蜗杆磨床检测的重要性与核心项目解析
蜗杆磨床作为精密传动部件加工的核心设备,其加工精度直接影响蜗轮蜗杆副的传动性能。在航空航天、数控机床、汽车制造等领域,蜗杆磨床需要通过系统化检测来保障±0.002mm级加工精度的稳定性。规范的检测流程不仅能预防批量加工缺陷,更能延长设备使用寿命,降低企业运维成本。
六大核心检测项目体系
1. 主轴系统精度检测
使用千分表测量主轴径向跳动(≤0.003mm),通过激光干涉仪检测轴向窜动(≤0.002mm)。重点监控主轴温升对精度的影响,连续运行4小时温升应≤25℃。
2. 蜗杆齿形误差检测
采用三坐标测量仪进行螺旋线误差检测(精度需达DIN 3级),使用专用蜗杆检测仪测量齿距累积误差(≤0.008mm)。对于大模数蜗杆需进行接触斑点检测,有效接触面积应≥85%。
3. 砂轮系统动态平衡
运用动平衡仪确保砂轮组件残余不平衡量≤1.5g·mm/kg,检测时需模拟实际工作转速(通常1500-4000rpm)。每次更换砂轮后必须进行动态平衡校正。
4. 机床位置精度验证
按照ISO 230-2标准进行定位精度检测,X/Y/Z轴重复定位精度应≤0.005mm。采用球杆仪检测圆度轨迹误差(≤0.015mm),特别关注蜗杆螺旋角方向的运动精度。
5. 冷却液系统效能检测
测量冷却液流量(≥20L/min)、压力(0.3-0.5MPa)及过滤精度(≤25μm)。定期进行PH值检测(8.5-9.5),监控防锈剂浓度变化对加工表面质量的影响。
6. 数控系统参数校验
检查电子齿轮箱(EGB)传动比设定误差(≤0.001%),验证主轴同步功能精度。通过试切标准试件检测蜗杆导程误差(≤0.005mm/100mm),确保软件补偿功能有效。
检测周期与数据管理建议
日常检测应包含开机前主轴预热检测(30分钟)和加工后精度复检。建议每月进行系统性精度验证,每季度开展预防性维护检测。建立数字化检测数据库,采用SPC统计过程控制方法分析精度衰减趋势,实现预测性维护。
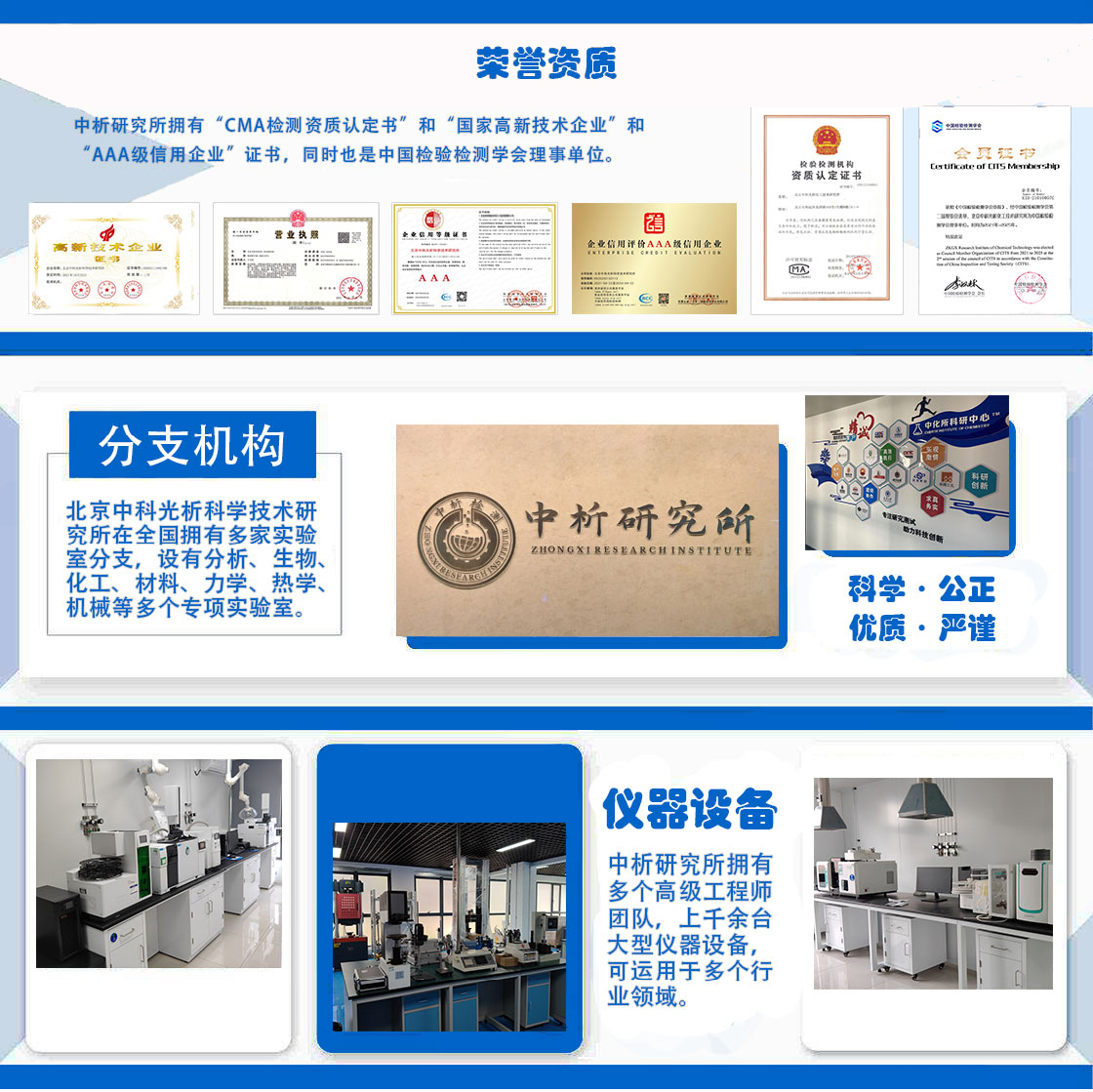
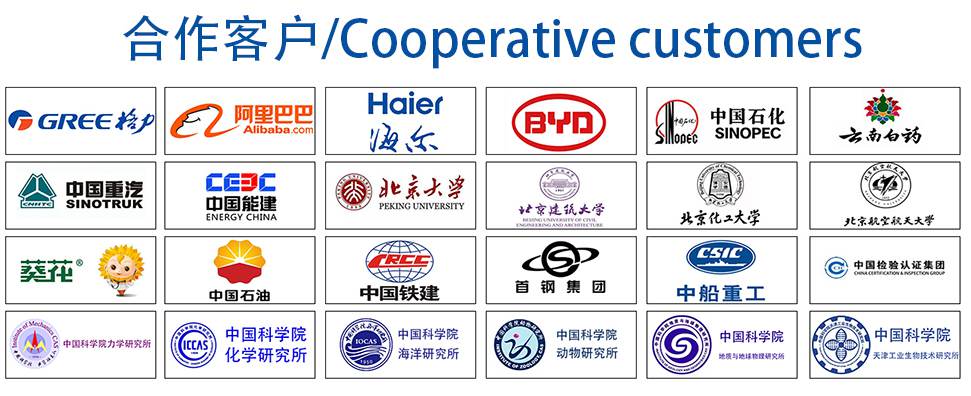