加工中心检测项目全解析
加工中心作为现代精密制造的核心设备,其性能直接影响产品质量和生产效率。为确保设备处于最佳状态,定期开展系统性检测已成为企业质量管理的关键环节。通过覆盖机械、电气、软件等多维度的检测项目,能够精准定位潜在问题,延长设备寿命,提升加工精度稳定性。下文将详细阐述加工中心检测的核心项目及其实施要点。
一、基础几何精度检测
几何精度是加工中心的核心性能指标,包含三大类检测内容:1) 主轴轴线与工作台面的垂直度检测,使用高精度直角规配合千分表测量;2) 各直线轴运动平行度检测,通过激光干涉仪进行全程误差补偿;3) 旋转轴重复定位精度测试,需在标准温度下完成至少10次循环测量。
二、动态性能检测
动态性能反映设备实际加工能力,重点检测项目包括:1) 主轴最大转速稳定性测试,需连续运行2小时监测温升和振动值;2) 多轴联动轨迹精度检测,使用球杆仪绘制空间误差补偿曲线;3) 快速进给加减速性能测试,记录G00指令下的实际运动曲线与理论值的偏差。
三、热变形误差检测
针对长期运行的加工中心,热误差检测至关重要:1) 主轴热伸长量监测,通过非接触式位移传感器连续采集4小时数据;2) 机床结构温度场分布检测,布置不少于20个热电偶点;3) 热对称性分析,对比设备冷态与热态下关键几何参数的差异度。
