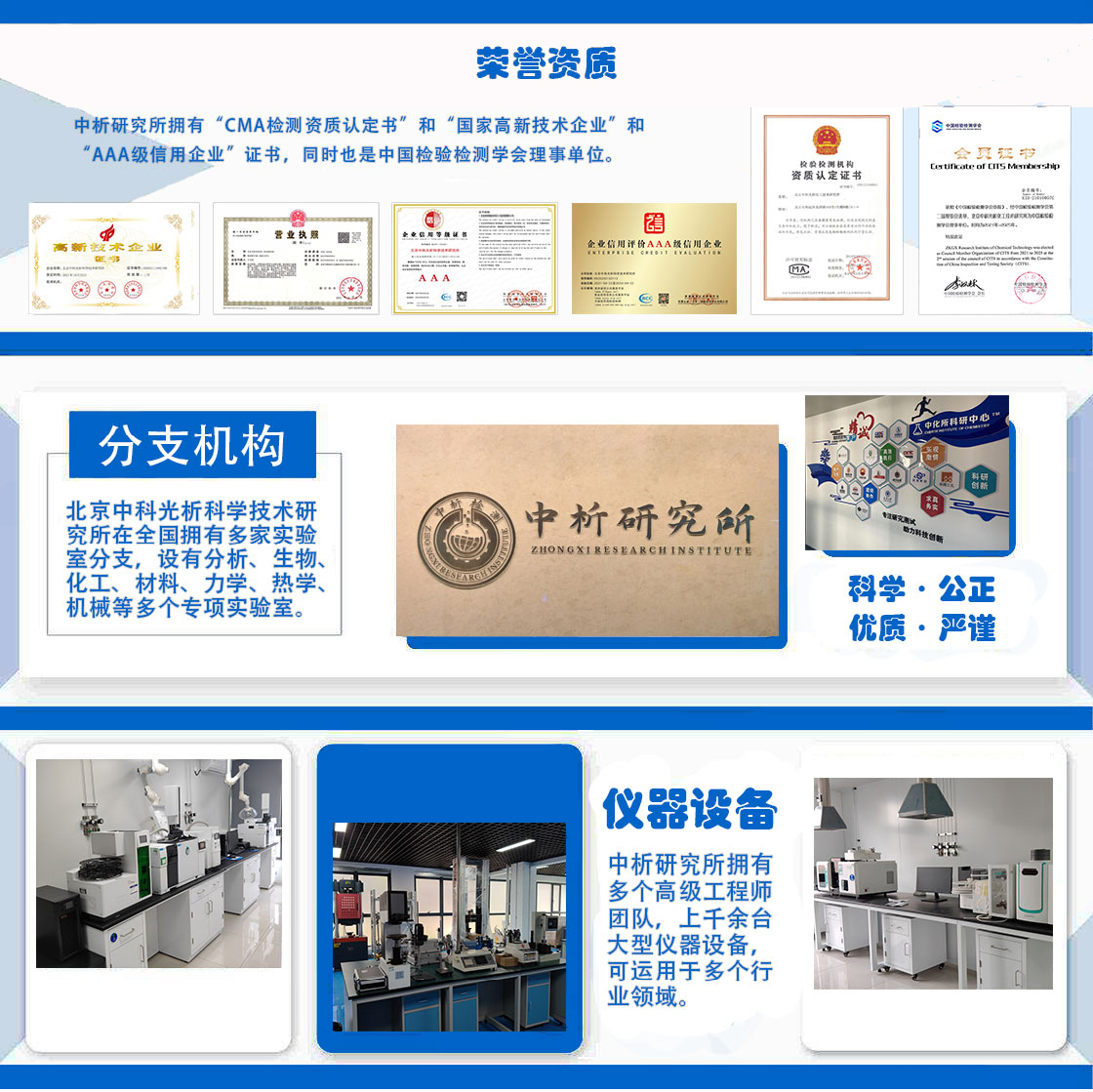
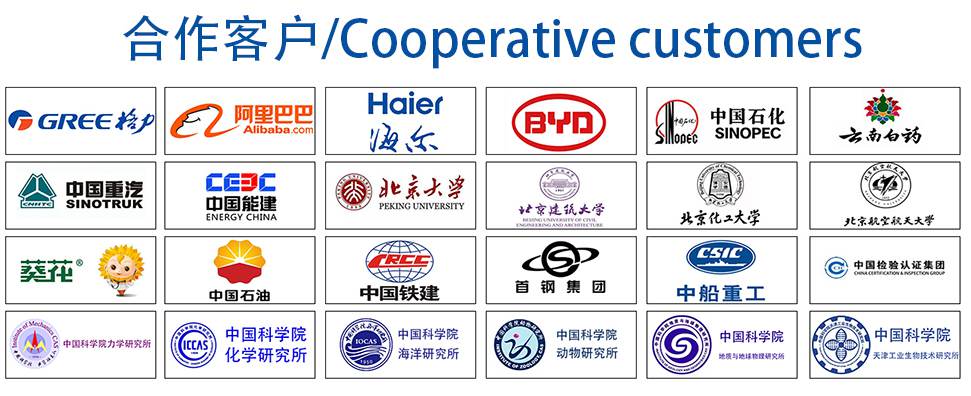