四、功能安全测试
安全性能检测保障操作人员和设备安全:1) 急停系统响应时间测试,要求触发后0.5秒内完全制动;2) 防护门联锁功能验证,模拟13种异常开门场景;3) 过载保护装置灵敏度检测,需加载120%额定载荷进行实效测试。
五、数控系统功能验证
包括PLC程序逻辑测试、NC代码编译正确性验证、补偿参数有效性检测三大模块。重点验证反向间隙补偿、螺距误差补偿、刀具半径补偿等核心功能的实施效果,确保补偿后定位精度达到ISO 230-2标准要求。
检测方法与周期建议
建议采用三级检测体系:日常点检(每班次)、月度精度校验(激光校准)、年度全面检测(含机械磨损量评估)。对于高精密加工场景,推荐每2000小时进行主轴动平衡检测,并使用三维探头开展空间精度标定。
通过科学规范的检测流程,企业可将加工中心精度损失控制在0.005mm/年以内,有效降低因设备状态异常导致的废品率。检测数据应建立数字化档案,为预防性维护提供数据支撑,最终实现加工质量与生产效率的双重提升。
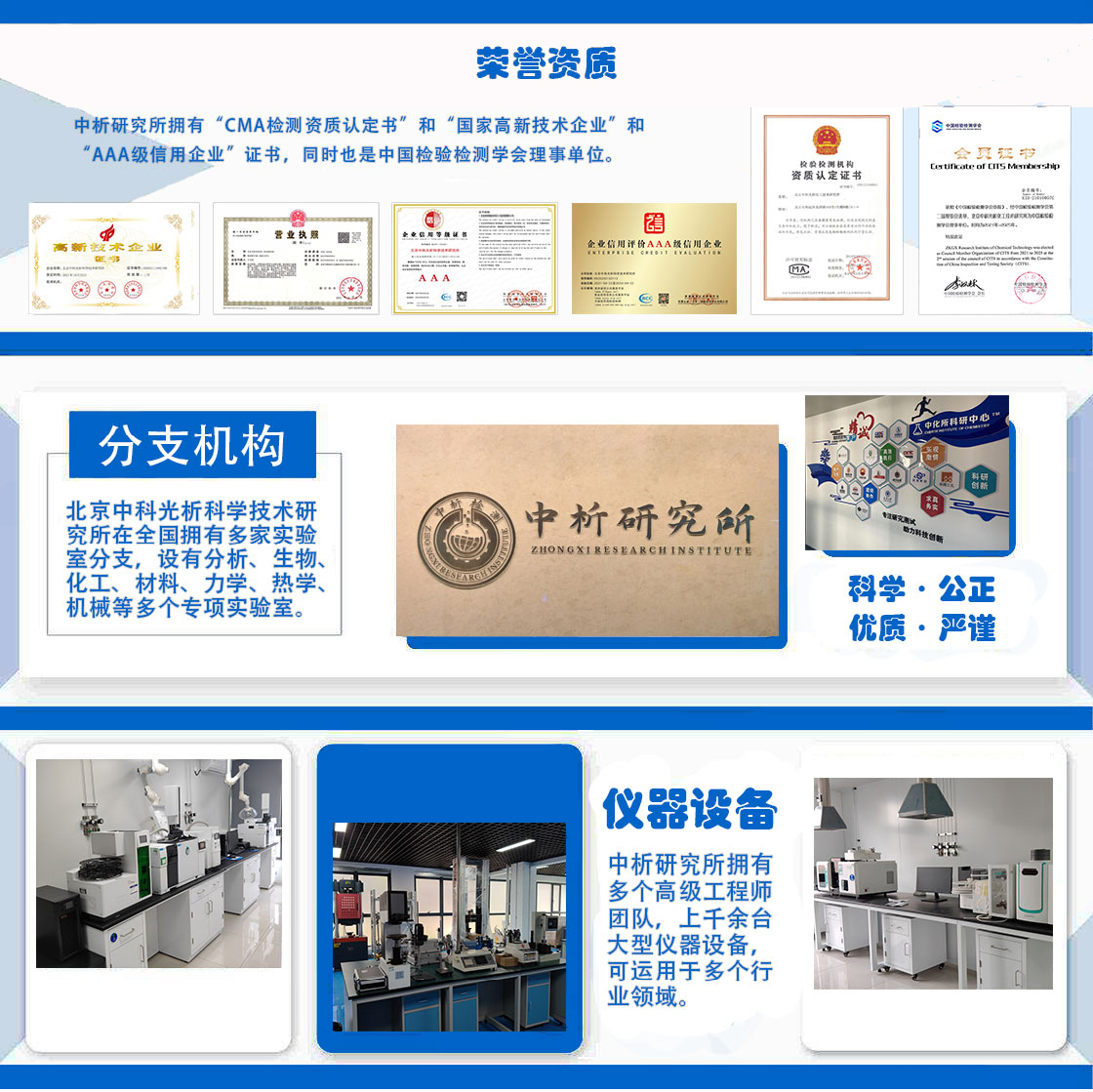
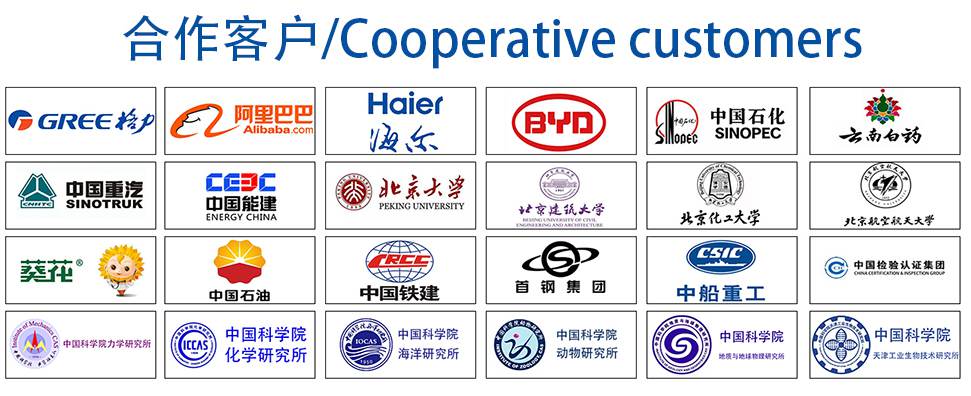